Tuning position-pressure or position-force, Tuning a position-pressure, Or position-force system – Delta RMC151 User Manual
Page 63
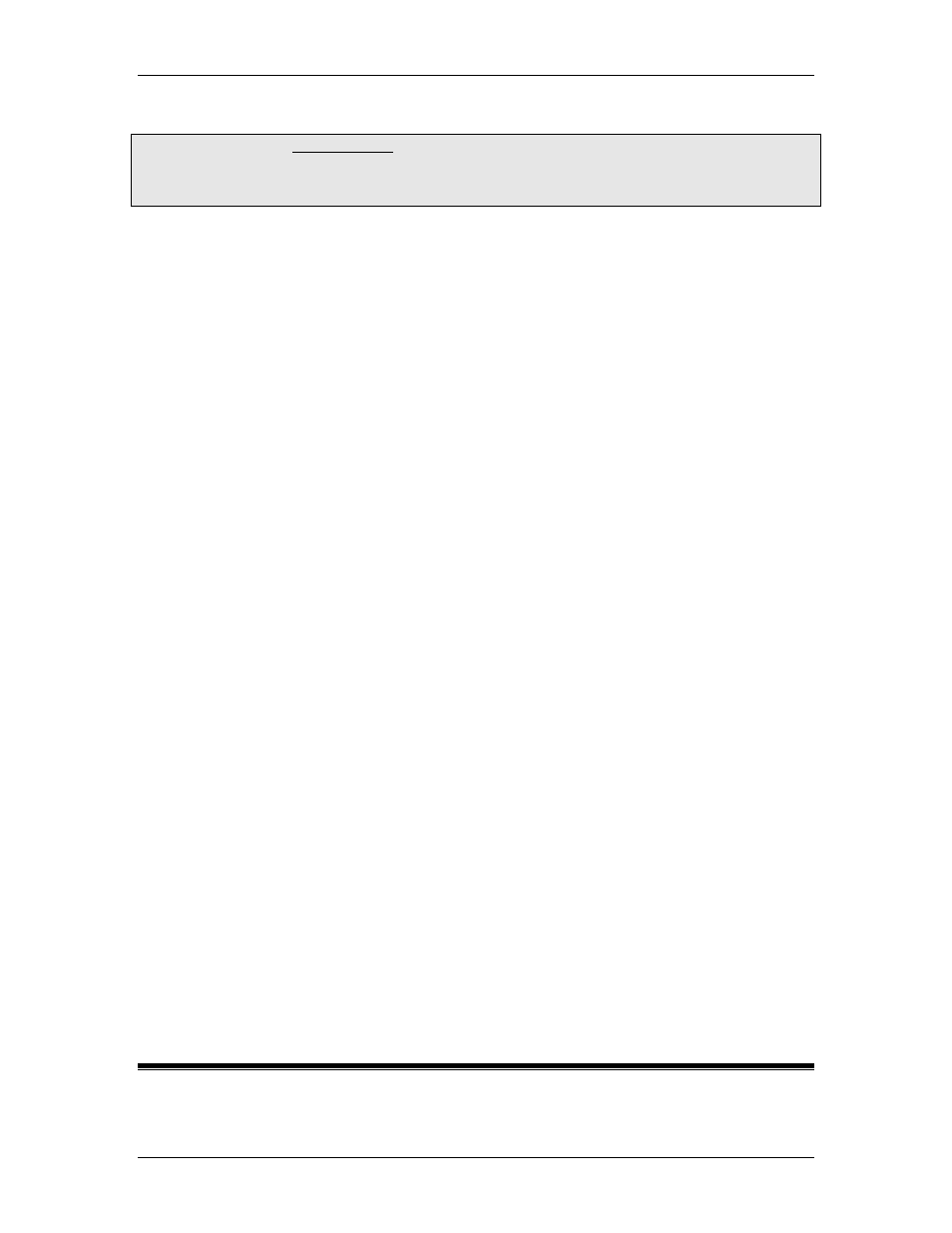
2 Starting Up the RMC
3. Change the gain.
Tip: You can use the Tuning Wizard to calculate a model and use the Gain Calculator to
choose gains. After uploading a plot of pressure or force control, where the axis is controlling a
changing pressure or force, click the Tuning Wizard.
If you use the Tuning Wizard, you do not need to continue manually changing the gains.
5. Adjust the Feed Forwards
Pressure/Force Rate Feed Forward
Ramp the pressure/force, and adjust the Pressure/Force Rate Feed Forward. Start with a
small value. The Pressure/Force Rate Feed Forward should help the Actual
Pressure/Force track the Target Pressure/Force during the ramp. Your system may not
need any Pressure/Force Rate Feed Forward.
Pressure/Force Feed Forward
Most systems do not require the Pressure/Force Feed Forward. If your system exerts a
pressure or force that is roughly linear to the amount of Control Output, you may need
the Pressure/Force Feed Forward. To tune the Pressure/Force Feed Forward, move the
Target Pressure/Force to various values, and adjust the Pressure/Force Feed Forward
while the Target Pressure/Force is stationary. Do this for several value of pressure/force
to ensure the best Pressure/Force Feed Forward.
6. Re-adjust the Proportional and Integral
Ramp the pressure/force, and re-adjust the proportional and integral gains. This should
make it track better.
7. Adjust the Differential Gain
If you need better control, add some Differential Gain. The Differential Gain is typically a
couple orders of magnitude less than the Proportional Gain.
8. Fine-tune the System
The final tuning of the system should be made at the rate and pressure/force range of
intended operation. Look for following errors, overshoot, or oscillations, and consider the
following:
•
Should the system seem a little sloppy, try adjusting the Proportional Gain.
•
If the actual pressure lags or leads the target position during the entire constant
velocity section of the move, adjust the Feed Forwards.
•
If an Output Saturated error occurs, there is not enough drive capacity to drive the
axis at the requested rate of pressure/force change. Should this occur, increase the
Ramp Time or decrease the speed of the system.
•
If the Control Output is not high, the gains can probably be increased for better
control, depending on system stability.
•
Adding or changing the pressure/force feedback filter may help if noisy feedback is
suspected.
2.3.8. Tuning a Position-Pressure or Position-Force
System
deltamotion.com
43