Delta RMC151 User Manual
Page 818
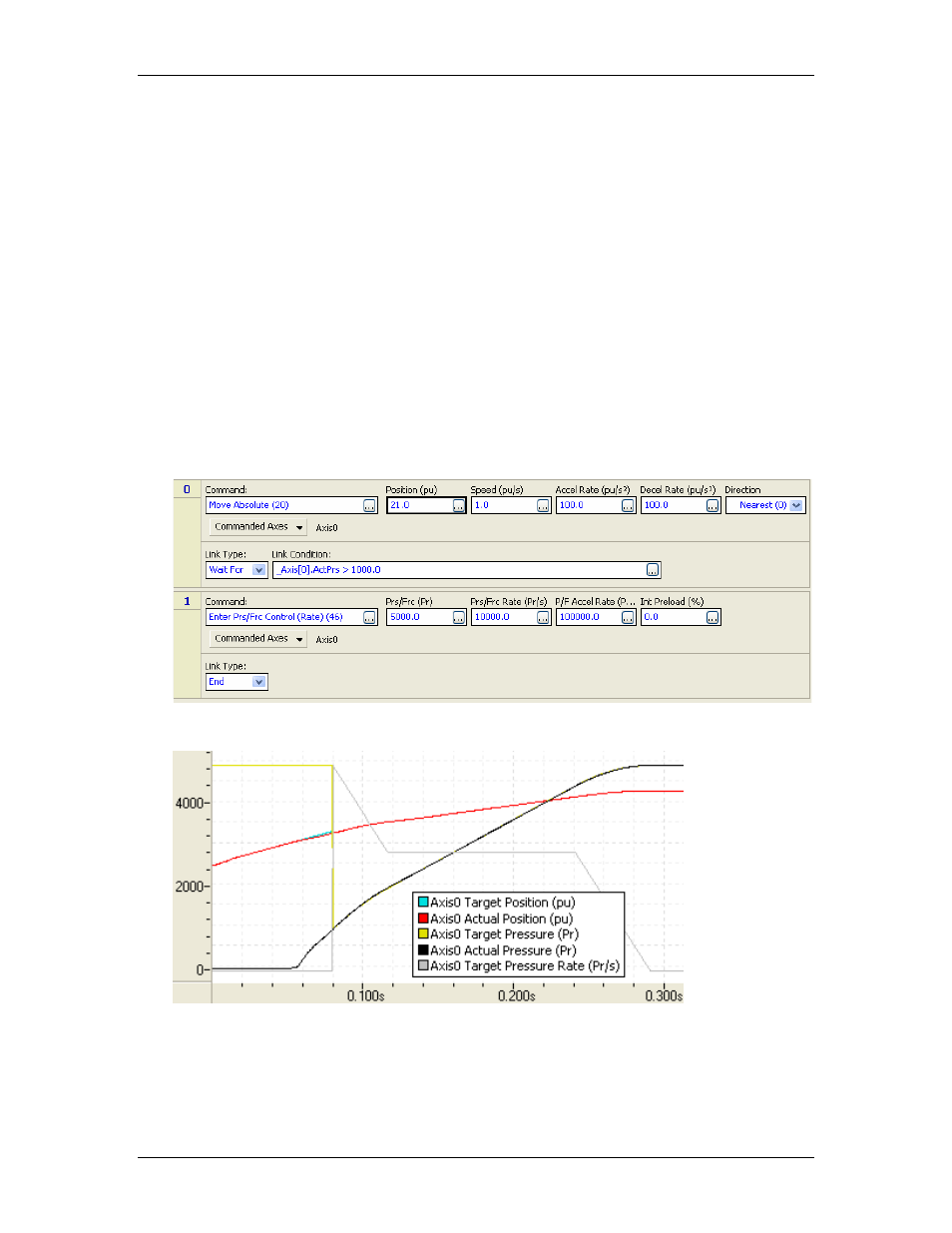
RMC70/150 and RMCTools User Manual
If the Pressure/Force Accel Rate is zero, the Pressure/Force will immediately begin
changing at the specified Pressure/Force Rate.
Upon entering pressure or force control, the Target Pressure/Force will be set to the
Actual Pressure/Force. The Target Pressure/Force will then be ramped to the Requested
Pressure/Force at the specified Pressure/Force Rate.
The Integrator Preload specifies the value that the Integral Output Term should be set
to when transitioning into pressure/force control. The Preload is specified as a percentage
of the Output Scale (typically 10V), and is not affected by the pre-transition integrator
state. Typically, this can be left at the default value of 0. If the pressure/force exhibits a
drop upon entering pressure/force, increase this value to help smooth the transition.
Example
Consider a hydraulic press that must move toward the material to be pressed, transition
to pressure control and hold a certain pressure.
The user program below shows a possible sequence of steps.
Step 0 issues a Move Absolute command to move the axis to a position beyond where it
expects to encounter the material. The Step 0 Link Type waits for the Actual Pressure to
exceed 1000, then it goes to Step 1 which issues an Enter Pressure/Force Control (Rate)
command. The axis will transition to pressure control and go to the Requested
Pressure/Force of 5000.
The plot below shows the transition:
At the beginning of the plot, the position is increasing. At approximately 0.55 seconds,
the Actual Pressure starts increasing. When the Actual Pressure reaches 1000 at
approximately 0.8 seconds, the Enter Pressure/Force Control command is issued, the axis
transitions to pressure control, and then the Target Pressure ramps to 5000. Notice that
the Target Pressure Rate decelerates to the specified rate and then decelerates to zero,
stopping at the requested pressure.
798
Delta Computer Systems, Inc.