Using a profinet i/o connection, E using a profinet i/o connection, Selecting the input and output modules – Delta RMC151 User Manual
Page 491: E using, A profinet i/o connection
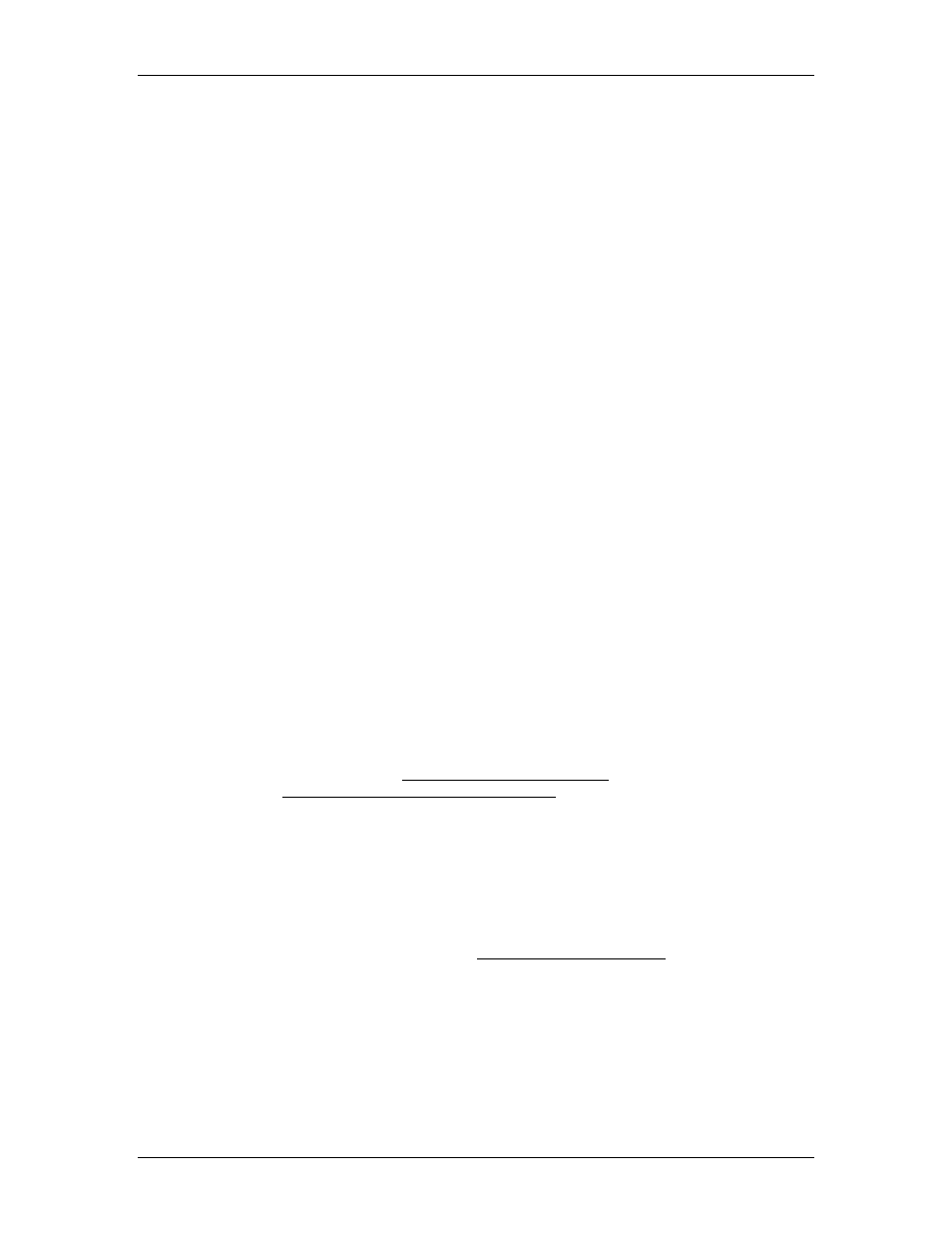
6 Communication
recommended because it can result in the IP address being changed or cleared at times
when RMCTools is connected to the RMC.
An alternative method is to set the IP address settings in RMCTools, and then instruct the
IO-Controller through the PROFINET Configuration Software to leave the IP address as it
is when connecting to the IO-Device. For example, STEP7’s HW Config software version
5.5 includes an Assign IP address via IO controller checkbox in the IO device’s
general properties that should be unchecked to choose this option. This is the
recommended method for RMC controllers.
Selecting the Input and Output Modules
The RMC PROFINET devices are set up to have 3 virtual slots. The first slot is the DAP,
and will be named RMC150E or RMC75E. The second slot is the Input Slot, and the third
slot is the Output Slot. In the PROFINET IO device library, under the selected DAP, you
will find a folder of input modules and a folder of output modules. Select exactly one
Input module and one Output module to install in slots 1 and 2 respectively.
The Input and Output modules to choose from differ only in the number of registers to be
transferred. The Input module corresponds to the Outgoing Cyclic I/O Data area in the
RMC, and the Output module corresponds to the Incoming Cyclic I/O Data area. Notice
that if the Sync Register is used, the first register in each block will be reserved as the
Sync Register.
Setting the Update Time
One additional item configured in the PROFINET configuration software that affects the
PROFINET communication with the RMC is the Update Time. The RMC75E and RMC150E
controllers support update times of 2 ms, 4 ms, 8 ms, 16 ms, 32 ms, 64 ms, 128 ms, 256
ms, and 256 ms. Notice that the update time cannot be set lower than the Loop Time of
the RMC. Therefore, if a 4 ms loop time is used, then the minimum PROFINET update
time will be 4 ms.
Related to the Update Time is the Watchdog Time. This is specified as a multiple of the
Update Time. For example, with a Watchdog Time multiplier of 3 and an Update Time of
16 ms, the Watchdog Time will be 48 ms. Most IO controllers fix this value at 3, but some
may allow configuration of this value.
6.8.10.7.3. Using a PROFINET I/O Connection
This topic describes the how to control the RMC via the PROFINET I/O connection's cyclic data.
For detail using the acyclic data, see Using PROFINET Record Data. For details on setting up a
connection, see the Setting up a PROFINET I/O Connection topic.
Understanding the Sync Register
The cyclic I/O data can operate in two modes: with a Sync Register and without a Sync
Register. When using a Sync Register, the first Input Data register and first Output Data
register are each reserved as a Sync Register, and the RMC processes incoming data only
when the Sync Register changes. When not using a Sync Register, the RMC processes
incoming data each time any register in the block changes.
The Sync Registers show up in the Input and Output Data images in the PLC. In the RMC,
they are only visible in the Event Log. See Troubleshooting PROFINET for details.
Why Use a Sync Register?
The Sync Register gives the user tight control over synchronization between the PLC and
RMC. In applications that do not require this level of synchronization, the user can choose
to not include the Sync Register.
The synchronization provided by the Sync Register is useful when:
•
Treating writes to a block of registers as a consistent block.
Not all PLCs synchronize their I/O with the PLC scan. Therefore, while data is being placed
deltamotion.com
471