Command: gear position (clutch by time) (30), Gearing, Gear pos (clutch by time) (30) – Delta RMC151 User Manual
Page 748: E gear pos (clutch by time) (30)
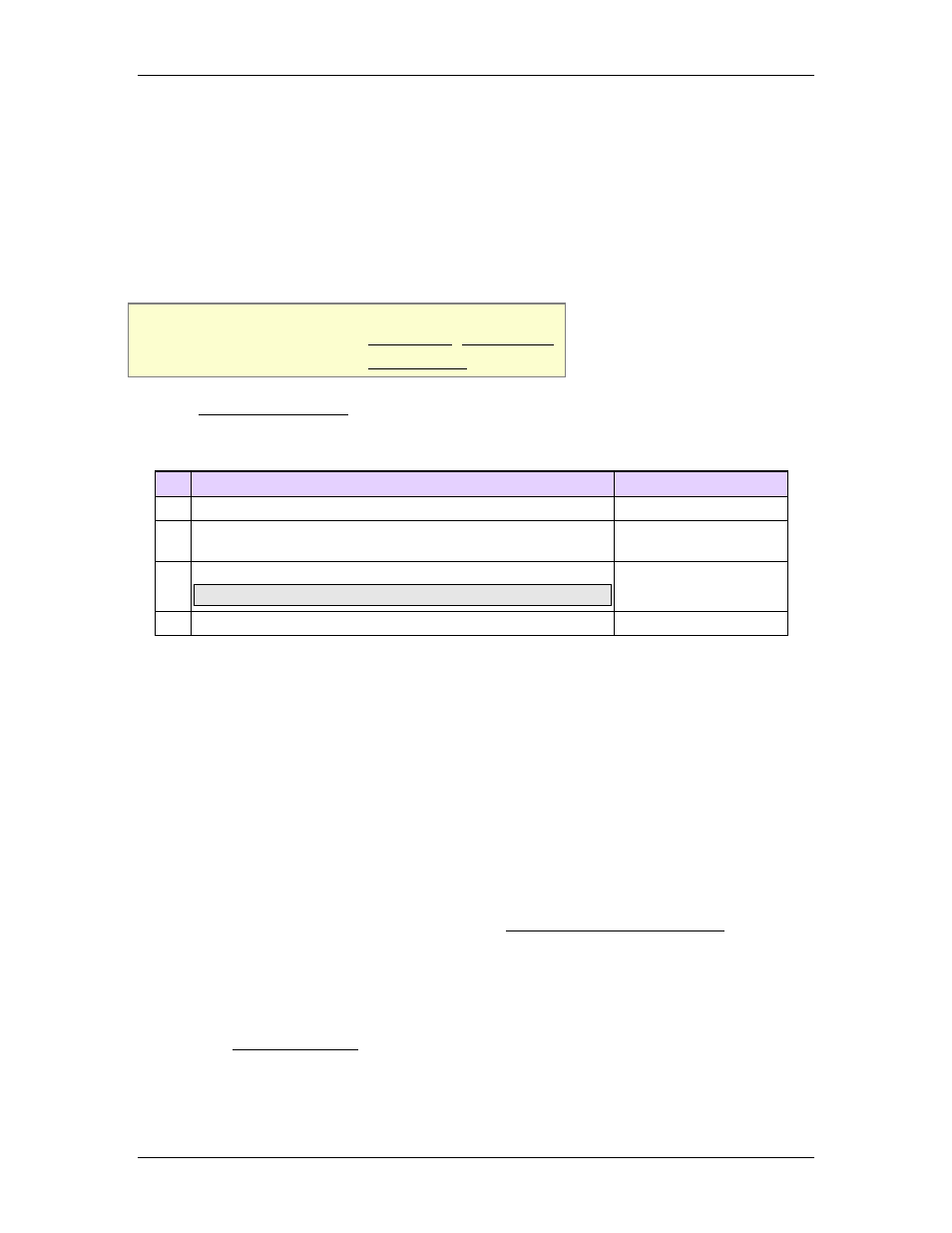
RMC70/150 and RMCTools User Manual
The Target Generator Done, State A and State B bits are all off during the gearing.
Pri. TG SI Busy (Primary Target Generator Superimposed Busy) Bit
This bit will be set during the transition. The transition begins when the motion command
is issued, not necessarily when the Transition command is issued. When the transition
completes, this bit will clear. At this point, the slave axis will on the mapped relationship.
8.4.6.2. Command: Gear Position (Clutch by Time) (30)
Supported Axes: Position Control Axes
Supported Control Modes: Position PID, Position I-PD
Firmware Requirement: 1.30 or newer
See the Commands Overview topic for basic command information and how to issue
commands from PLCs, HMIs, etc.
Command Parameters
# Parameter Description
Range
1 Numerator
Any REAL number
2 Denominator
Any REAL number,
not 0
3 Master Register
Note: Specifying a Register Address
Valid RMC register
4 Clutch Time (sec)
>=0
Description
This command gears the axis to the Master Register, using the value in this register as
the master position. Typically the master register is the Target or Actual Position of
another axis.
When this command is issued, the RMC uses the current gear ratio or determines the
current gear ratio by comparing the velocities of the master and slave. The gear ratio is
then ramped from its current effective ratio to the requested ratio, in the time specified
by the Clutch Time parameter. The ratio is determined by the Numerator and
Denominator.
If the master register is not a Target or Actual Position, the Gear Position (Clutch by
Time) (30) command will assume an initial gear ratio of 0:1. This may cause a jerk in the
motion of the geared axis if it is already moving.
If the master is moving very slowly or nearly stopped when this command is issued, the
initial gear ratio may be very large. There are two ways to avoid this problem:
•
Use a different gearing command, such the Gear Pos (Clutch by Rate) (39) command.
•
First issue this command with a 0:1 ratio and a time of zero, then immediately issue
this command again with the desired gear ratio and clutch time.
If both axes are stopped or moving very slowly, this command can be issued with a
Clutch Time of zero. If either of the axes are moving, a Clutch Time of zero may cause
a sudden jerk.
See the Gearing Overview topic for general information about gearing, including Gear
Ratio, Clutching and possible Gear Masters.
Gear Position (Clutch by Time) Example
728
Delta Computer Systems, Inc.