Axes, Axes types – Delta RMC151 User Manual
Page 83
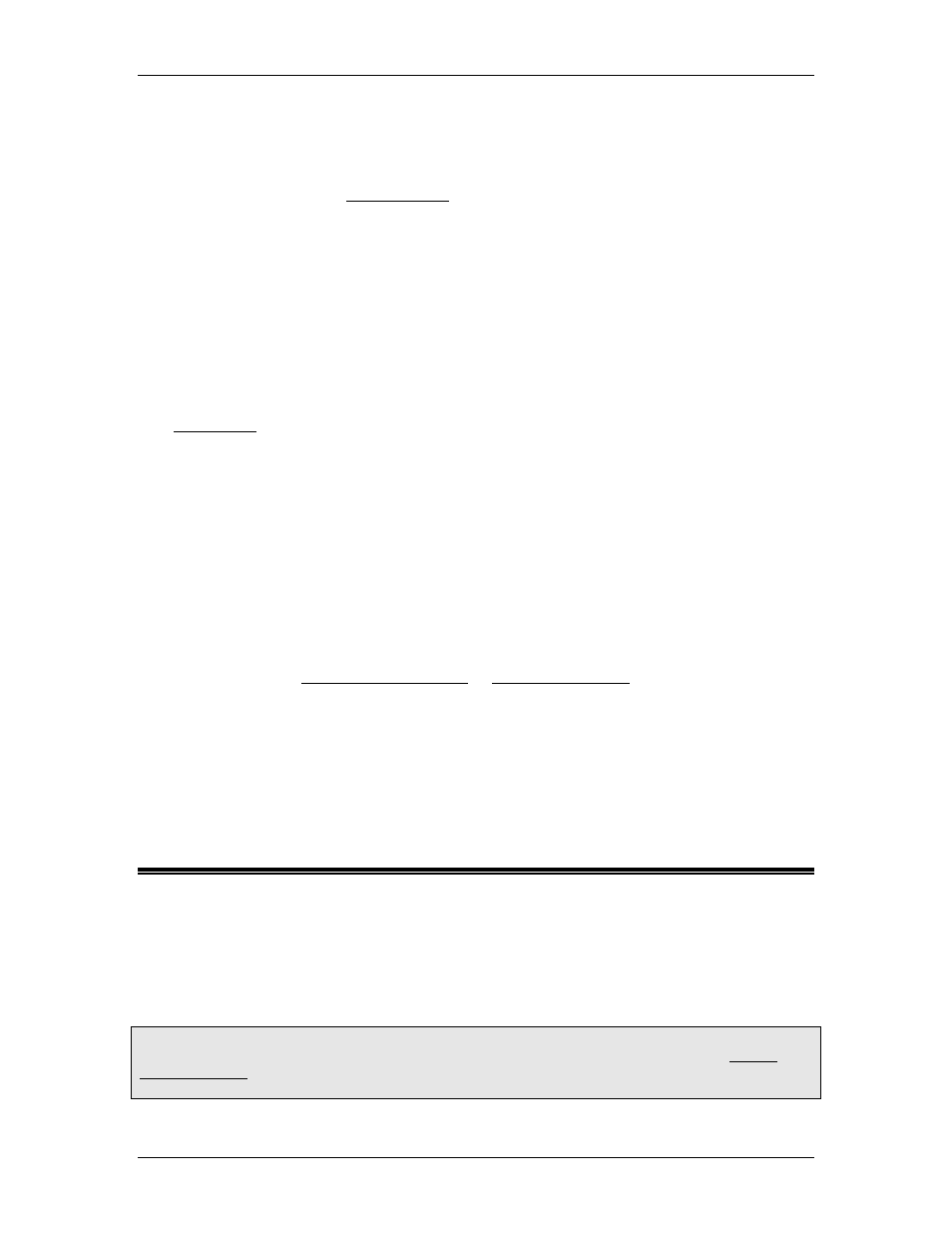
3 Controller Features
with SSI devices that have more than 24 bits, but you should make sure the counts will
not exceed 16,777,216. These limitations do not apply to voltage, current, or MDT
feedback types, since their values never exceed 24 bits.
Delta recommends that the Counts value not be allowed to exceed 24 bits (16,777,216)
because this causes the Actual Position to lose resolution. This occurs because the Actual
Position is stored as a 32-bit floating point number, which is limited to 24 bits of
precision. The resolution of a floating-point number depends on how large the number is.
For example, a floating point number can precisely represent any integer that fits in 24
bits (-16,777,216 to +16,777,216) or it can represent numbers at a 0.001 resolution in
the range of -16,777.216 to +16,777.216.
To determine when an axis’ Actual Position will lose resolution, look at the Counts
register. As long as the Counts register stays within 24 bits (-16,777,216 to
+16,777,216), then the Actual Position register will approximately match the resolution of
the transducer. However, as the Counts move outside that range, the Counts register and
the Actual Position register will lose resolution.
For example, if the Counts are 16,777,220 (slightly larger than 24 bits), and the
transducer counts (the counts directly from the transducer are represented exactly in the
Raw Counts register, which may be different from the Counts register, but it does indicate
the change in counts exactly) change by one to 16,777,221, the Counts value will still
read 16,777,220. It will not change until the counts have changed by 2, to 16,777,222.
This will cause the Actual Position to become "jerky" and will affect the control. This
problem is doubled for each power-of-two increase in the Counts value. Notice that the
Counts and Actual Position registers are still accurately keeping track of the position
change, but they are losing resolution.
Notice that in order to preserve accuracy on incremental feedback types, the RMC
internally maintains a 32-bit integer accumulator. This ensures that the position does not
drift due to loss of resolution.
Rotary axes use the Count Unwind value, which will keep the Counts within a defined
range. Therefore, as long as the Count Unwind is kept below 16,777,216, this additional
loss in resolution will not occur.
For linear axes, you can keep the Counts register from exceeding 24 bits by homing the
axis, or using the Set Actual Position (49) or Offset Position (47) commands. With
quadrature encoder inputs, the usable range with full resolution can be doubled by setting
the zero value of the Actual Position to the middle of travel. For absolute linear SSI
feedback, you can also use the Count Offset parameter to move the usable Counts range
closer to zero.
3.3. Axes
3.3.1. Axes Types
The axis types listed in this topic are available on the RMC. The required inputs and outputs
for each axis type constitute 1 axis. For example, a Position-Force application may require 3
analog inputs and 1 output, but is considered a single axis.
The RMC70 is a 1- or 2-axis motion controller with possible additional reference axes, with a
maximum of 4 axes.
The RMC150 can have up to 8 control axes and any number of reference axes, with a
maximum of 16 axes.
Note: It is possible to add more analog inputs on the RMC70 than can be assigned to axes.
However, it is still possible to view the voltage of the extra analog inputs using the Analog
Input Registers. Inputs that are unassigned to axes can have no status bits, error bits, scaling,
filtering, etc.
deltamotion.com
63