Command: sine start (72), Sinusoidal, Sine start (72) – Delta RMC151 User Manual
Page 774
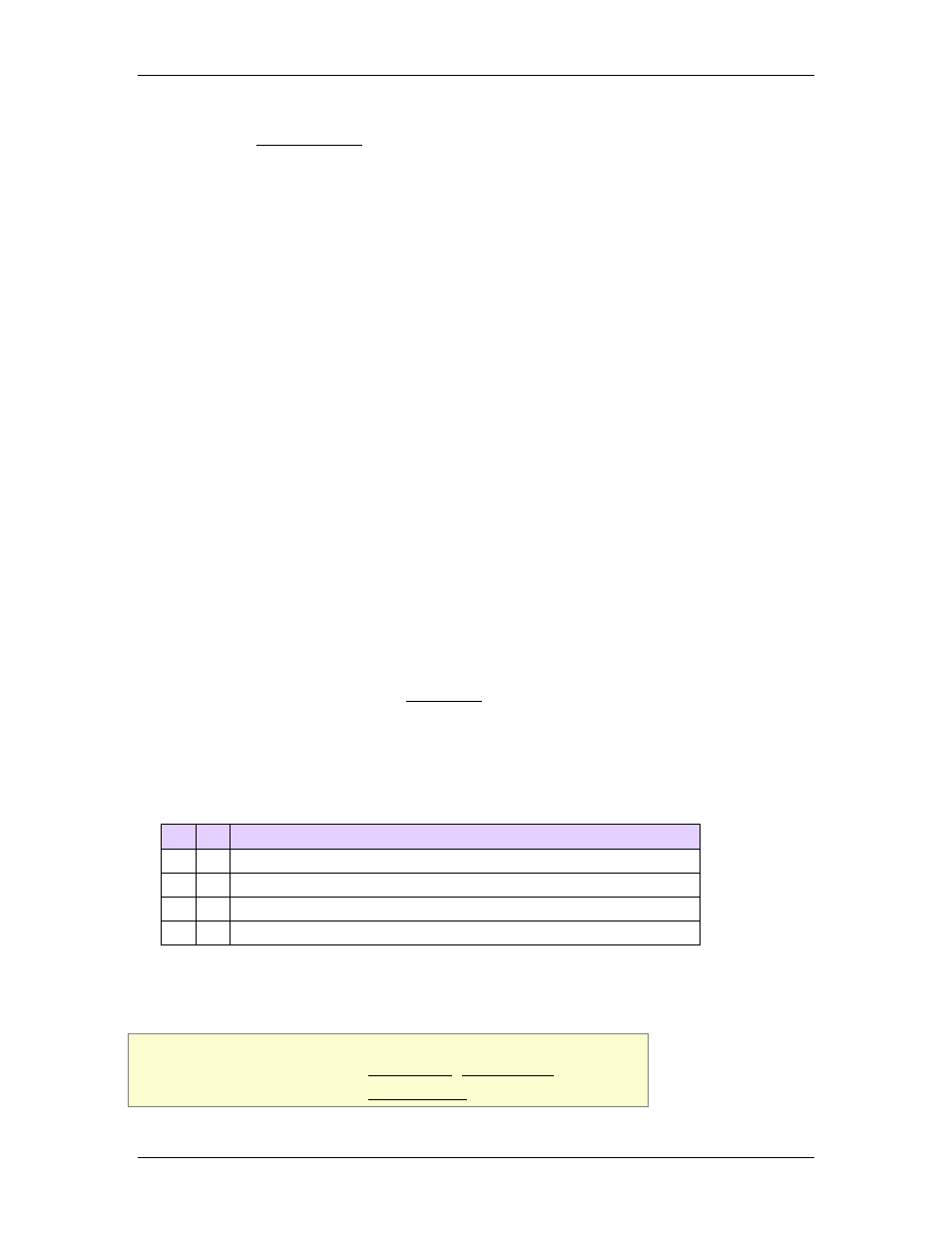
RMC70/150 and RMCTools User Manual
This command specifies a profile in terms of speed versus position. The RMC compares
the current Target Position with the Requested Position and computes a target profile
that reaches the Requested Velocity at the Requested Position. Once the Requested
Position (and therefore Requested Velocity) is reached, the Done status bit will be set.
If the Requested Velocity was non-zero, the target generator will continue at the final
Requested Velocity indefinitely. This command is a closed loop control command.
Notice that it is difficult to determine exactly how long the move will take. This command
will attempt to move the axis using the shortest path possible and will attempt to make
the Target Acceleration non-zero during the entire move.
If the Requested Position is behind the Actual Position at the time this command was
issued, a Command Error or Runtime error will be set. "Behind" refers here to being in
the direction opposite to the current direction of travel. Similarly, if the axis is stopped,
the Requested Velocity must be positive if the Requested Position is greater than the
current position, and negative if the Requested Position is less than the current
position.
Why Bother?
This command is good when you want to specify the ends, not the means. There are two
applications where this really works well:
•
When you suddenly want to stop at a certain position, but do not know what
deceleration rates you need. Maybe you usually use a deceleration of 100 in/s
2
, but if
the axis is travelling fast close to the position where you want to stop, the decel rate
of 100 might not be enough to stop you fast enough. If you issue a Speed at Velocity
(36) command with a Requested Velocity of zero, the RMC will calculate the
deceleration for you and will get you stopped at the requested position. Note that if
you issue this command a long distance before you stop, the calculated decelerations
may be so low that it takes a long time to stop.
•
Injection molding applications often specify the speed relative to the position. You can
set up a user program that issues this command for each trigger point, and it will go
to the Requested Velocity at the position.
Target Generator State Bits
The Target Generator bits in the Status Bits register indicate which portion of the move
the axis is currently in. These bits are useful when programming complex motion
sequences.
Target Generator Done bit
This bit indicates the move is complete, which occurs when the Target Position has
reached the Requested Position.
Target Generator State A and B bits
B
A Description
0
0
The target generator is complete
0
1
Acceleration
1
0
Constant Velocity
1
1
Deceleration
8.4.7.2. Command: Sine Start (72)
Supported Axes: Position Control Axes
Supported Control Modes: Position PID, Position I-PD
Firmware Requirement: 2.30 or newer
754
Delta Computer Systems, Inc.