Delta RMC151 User Manual
Page 492
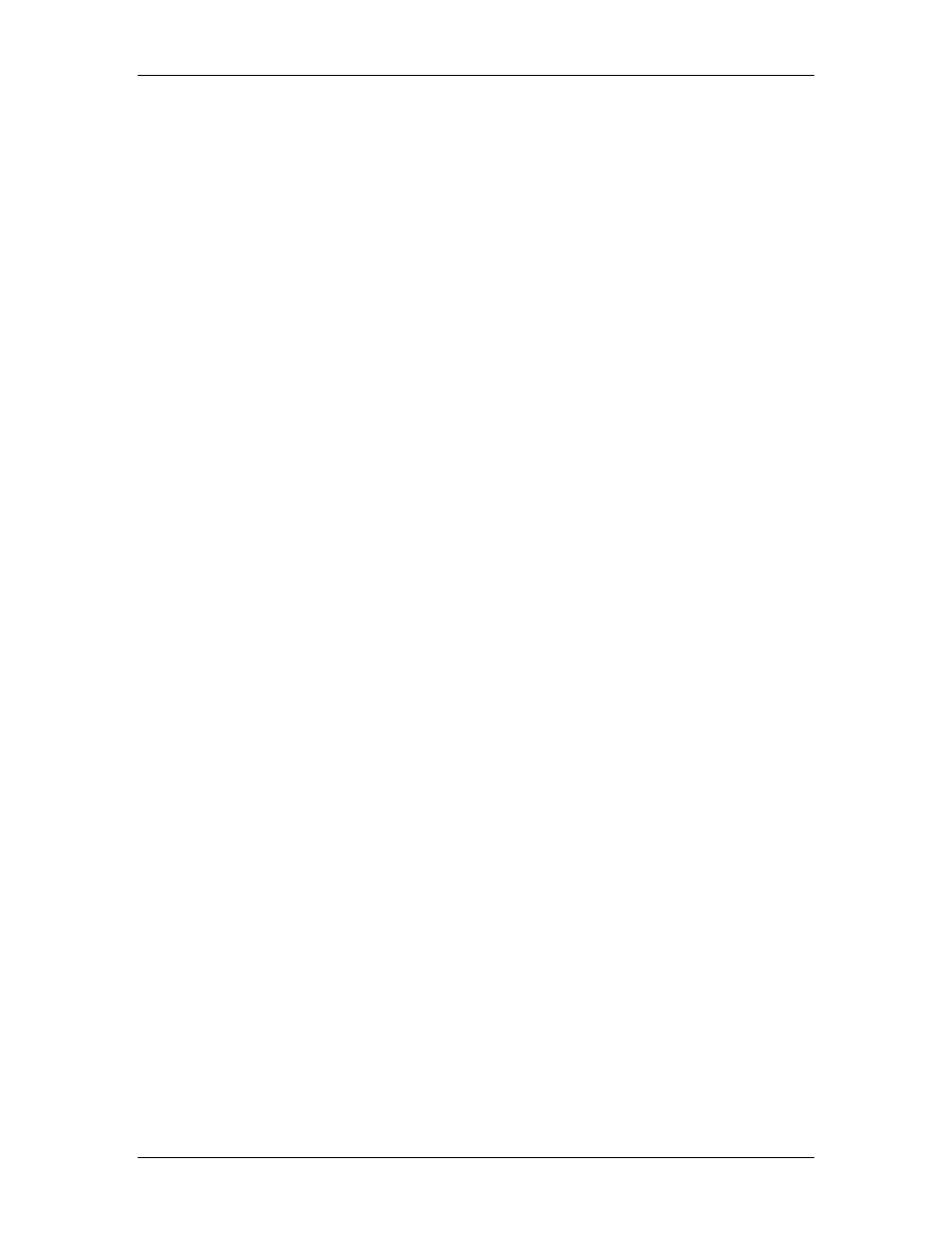
RMC70/150 and RMCTools User Manual
in the Output Data by the PLC program, a copy of the Output Data could prematurely be
sent to the RMC, mixing some old data with some new data. When the Sync Register is
used, this problem is avoided by the simple convention of having the PLC program update
the Sync Register after all other registers have been set to the desired values. The RMC is
then guaranteed to receive all the data in a single block.
•
Coordinating when Input Data has been updated to reflect an issued command.
This benefit is best demonstrated with an example. Suppose that an axis is holding
position with its In Position status bit set. If the PLC issues a new move command to a
new position, then we will see that the In Position bit will go off when the command is
first processed and remain off until the new move completes and the axis is at the new
position. How then does the PLC know when its copy of the In Position bit received in
the Input Data reflects the new command having been received? When the Sync Register
is used, the PLC can simply wait until the Sync Register coming from the RMC matches
the one it sent to the RMC when issuing the command, and it can then safely examine the
In Position bit.
Setting the Sync Register Mode
To select whether the Sync Register is used:
1. In the Project pane, expand the Modules folder, double-click the CPU module, and
choose PROFINET.
2. Under Sync Register, select either Use a Sync Register or Do not use a Sync
Register.
Using Input Data in the PLC
If the Sync Register is used, then the first register is reserved as the Sync Register. All
other registers in the Input Data are controlled by the Outgoing Cyclic I/O Data address
specified in the PROFINET Settings Page. When the I/O connection is established, the
Input Data is automatically updated in the PLC at the specified PROFINET update time.
The PLC can simply use the data whenever it needs it. The RMC does not wait for the
Sync Register to change to update its Outgoing Cyclic I/O Data.
Notice that the data types of the variables in the RMC must match the data types of the
structure receiving the Input Data from the RMC. Specifically, registers of type REAL in
the RMC must correspond to REAL data types in the PLC, and all other RMC data types
(DINT and DWORD) should correspond to tags of type DINT or DWORD in the PLC.
Writing Output Data with a Sync Register from the PLC
To write data in the RMC controller using I/O data when the Sync Register is used, do the
following in the PLC:
1. Wait for the Sync Registers in the Input Data and Output Data to match.
2. Update any Output Data register values, except the Sync Register.
3. Change the value of the Output Data Sync Register.
4. Do not change any Output Data registers until the Input and Output Sync Registers
match again.
The RMC will apply the Output Data register contents only once.
Writing Output Data without a Sync Register from the PLC
To write data in the RMC controller using I/O data without the Sync Register, simply
change the Output Data registers in the PLC and they will get applied in the RMC. Often
care must be taken as to the order that the registers are updated to ensure that actions
triggered by changes to registers in the RMC have updated values for any parameters
they use. It is often necessary to also understand whether the I/O data is updated
synchronously to the PLC scan or not.
Writing to the Command Area from the PLC
The Incoming Cyclic I/O Data area can be set up to point to the Command Area registers
directly, or indirectly through the Indirect Data Map. The Sync Register should always be
472
Delta Computer Systems, Inc.