Delta RMC151 User Manual
Page 118
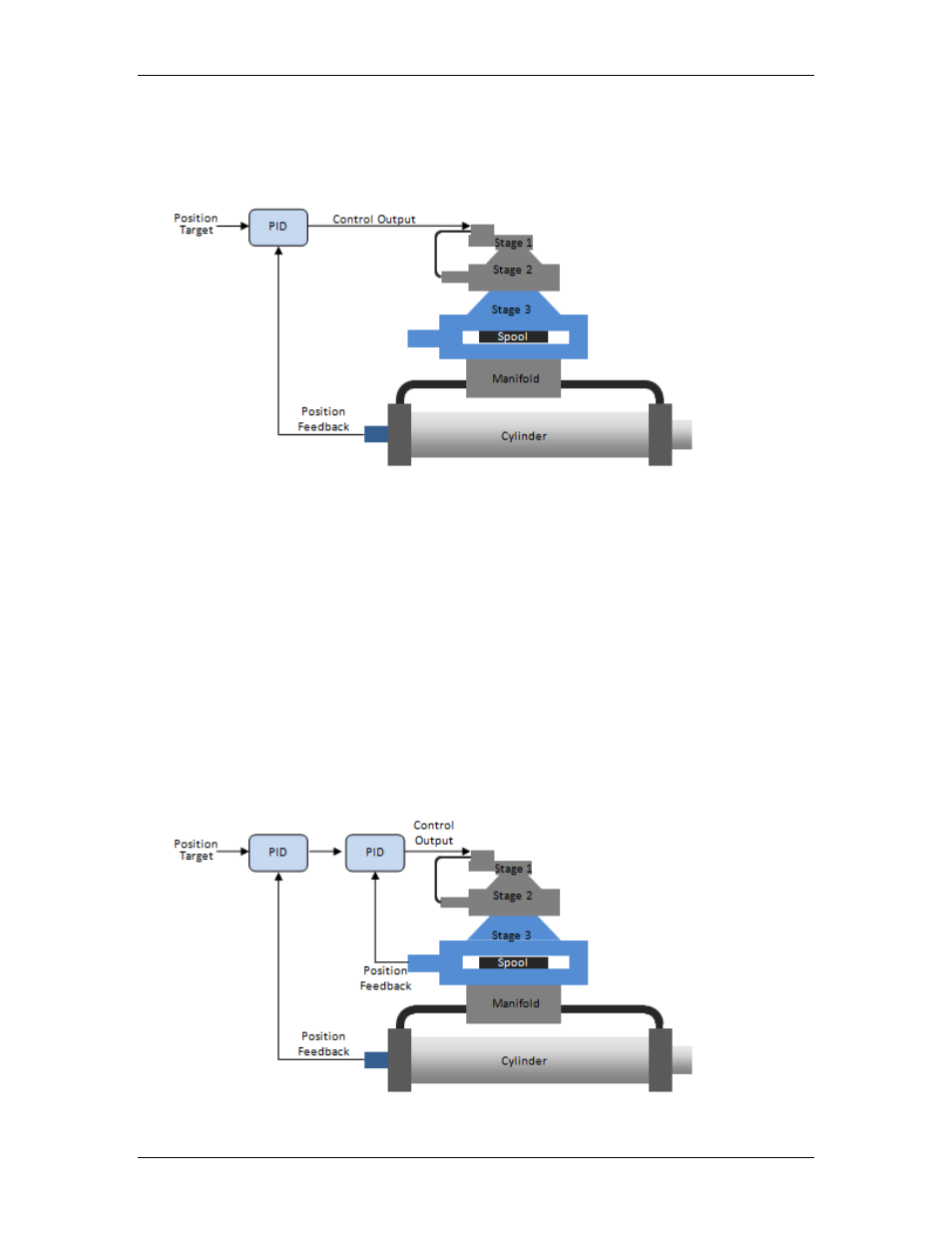
RMC70/150 and RMCTools User Manual
The ultimate goal of the cascaded loops is to control the end process. Cascade control can
provide precise control for certain difficult systems, for example systems in which some
lag time exists.
To better understand cascade control, consider the following example in hydraulic motion
control:
The figure above shows a very large hydraulic cylinder with a 3-stage proportional valve.
The goal is to control the cylinder position.
The first two valve stages have internal electronic controls, and all we need to know
about them is that the first two stages will produce a velocity on the third stage that is
roughly proportional to the Control Output signal received by the valve. The third stage
has no electronic controls.
A standard PID control loop can be applied to this system, as shown in the figure.
However, this results in poor control. The valve spool responds very quickly compared to
the cylinder. Therefore, when the Position Target of the system (the desired position of
the cylinder) changes, the valve spool will immediately move over its full length of travel,
while the cylinder has barely begun moving, and when the actual position eventually
catches up to the target, the spool will immediately move back the full length, and in that
way, the system can begin to oscillate and will result in poor control.
A better method is to apply an additional inner PID loop to the valve in a cascaded
configuration, as shown in the figure below. This requires spool position feedback from
the third stage of the valve. The valve will then provide a much more linear flow in
relation to the Control Output, which will make the outer position PID much easier to tune
and will provide better control.
Cascade Control Advantages
98
Delta Computer Systems, Inc.