Noise error rate, E noise error, Rate – Delta RMC151 User Manual
Page 920: Noise error, E noise error rate
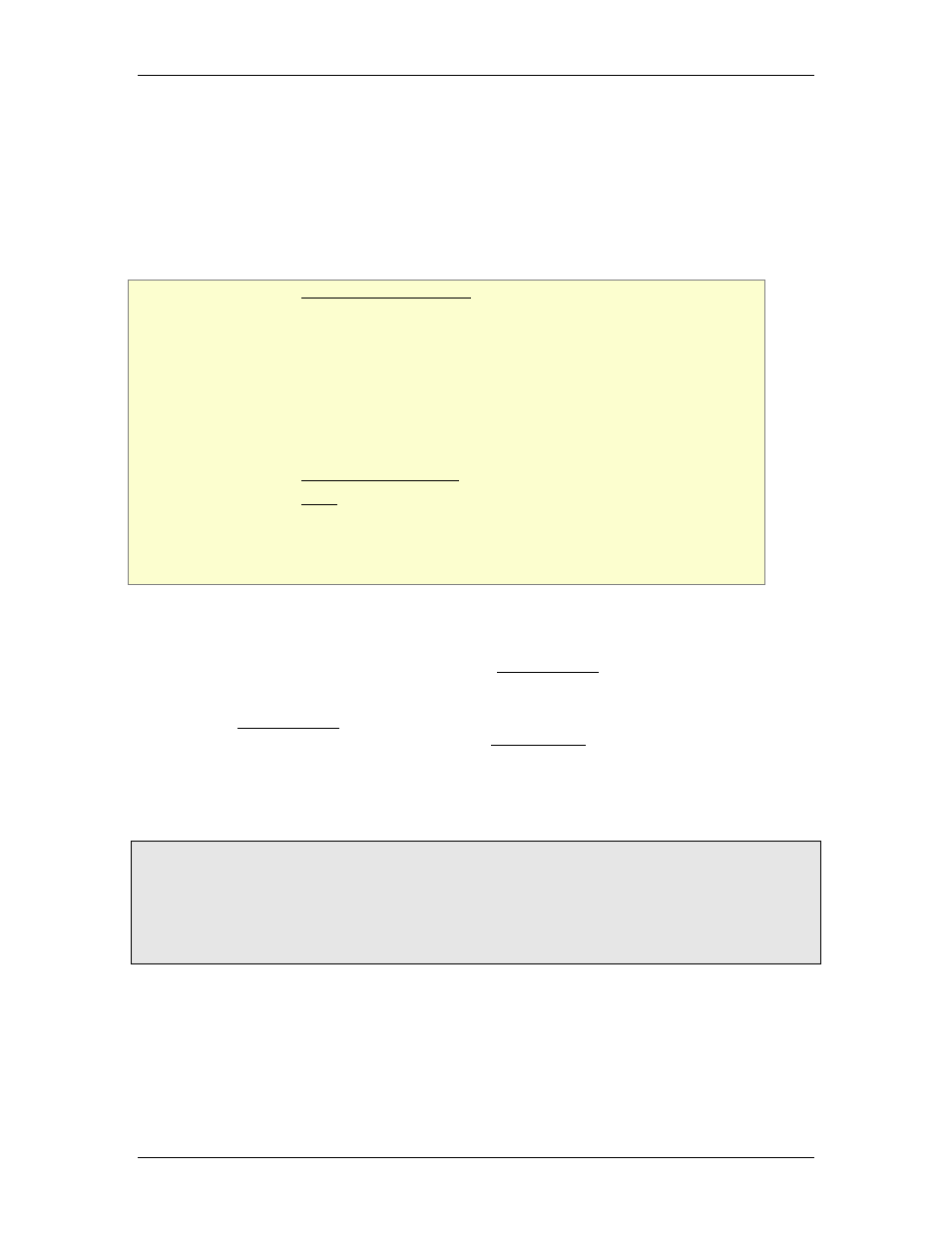
RMC70/150 and RMCTools User Manual
If an axis is considered stopped when the velocity is exactly zero, it would be impossible
for it to ever be considered stopped, since there is always noise in real-life systems. For
example, perhaps a system (scaled in inches) has velocities up to 0.08 in/sec when it's
standing still. Setting the Stop Threshold to 0.1 in/sec will let you know when the axis is
stopped.
9.2.2.2.16. Noise Error Rate
Type: Axis Parameter Register
RMC70 Address: Primary Input: %MDn.6, where n = 12 + the axis number
Secondary Input: %MDn.24, where n = 12 + the axis number
RMC150 Address: Primary Input: %MDn.6, where n = 24 + the axis number
Secondary Input: %MDn.24, where n = 24 + the axis number
System Tag: Primary Input: _Axis[n].NoiseErrorRate
Secondary Input: _Axis[n].SecNoiseErrorRate
where n is the axis number
How to Find: Axes Parameters Pane, All tab: Feedback
Data Type: REAL
Units: See Below
Range: ≥ 0
Default Value: 1000
Description
This parameter is designed to specify the noise detection on the feedback. It is primarily
designed for MDT inputs, but also works well for analog voltage or current inputs. If a
large change in the feedback is detected, the Noise Error bit will be set.
The Noise Error Rate defines the maximum allowable rate of change in the feedback of
the axis. If the rate of change exceeds the Noise Error Rate for more than 3 loop times,
then the Noise Error bit will be set. If the Noise Error bit becomes set, it may cause a Halt
if so configured by the Auto Stops and if the Direct Output Status bit is off. During noise
less than 3 loop times, the Actual Position (or the value measured by the axis' input) is
estimated to allow recovery from electrical noise.
Make sure to set the Noise Error Rate to a value much higher than the maximum
expected rate of change in the axis' units. For example, if the axis will be traveling at up
to 200 pu/s, then set the Noise Error Rate to something much higher, such as 800.
Note:
The Noise Error bit may turn on because the Noise Error Rate parameter is set too low. The
Noise Error Rate should be set to a value much higher than the expected velocity (or rate of
change of pressure or force) of the axis. If your axis is experiencing Noise Errors, this is the
first item you should check. Setting the Noise Error Auto Stop to Status Only to avoid halting
due to an overly low Noise Error Rate parameter can cause significant control problems,
because the Actual Position and Actual Velocity may still be incorrectly calculated.
Quadrature Inputs
The Noise Error Rate parameter does not apply to quadrature axes. Instead, if the RMC
detects an illegal transition (both A and B signals transition simultaneously), or an
overspeed condition (pulse frequency exceeds maximum specifications), a Noise Error will
occur.
Units
900
Delta Computer Systems, Inc.