Simulating motion – Delta RMC151 User Manual
Page 133
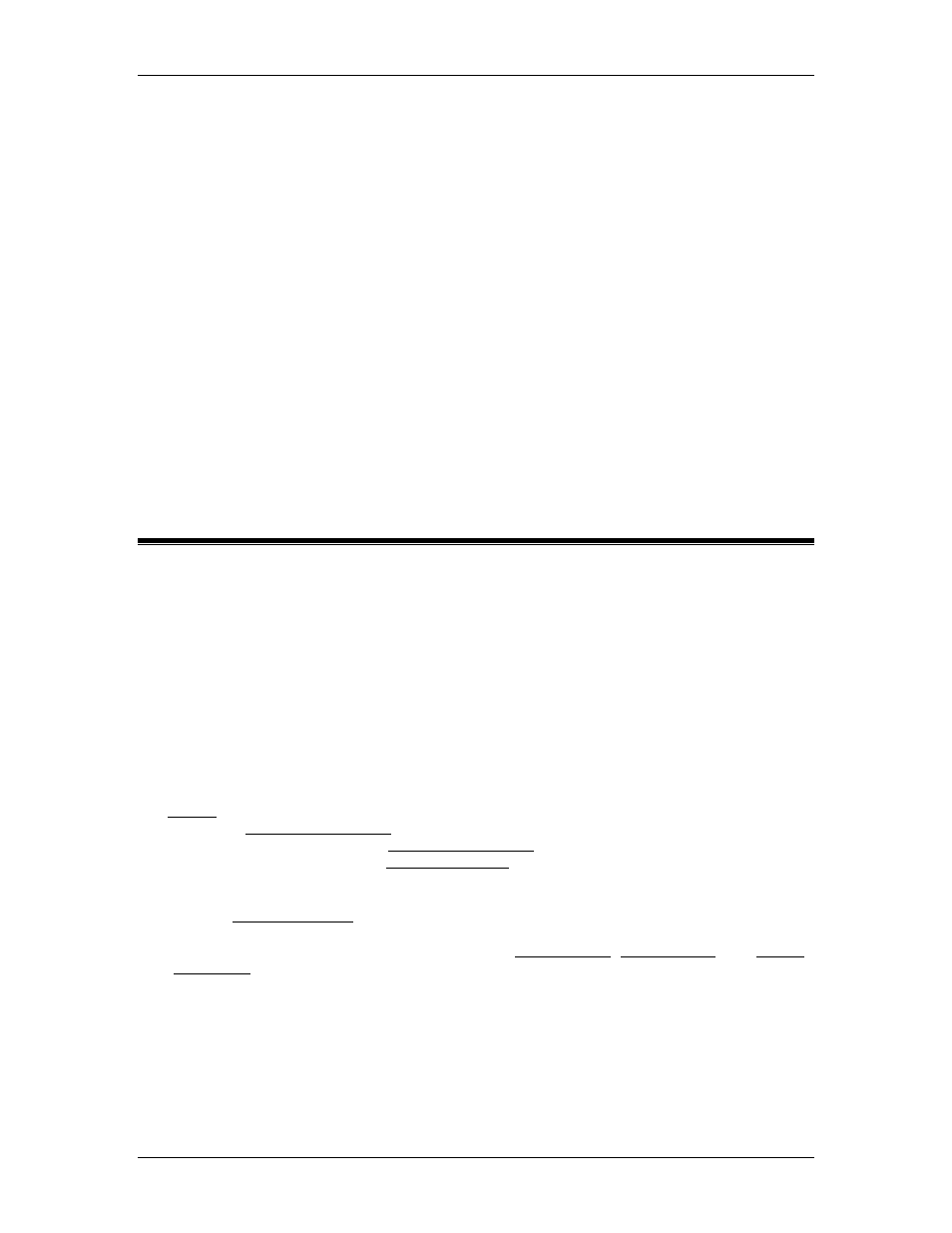
3 Controller Features
The behavior of the components of the gearing target, including the Target Velocity,
Target Acceleration, and Target Jerk, depend on the type of register used as the master:
•
Target Position
When gearing to a Target Position, the slave Target Velocity will be the ratioed master
Target Velocity, the slave Target Acceleration will be the ratioed master Target
Acceleration, and the slave Target Jerk will be the ratioed master Target Jerk.
•
Actual Position
When gearing to an Actual Position, the slave Target Velocity will be the ratioed
master Actual Velocity (filtering applies), the slave Target acceleration will be the
ratioed master Actual Acceleration (filtering applies), and the slave Target Jerk will be
zero (0).
•
Actual Pressure/Force
When gearing to the Actual Pressure/Force, the slave Target Velocity will be the
ratioed master Actual Pressure/Force Rate, the slave Target Acceleration will be the
ratioed simple derivative of the velocity, and the slave Target Jerk will be zero (0).
•
Other Registers
When gearing to any other register, the slave Target Velocity will be the ratioed simple
derivative, the slave Target Acceleration will be the ratioed simple derivative of the
velocity, and the slave Target Jerk will be zero (0).
3.6.5. Simulating Motion
The RMC can simulate position, pressure, and force control on a position, position-pressure or
position-force control axis. The simulator is not available on pressure-only, force-only, or
velocity control axes. During simulate mode, the axis' physical output is 0 V.
Use simulate mode to:
•
Learn how to move and tune an axis.
•
Develop and run user programs on your RMC before the machine is ready for motion.
•
To approximate a given real hydraulic system.
Set the Simulate parameters to values that correspond to your real system. Then tune
the simulated axis. This will give you a good indication of the tuning values required
for the real system.
The simulated system will be limited to the limits of the simulated transducer. For example, if
the Counts for a simulated MDT-feedback axis tries to go under 0 counts, or above 1048575
(16#FFFFF), a Transducer Overflow error will occur. If a voltage feedback axis tries to go
below -10 Volts or above +10 V, a Transducer Overflow error will occur. To recover from a
transducer overflow error, use the Direct Output (9) command to move away from the limit.
Simulator Wizard
Use the Simulator Wizard to quickly set up an axis in simulate mode. It will set the
simulator parameters, travel limits, and tuning gains so you can immediately move the
axis in simulate mode. Axis parameters such as Linear/Rotary, SSI Data Bits, and Analog
Input Type (±5V, ±10V, 4-20mA) should be set before using the wizard.
1. Enter Desired Position Range
Enter the desired range of position travel. For rotary axes, choose the number of
position units per rotation.
2. Enter Maximum Velocity
Enter the desired maximum velocity. This is the velocity at which the axis will move
with 10 V of Control Output.
deltamotion.com
113