Error bits register, Error bits, Error bit – Delta RMC151 User Manual
Page 869
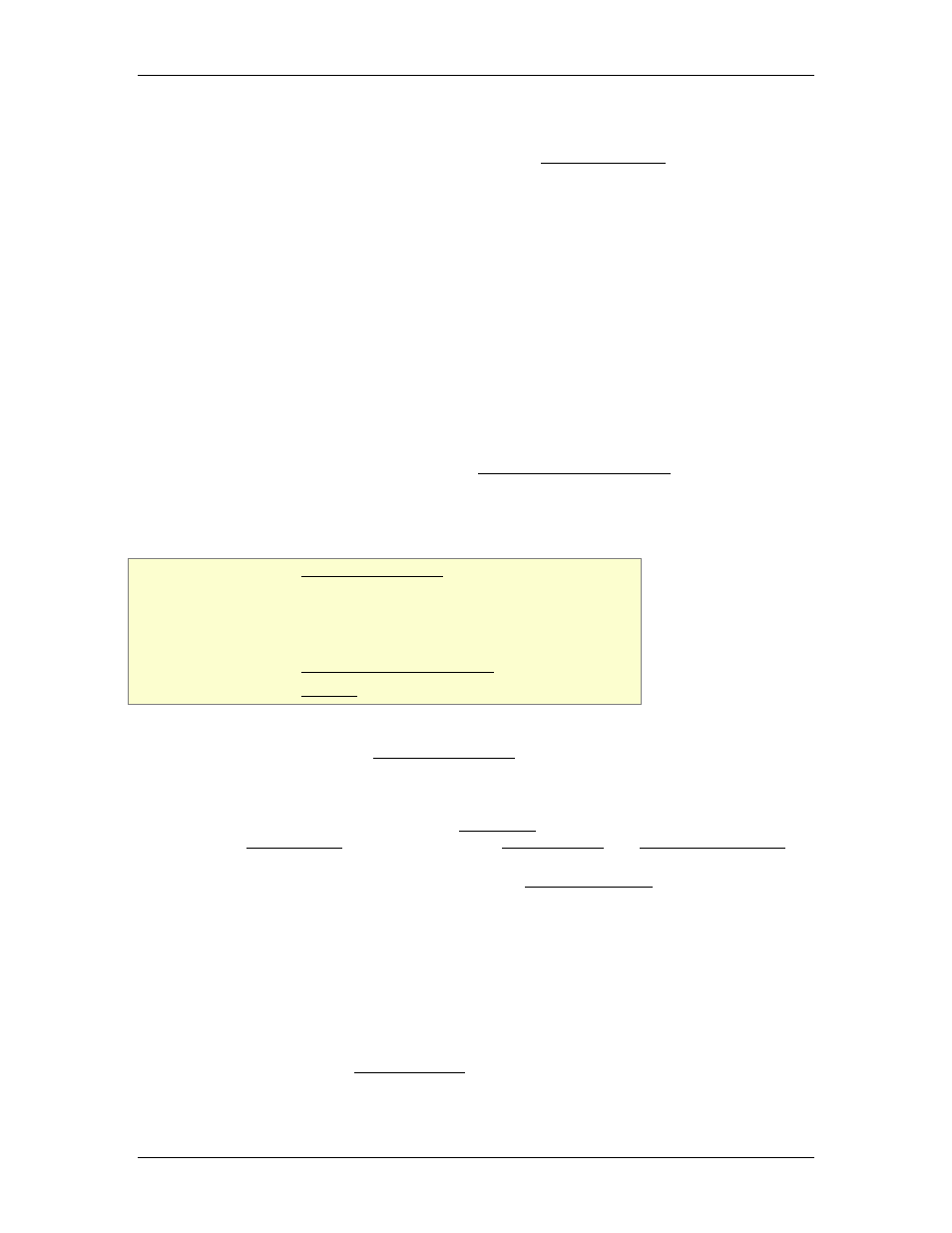
9 Register Reference
This bit indicates that the feedback transducer on the secondary input has no errors.
This bit provides the instantaneous general status of the transducer, and is especially
useful when implementing Custom Feedback. This bit is available in firmware 3.54.0
and newer.
The Secondary Transducer OK bit will be off if the transducer is experiencing any of t
following:
•
Pressure/Force No Transducer
•
Pressure/Force Transducer Overflow
Notice that the Secondary Transducer OK bit is instantaneous. The P/F No Transducer
and P/F Transducer Overflow axis error bits do not necessarily provide the
instantaneous state of the feedback as the Transducer OK status bit does. These thre
error bits will turn on only after the error has existed for three loop times, during whi
time the Input Estimated bit is on. In addition, they will latch on and remain on even
the underlying error has gone away.
31 -
Command Acknowledge Bit
The RMC sets the Command Acknowledge bit to match the Command Request bit of
the last command. This bit is intended to be used for synchronizing a PLC program w
the RMC. See the Command Acknowledge Bit topic for details.
9.2.1.2.2. Error Bits Register
Type: Axis Status Register
RMC70 Address: %MDn.1, where n = 8 + the axis number
RMC150 Address: %MDn.1, where n = 8 + the axis number
System Tag: _Axis[n].ErrorBits, where n is the axis number
How to Find: Axes Status Registers Pane, Basic tab
Data Type: DWORD
Description
The Error Bits register is an Axis Status Register. It is a collection of bits that provide a
summary of the errors on the axis. An error bit is set when certain conditions occur.
Unless otherwise noted, these bits do not clear unless a Clear Faults command or any
other motion command is issued and the underlying error condition has gone away.
When a bit is set, a halt will occur if the Auto Stops are configured to do so and the axis is
not in the Direct Output state. Notice that the No Transducer and Transducer Overflow
Error bits can not be set to Status Only.
When an error bit is set, it will be reported in the Event Log Monitor.
Addressing Error Bits
In RMCTools, individual Error bits can be addressed by appending the bit tag name to
"_Axis[n].ErrorBits.", where n is the axis number. For example,
"_Axis[1].ErrorBits.FollowErr" is the Axis 1 Following Error Bit.
Clearing Error Bits
When an error bit is set, it remains set although the error condition may have
disappeared. For example, if the Control Output saturates, the Output Saturated error bit
will be set and remain set even though the Control Output is no longer saturated.
To clear errors, issue the Clear Faults (4) command. It will clear all the error bits whose
underlying error condition has gone away.
deltamotion.com
849