Delta RMC151 User Manual
Page 134
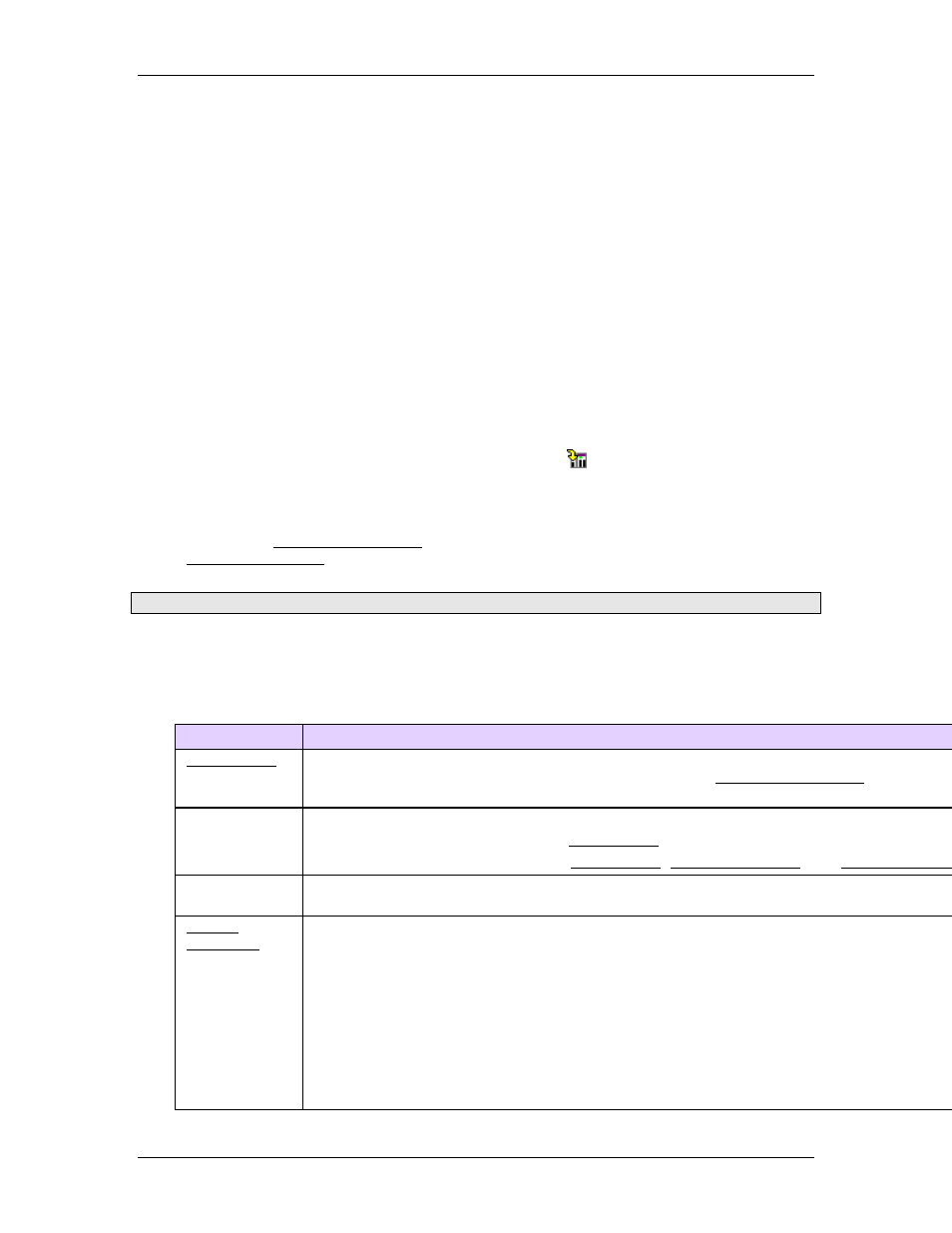
RMC70/150 and RMCTools User Manual
3. Enter Maximum Acceleration
Enter the desired maximum acceleration. This is not necessarily a true limit of the
acceleration, but helps determine the response of the simulator and the tuning gains.
For best results, set this value significantly higher than the acceleration rates you
intend to use on the axis. This value is typically at least an order of magnitude (10x)
greater than the maximum velocity.
4. Enter Pressure or Force Information
If the axis is position-pressure or position-force, enter the maximum force of the
simulator, and the desired range of the force area at the ends of the travel.
The tuning of the pressure or force is affected by the position settings, especially the
Maximum Acceleration. If the pressure or force tuning is poor, or pressure or force
following errors occur, run the Simulator Wizard again and increase the Maximum
Acceleration.
5. Review Parameters
Click Next and review the axis parameter settings in the Proposed column. Any
parameters with blue text can be changed. When you are satisfied with the values,
click Finish.
6. Download Axis Parameters
In the Axis Tools window, click the download button to apply the parameter
changes to the controller.
After setting these parameters, make sure to enable the axis. This can be done by
sending the Enable Controller (7) to the RMC. To do a basic move on the axis, send the
Move Absolute (20) command.
Note: The simulator wizard will set the simulator to 2
nd
order.
Simulating a Real System
The simulator can be configured to approximate your actual system. The simulator
parameters are in the Axis Tools, in the Axis Parameters, on the All tab, in the
Simulator section. You will need to set the parameters listed in the table below. Use the
guidelines below to calculate the Simulate parameters to approximate your real system:
Parameter
To calculate this parameter:
The System Gain units are pu/s/V, which is the speed the system moves for 1 V of control
To find this value, give 1 volt of Control Output (use the Open Loop Rate (10) command).
plot to find the steady-state Actual Velocity of the system. This is your System Gain.
Simulator
Order
The simulator can be set to 1
st
or 2
nd
order.
A 1
st
order system is defined by the System Gain and Time Constant.
A 2
nd
order system is defined by the System Gain, Natural Frequency, and Damping Factor
Time Constant
For a 1
st
order system. To calculate the time constant, determine the time it should take th
velocity to reach 95% of the steady state, and divide by 3.
For a 2
nd
order system. The Natural Frequency for a hydraulic system is normally between
30. Use the following formula to calculate the natural frequency for hydraulic system:
ω
= sqrt[(4*200000 *A
2
) /(mass * volume)]
where
ω =
Natural Frequency (Hz)
A = area of the piston (in
2
)
mass = the mass moved by the system (lb)
114
Delta Computer Systems, Inc.