Runtime error, Command modified, Runtime – Delta RMC151 User Manual
Page 874: Error, S runtime error, Pressure/force no transducer, R pressure/force transducer overflow, Pressure/force transducer overflow, Pressure/force noise error
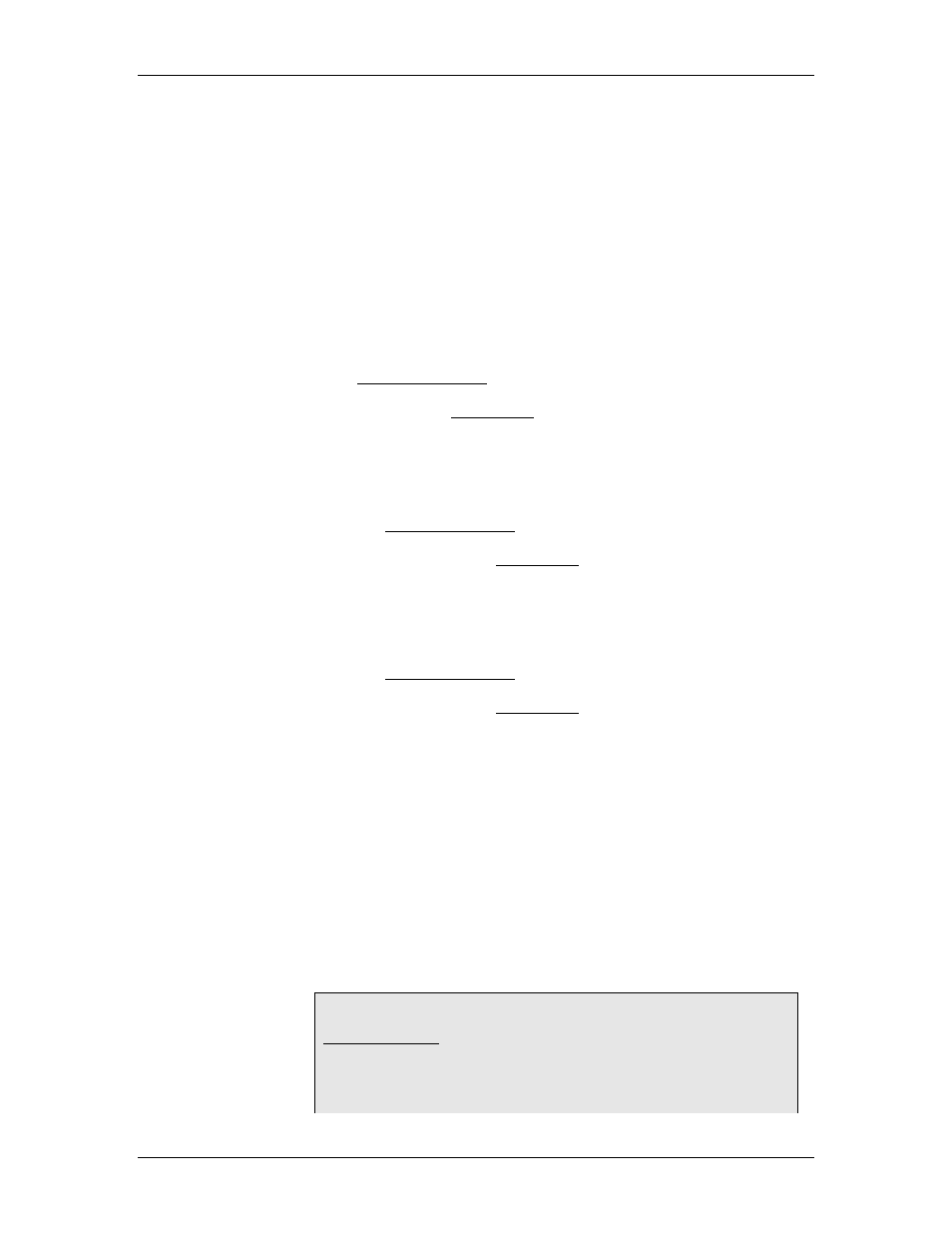
RMC70/150 and RMCTools User Manual
of errors that cause this bit to be set. This bit is cleared
when any valid command is issued.
12
CmdMod
Command Modified
This bit is set when a command has been modified. If a
command contains an invalid Command Parameter, it may
be modified. A command that has been modified will then be
a valid command. For example, it the Requested Position is
beyond the travel limits, the command will be automatically
changed so that it will move to the limit. By default, an axis
will halt when a command is modified. If the Command
Modified Autostop is set to Status Only, then the axis will
not halt and the modified command will be processed as
usual.
When this error occurs, an error number will be stored in the
Last Error Number status register. Depending on the Event
Log filter settings, this error may also be logged to the Event
Log. See the Error Codes topic for a list of errors that cause
this bit to be set. This bit is cleared when any valid
command is issued.
13
CfgErr
Configuration Error
When an attempt is made to write an invalid value to a
parameter, this bit is set and an error number is stored in
the Last Error Number status register. Depending on the
Event Log filter settings, this error may also be logged to the
Event Log. See the Error Codes topic for a list of errors that
cause this bit to be set. This bit is cleared when any valid
parameter write occurs.
14
RunErr
Runtime Error
When an unexpected condition occurs that does not have its
own error bit, this bit is set and an error number is stored in
the Last Error Number status register. Depending on the
Event Log filter settings, this error may also be logged to the
Event Log. See the Error Codes topic for a list of errors that
cause this bit to be set.
15
-
Reserved
16
-
Reserved
17
-
Reserved
18
PFNoTrans
Pressure/Force No Transducer
This error bit is set in the same way that the No Transducer
error bit is set, except this bit is set based on the secondary
analog pressure/force input.
19
PFTransOverflow Pressure/Force Transducer Overflow
This error bit is set in the same way that the Transducer
Overflow error bit is set, except this bit is set based on the
secondary analog pressure/force input.
20
PFNoiseErr
Pressure/Force Noise Error
Note:
The Pressure/Force Noise Error bit may turn on because the
Noise Error Rate parameter is set too low. The Pressure/Force
Noise Error Rate should be set to a value much higher than the
expected velocity of the axis. If your axis is experiencing Noise
Errors, this is the first item you should check. Setting the
Pressure/Force Noise Error Auto Stop to Status Only to avoid
854
Delta Computer Systems, Inc.