Command: open loop relative (12), Open loop relative (12) – Delta RMC151 User Manual
Page 725
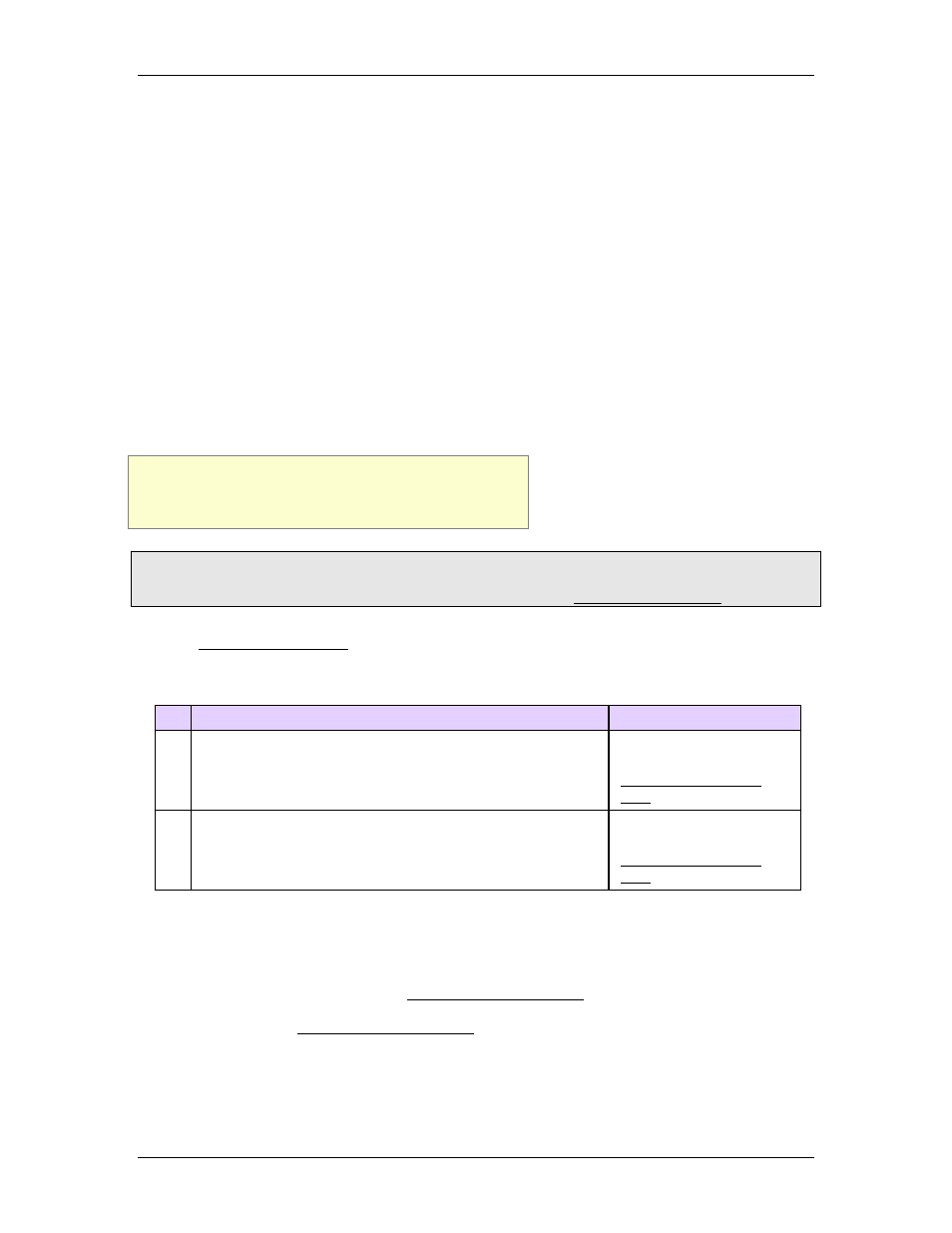
8 Command Reference
If this command is used with a Requested Output of zero volts, notice after reaching
position, the position will probably drift because it is in open loop. If you need to hold
position, switch to closed loop control, or adjust the Output Bias to minimize drifting.
Why Bother?
This command is often used to stop the axis in Open Loop, instead of an Open Loop Rate.
With this command you'll know approximately where the axis will stop, which you don't
know with an Open Loop Rate. To do this, the Requested Output must be 0 (or close to
zero).
Another use for this command is making an open loop profile based on position, which
can be used in injection molding.
Another application is clamping. If the Requested Position is beyond the clamping point,
some Control Output will always be applied when it is clamping. When moving into the
clamp, the axis will be slowing down because of the ramp and won't hit so hard.
8.4.3.4. Command: Open Loop Relative (12)
Supported Axes: Position Control Axes
Supported Control Modes: All
Firmware Requirement: 1.00 or newer
Note:
This command is a specialized Open Loop command. Do not use before fully understanding
how it works! To simply issue an Open Loop output, use the Open Loop Rate (10) command.
See the Commands Overview topic for basic command information and how to issue
commands from PLCs, HMIs, etc.
Command Parameters
# Parameter Description
Range
1 Requested Output (V)
-10≤V≤10
See Limitations in
2 Requested Distance (pos-units, signed)
Any.
See Limitations in
Description
This command ramps the open loop Control Output from its current value to the
Requested Output while the axis moves the distance specified by the Requested
Distance.
This command is identical to the Open Loop Absolute (11) except that the Requested
Distance is relative to the Actual Position when the command is issued, not an absolute
position. See the Open Loop Absolute (11) topic for details.
Limitations
•
The Requested Output must be of the same sign as the Control Output at the
time the command is issued. The Control Output cannot change sign during the
ramping. An incorrect Requested Output will cause a command error.
deltamotion.com
705