Delta RMC151 User Manual
Page 301
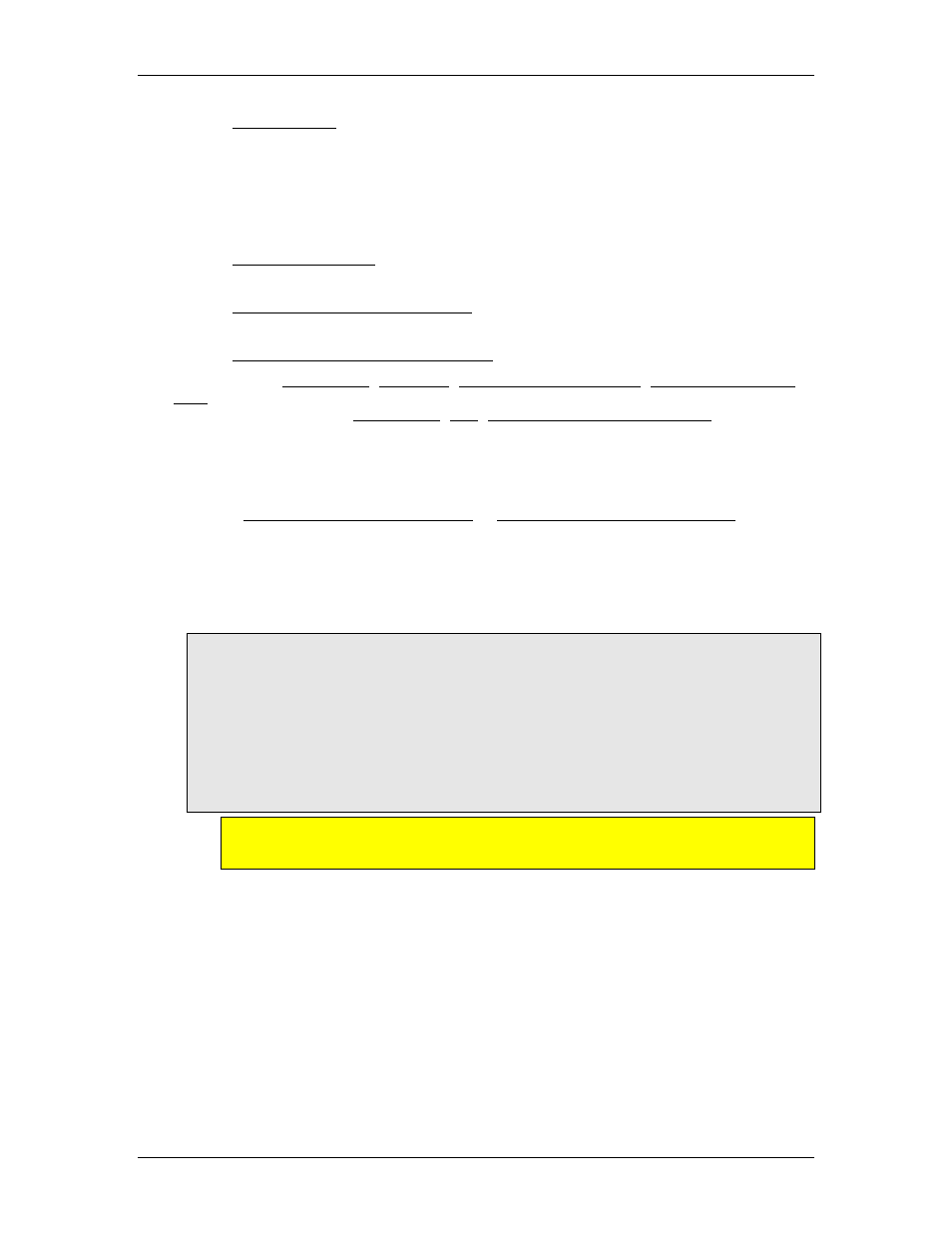
5 Programming
See the User Programs topic for details on how to create and run user programs to issue
to commands to the RMC.
Issuing Commands from a Host Controller, such as a PLC or HMI
You can issue commands directly to the RMC from a host controller, such as a PLC or
HMI. It is possible to issue commands to multiple axes simultaneously.
Via PROFIBUS
See the PROFIBUS Overview topic and read the topic of the mode you are using.
Via PROFINET IO
See the Using a PROFINET I/O Connection topic.
Via EtherNet/IP I/O
See the Using an EtherNet/IP I/O Connection topic.
Via Ethernet (Modbus/TCP, FINS/UDP, CSP or DF1 over Ethernet, Mitsubishi Procedure
or Serial RS-232/485 (Modbus RTU, DF1, Mitsubishi Bidirectional Protocol)
Use the following procedure to issue a command:
1. Determine which Axes
Determine which axis or axes you are going to issue the command to.
2. Find the Address
In the RMC70 Command Registers Map or RMC150 Command Registers Map, locate
the addresses of the Command Registers for the communication protocol and RMC you
are using.
3. Write to the Command Registers
Write values to the Command Registers of the axis or axes you wish to issue the
command to. You need only write to as many Command Parameters as are used by
the command you will issue.
Note:
The RMC will process the command as soon as a write is made to the Command
register. Most PLCs or HMIs can write to the these in one write, such as a block write.
If your host controller can only write to one register at a time, it is important that you
write to the Command register last. If your system can write to multiple registers at a
time, you can write to all the Command Area registers at once.
Note:
If you are using a 16-bit addressing protocol, such as Modbus, you must write 2 words
for each register you wish to write to in the RMC. All command registers are 32-bit
floating-point values.
Caution: For each command you wish to issue, write it only once so that it is
issued only once. If you issue the same motion command multiple times, it can
cause the target position to overshoot the requested position.
4. Optional: Use the Command Request and Acknowledge Bits
If your system requires tight synchronization, you should use the Command Request
and Acknowledge bits. These bits indicate that the RMC has received the command.
Typically, these bits are only needed when using a PLC or other highly capable host
controller. See the Command Request and Acknowledge bits topic for details.
For example, if you issue a Move command and then wait for the In Position Status bit
to be set, it is important that you do not start checking the In Position status bit until
the RMC has received the command. The Command Request and Acknowledge bits tell
you when there RMC has received command.
Examples
1. RMC70: Move Absolute Command to Axis 1
deltamotion.com
281