Tuning a motor in torque mode – Delta RMC151 User Manual
Page 66
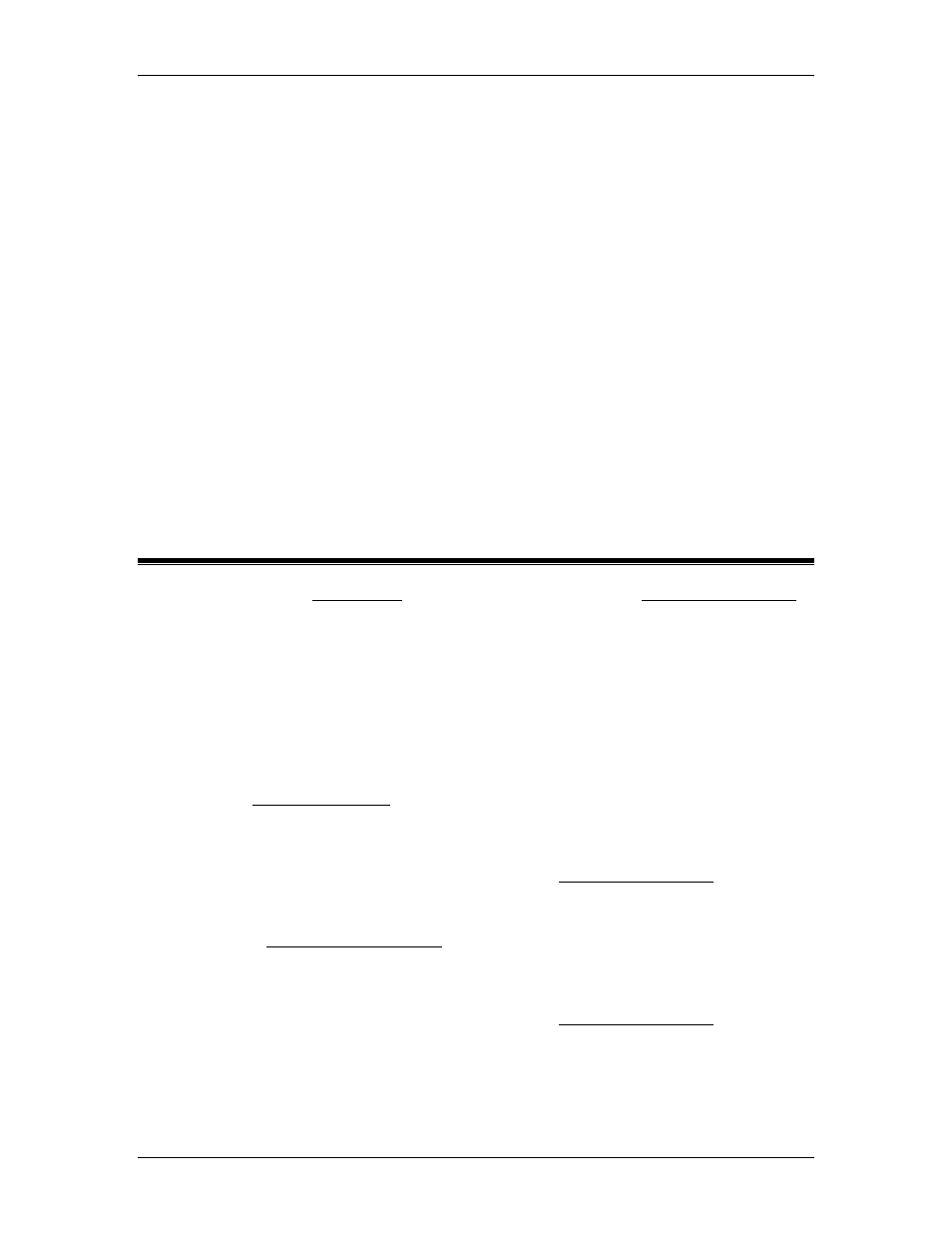
RMC70/150 and RMCTools User Manual
Issue the commands for transitioning between position and pressure/force as you intend
to do during normal machine operation. For some applications, this may involve creating
a simple user program.
View the transition on a plot. If the pressure/force drops off at the transition, increase the
Integrator Preload parameter in the Enter Pressure/Force command.
10. Fine-tune the System
The final tuning of the system should be made at the rate and pressure/force range of
intended operation. Look for following errors, overshoot, or oscillations, and consider the
following:
•
Should the system seem a little sloppy, try adjusting the Proportional Gain.
•
If the actual pressure lags or leads the target position during the entire constant
velocity section of the move, adjust the Feed Forwards.
•
If an Output Saturated error occurs, there is not enough drive capacity to drive the
axis at the requested rate of pressure/force change. Should this occur, increase the
Ramp Time or decrease the speed of the system.
•
If the Control Output is not high, the gains can probably be increased for better
control, depending on system stability.
•
Adding or changing the pressure/force feedback filter may help if noisy feedback is
suspected.
2.3.9. Tuning a Motor in Torque Mode
When tuning a motor in torque mode, use the basic instructions in the Tuning a Position Axis
topic, but use the order of the gains below.
Tuning Order
Torque motors generally do not have much damping. Damping must be provided for the
system, or it will be difficult to control. Providing some Differential Gain will effectively
dampen the system. Therefore, the Differential Gain must be set early in the tuning
process:
Method 1:
a. Set all the gains to zero.
b. Increase the Proportional Gain to the point where the motor moves somewhat when
given a Move Absolute (20) command. You should notice that the axis has a tendency
to overshoot.
c. Increase the Differential Gain so that the axis ceases overshooting. If the axis begins
oscillating or chattering, decrease the Differential Gain.
d. Continue tuning the gains in the order given in the Tuning a Position Axis topic.
Method 2:
a. Set all the gains to zero.
b. Issue the Hold Current Position (5) command to the axis.
c. Increase the Differential Gain until the motor start humming (or chattering or
oscillating), then decrease the Differential Gain significantly, perhaps up to 50%, to
avoid oscillation later when making moves.
d. Continue tuning the gains in the order given in the Tuning a Position Axis topic.
Small Motors
For very small motors that can be rotated by hand, the Differential gain can be set before
any other gains.
46
Delta Computer Systems, Inc.