Delta RMC151 User Manual
Page 767
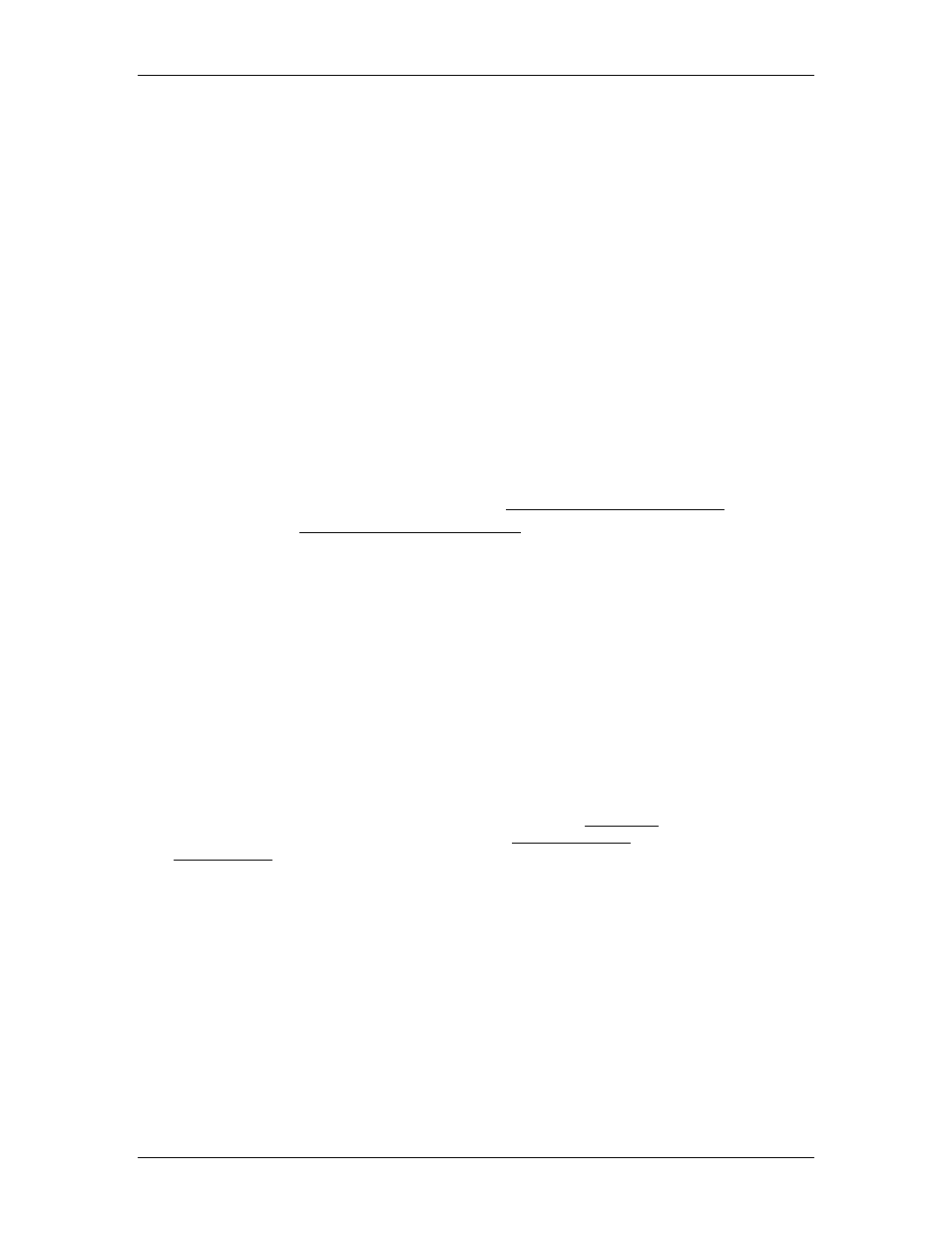
8 Command Reference
with respect to the
master position.
Because the profile is a 5th-order polynomial, it can have multiple points of inflection.
This means the position can change direction several times. Care must be taken that the
profile generates the expected profile. Make sure to test the command with the
parameters you expect to use. Breaking the move into shorter sections can help minimize
large swings.
Endpoint Conditions - Master Start Position
At the Master Start Position, the slave will be at the Slave Start Position, which is the
position at the time the command was issued. The Gear Ratio and Gear Ratio Rate at this
position are determined as described below.
If the slave was already geared when this command was issued, the gear ratio will be the
slave's current gear ratio. The gear ratio rate will be the current gear ratio rate if the
previous command was an Advanced Gear Move. Otherwise it will be zero (0).
If the slave was not geared when this command was issued, the gear ratio is set to the
ratio of the current slave velocity to the current master velocity. The gear ratio rate is
assumed to be zero (0). If the master is moving very slowly or nearly stopped when this
command is issued, the computed gear ratio may be very large. There are two ways to
avoid this problem:
•
Use a different gearing command, such the Gear Pos (Clutch by Rate) (39) command.
•
First issue the Gear Pos (Clutch by Time) (30) command with a 0:1 ratio and a time of
zero, then immediately issue this command with the desired parameters.
Endpoint Conditions - Master Sync Position
At the Master Sync Position, the slave profile will be at the Slave Sync Position with
the specified Final Gear Ratio and Final Gear Ratio Rate.
Following the Profile
While the master is in the Profile Range or on the Master Start Position and Master Sync
Position endpoints, the slave will follow the profile regardless of the direction the master
is moving.
If the master position moves to one of the endpoints and the gear ratio rate at that
endpoint is zero, the profile will continue indefinitely at the gear ratio of the endpoint. If
the master moves to the Master Sync Position, the slave will be locked at that gear
ratio. If the master moves beyond the Master Start Position, the ratio will not be locked,
meaning that if the master moves back inside the profile, the slave will follow the profile.
If the master position moves beyond one of the endpoints and the gear ratio rate at that
endpoint is non-zero, the polynomial will continue for two loop times, and if a new
command is not issued during this time, then a Closed Loop Halt will occur and the
Runtime Error bit will be set. Notice that if the Runtime Error AutoStop is set to a
different type of halt, that halt will also occur.
The Target Generator Status bits can be used to check whether the master has moved
beyond an endpoint. See the Target Generator State Bits section below.
Intended Use
This command is intended to be followed by another command, especially if the Final
Gear Ratio Rate is non-zero. Typically, this command is used only in a user program,
where it is very easy to issue another command immediately when the Done bit is set,
indicating the master has moved beyond the Master Sync Position. Use the Wait For or
Conditional Jump Link Types to check for the Done bit.
A Final Gear Ratio of zero (0) means that the slave will stop when the master reaches
the Master Sync Position.
Why Bother?
deltamotion.com
747