Motion, Synchronizing axes – Delta RMC151 User Manual
Page 120
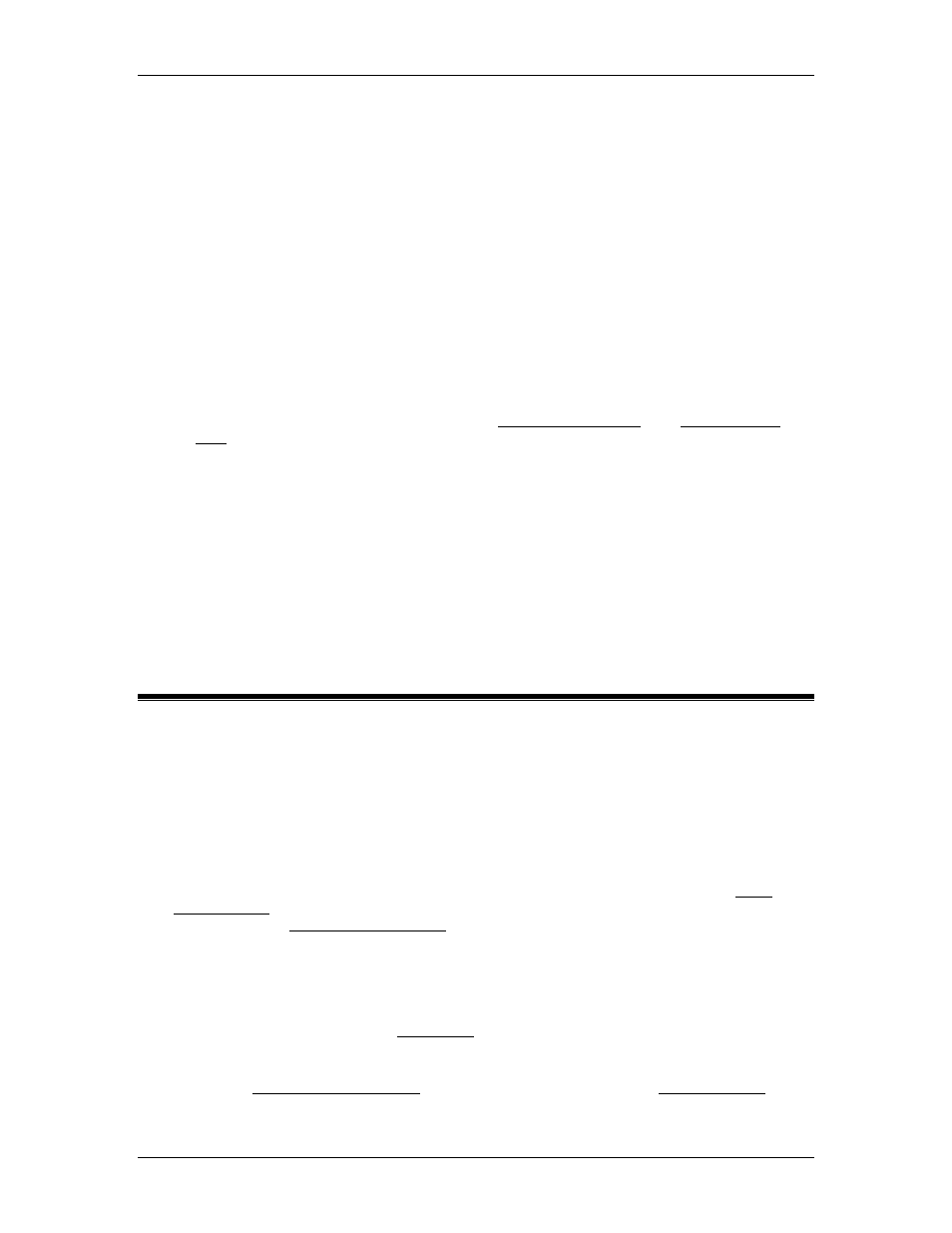
RMC70/150 and RMCTools User Manual
4. Set up Outer Loop Axis
Set up the outer loop axis, including scale/offset and tuning. During closed loop
control of the outer loop (including during tuning), make sure that the inner loop axis
remains in closed-loop control and geared to the PDIF output of the outer loop axis. If
the inner loop halts, you will need to put in closed loop control again and restart the
Gear Absolute. You should make sure the AutoStops and tolerances for the inner loop
are set to avoid unnecessary halts.
Using Cascade Control
Once both loops of the cascade control have been set up and tuned, the system can be
controlled by sending motion commands to the outer loop axis. There are a few items to
consider:
•
Control Order
The inner loop must always be in closed-loop control when the outer loop is controlling
the system. When manually controlling the inner loop, the outer loop should be in
open loop control.
•
Starting Up the System
Every time the system starts up, send the Transition Rate (56) and Gear Absolute
(25) commands to the inner loop axis. Then you can begin controlling the outer loop
axis.
•
Error Handling
You need to consider error handling between the axes. For example, if the inner loop
axis halts, the outer loop axis must halt. If the outer loop axis halt, the inner loop does
not necessarily need to halt.
3.6. Motion
3.6.1. Synchronizing Axes
In motion control, the term synchronization is a very general term. In the most general sense,
the RMC does everything synchronously, that is, it does things at specific times and responds
to events within a certain amount of time. This topic describes specific types of
synchronization of axes and explains how to achieve them in the RMC.
Identical Motion (Synchronized Identical Positions)
In this type of synchronization, the motion of the axes are identical. For example, two
cylinders on a press always move to the same positions at the same time, and must
always be at the same position during the moves.
To achieve this type of synchronization, issue identical commands (such as the Move
Absolute (20) command) to each axis simultaneously. To issue the commands
simultaneously, create a user program and put the commands in the same step. Or, from
a PLC issue identical commands to all axes in the same write.
Keeping the axes in sync:
To keep the axes from getting out of sync, do the following:
•
Put all Axes in the Same Halt Group
Put all the axes in the same Halt Group. If one axis in the halt group halts, then all
axes in the group will halt.
•
Set the Position Error Tolerance
Set the Position Error Tolerance for each axis. This will cause the Following Error bit to
turn on when the Actual Position comes too far away from the Target Position. When
100
Delta Computer Systems, Inc.