Profinet, Profinet overview – Delta RMC151 User Manual
Page 487
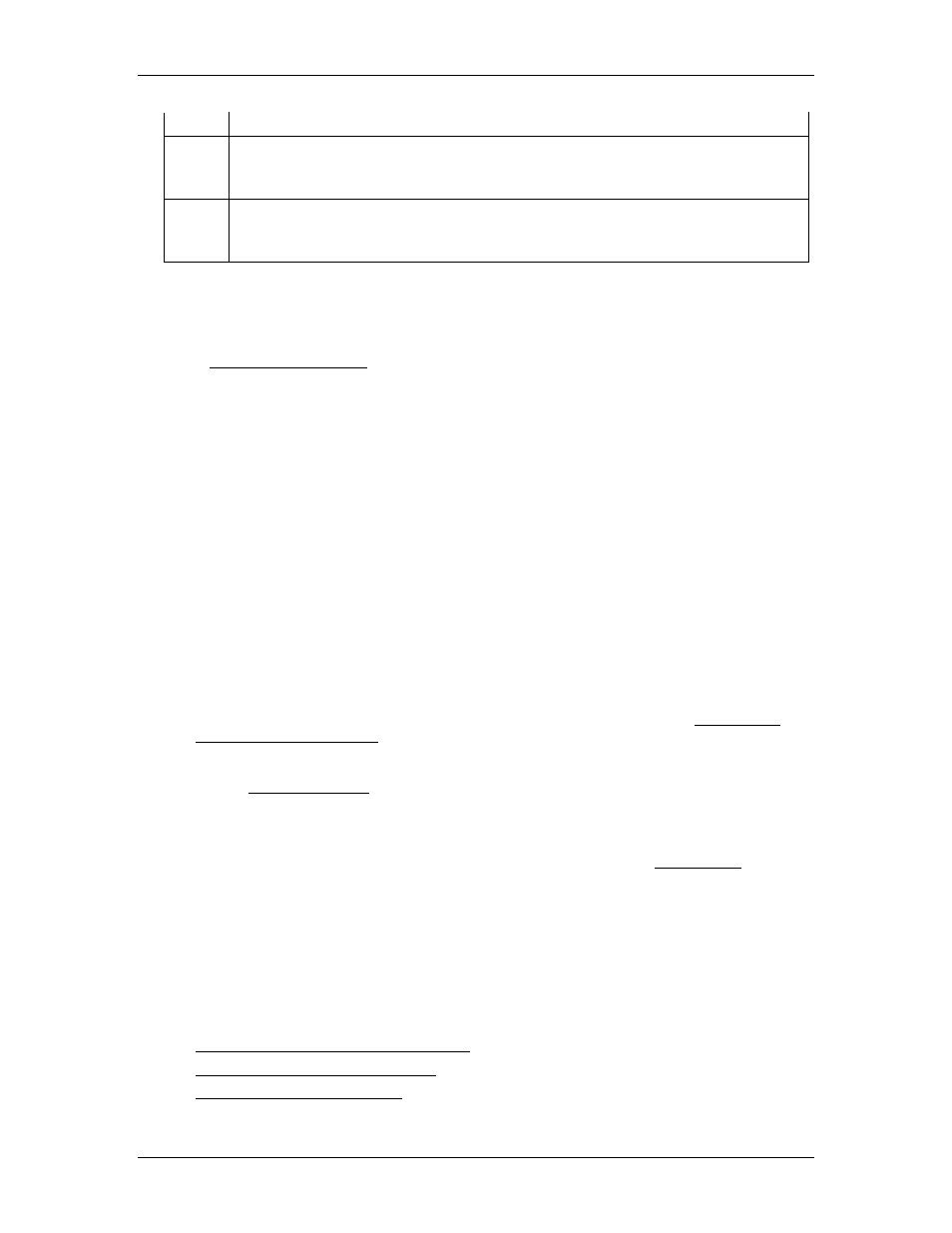
6 Communication
maximum value varies based on the PLC, but is generally around 120 registers.
0x13
(19)
Request length too small.
This error will occur on a Read or Write request if the length of the request is
smaller than expected.
0x15
(21)
Request length too large.
This error will occur on a Read request if the length of the request is larger than
expected.
Accessing Standard CIP Services and Attributes
The RMC supports a number of standard CIP objects. These objects have various services
and attributes that can be accessed through CIP Service requests. The RMC75E and
RMC150E Statement of Conformance documents—available for download on Delta’s web
site
these controllers. Advanced EtherNet/IP users can use these documents, together with
the EtherNet/IP specification and PLC documentation to access services in the supported
objects.
6.8.10.7. PROFINET
6.8.10.7.1. PROFINET Overview
PROFINET IO is an Ethernet-based standard for connecting distributed I/O with controllers for
fast data exchange, parameterization, and diagnostics. The bus cycle times for data exchange
are down in the millisecond range. Configuring a PROFINET IO system has the same look and
feel as in PROFIBUS.
The RMC75E and RMC150E controllers support PROFINET IO as an IO-Device. Therefore, an
IO-Controller must be configured to establish cyclic I/O data connections with the RMC and to
initiate acyclic data record transactions:
•
Cyclic I/O data is automatically exchanged between the PLC and RMC at the
specified update time. For example, status information from the RMC, and variables to
be written to the RMC would typically be part of the cyclic data. Cyclic I/O data is
defined by the Incoming and Outgoing Cyclic I/O Data as described in Setting up a
The RMC75E supports up to 128 registers in each direction, and the RMC150 supports
up to 256 registers in each direction. Notice that at the time of this writing (September
2010), Siemens S7 PLCs are limited to 63 registers in each direction.
•
Acyclic data transactions are performed only when needed. For example, if the PLC
creates a curve and sends it to the RMC, that data would typically be sent via the
acyclic data. Or, if the PLC needs to read a captured plot from the RMC, that is also
best done via the acyclic data. Acyclic I/O data is defined by the Record Data. The
RMC75E and RMC150E support acyclic transfer of up to 2048 32-bit registers (8192
bytes) in each direction.
The RMC supports only one controlling IO connection at a time. Therefore, PROFINET cannot
be used simultaneously with an EtherNet/IP IO connection. Other protocols can be used
simultaneously with PROFINET.
Further Information
For further information on setting up and using PROFINET IO with RMC controllers, refer to the
following topics:
•
Setting up a PROFINET I/O Connection
•
Using a PROFINET I/O Connection
•
deltamotion.com
467