Delta RMC151 User Manual
Page 119
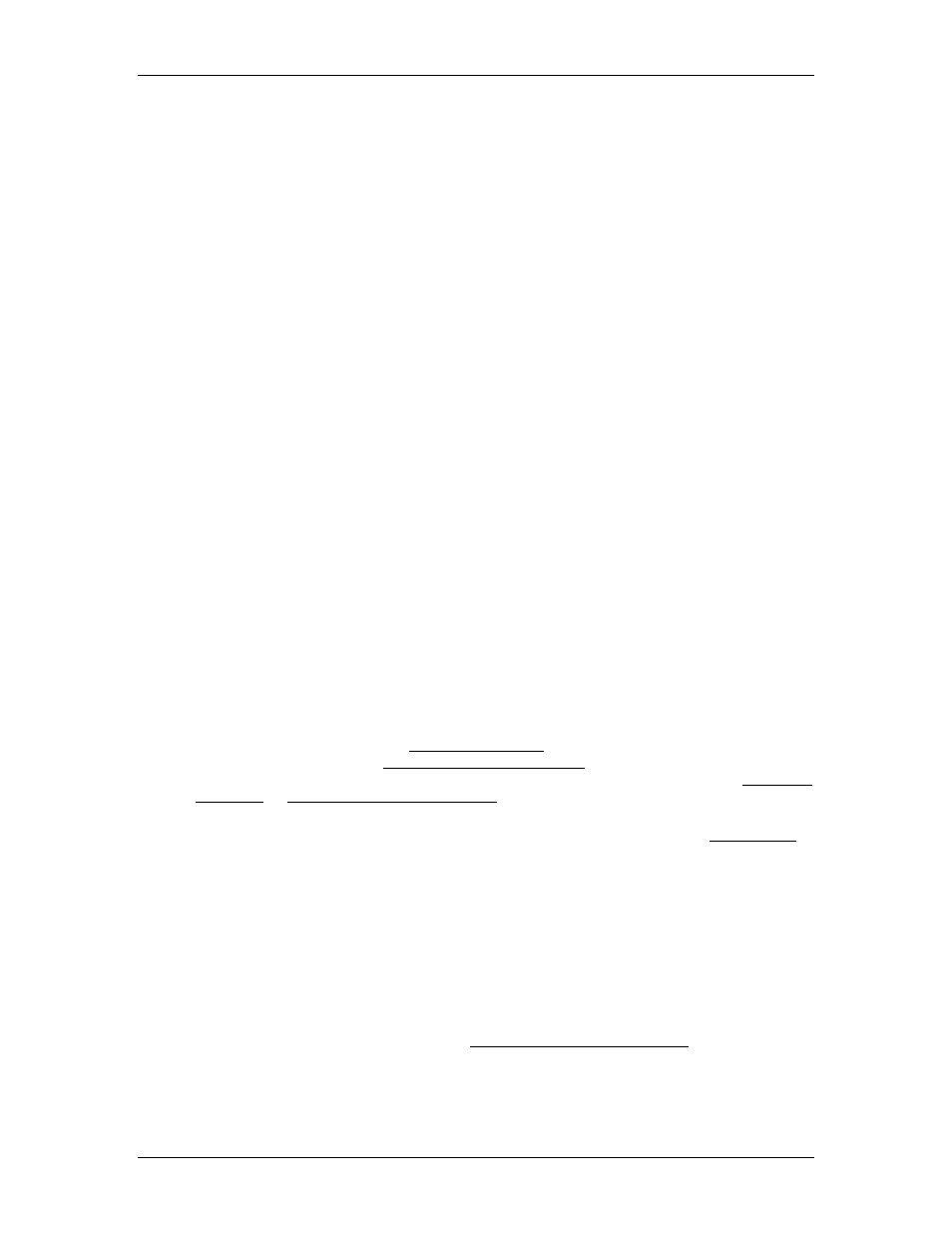
3 Controller Features
•
Allows inner loop to handle non-linear valve and other final control element problems.
•
Allows operator to directly control inner loop during certain modes of operation (such as
startup).
•
Allows controller to respond quickly to the faster inner loop.
Cascade Control Disadvantages
•
Cost of measurement of the secondary variable (assuming it is not measured for other
reasons).
•
Additional complexity.
Requirements for Cascade Control:
•
Inner loop system dynamics must be significantly faster (such as four times faster) than
the outer loop system dynamics. If the inner loop is not faster than the outer loop, then
the cascade will not offer any significant improvement in the system control.
•
Inner loop must have influence over the outer loop.
•
Inner loop must be measured and controllable.
Using Cascaded Loops in the RMC
Setting up Cascaded Loops
Setting up cascade control in the RMC involves the following steps:
1. Define Each Loop As an Axis
Each loop of the cascade control must be defined as an axis.
a. For the inner loop, define a standard Control axis.
b. For the outer loop, define a Cascading Outer Loop axis. This axis type provides
a virtual Control Output, but does not use a physical Control Output. If you
have more than two loops, all loops except the inner loop should be Cascading
Outer Loop axes.
2. Set up and Tune Inner Loop Axis
Set up the inner loop axis as normal, including setting the Scale/Offset and tuning.
3. Tie Output of Outer Loop to Input of Inner Loop
Use gearing to tie the output of the outer loop to the input of the inner loop. If the
inner loop is position, use the Gear Absolute (25) command. If the inner loop is
pressure or force, use the Gear Absolute (Prs/Frc) (59) command. Set the Gear
Absolute command parameters as listed below. You will also need to use the Transition
Rate (56) or Transition Rate (Prs/Frc) (64) command together with the Gear Absolute
commands.
a. The Master Register command parameter should be set to the PFID Output
of the outer loop axis.
b. The Master Point A and Master Point B command parameters should be set
to -100 and 100, respectively. This is because the PFID output ranges from -
100% to +100%.
c. The Slave Point A and Slave Point B command parameters should be set to
the minimum and maximum values that you want the inner loop axis to
control to. For example, if the inner loop is a valve spool that you want to
allow to travel from 0 to 0.5 inches, set the Slave Point A and Slave Point B
command parameters to 0 and 0.5, respectively.
d. Set the Endpoint Behavior command parameter to Truncate.
If the inner loop is velocity, use the Gear Vel (Clutch by Time) (31) command, with
the Master Register as described in item a above. The Denominator should be
set to 200, and the Numerator should be set to the velocity range of the inner
axis.
deltamotion.com
99