Delta RMC151 User Manual
Page 760
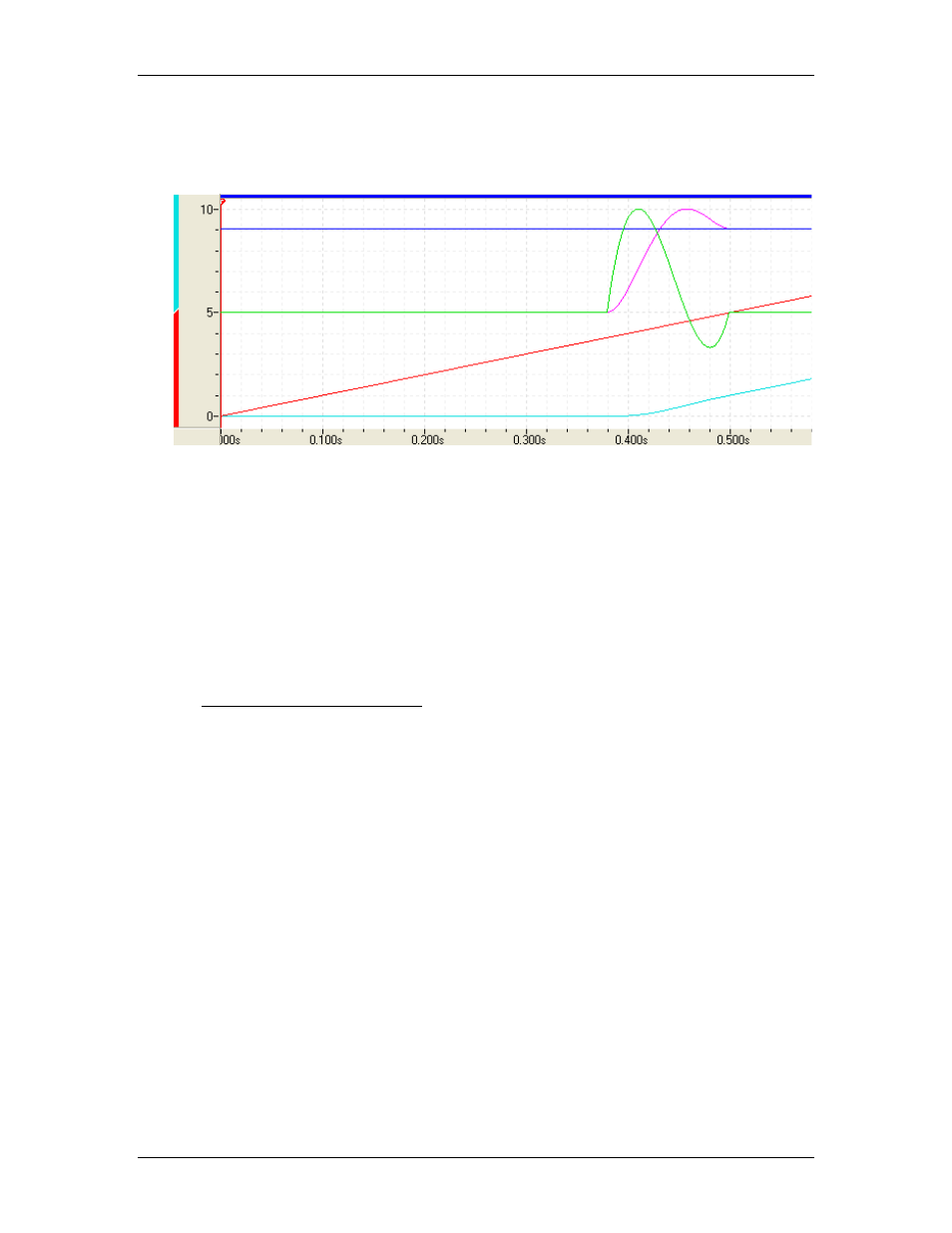
RMC70/150 and RMCTools User Manual
- Notice the sharp initial acceleration, but smooth rate of acceleration (due to zero jerk)
at the sync position. This makes tracking easier at the sync point.
Master Start Distance < 1.6666 x Slave Distance / Final Gear Ratio
- Notice that the slave velocity increases above the master velocity in order to reach the
sync position. This is acceptable or will be necessary in some applications.
If the Slave is not Initially Stopped
If the slave is not initially stopped when this command is issued, the Master Start
Distance will not be truncated to 2.5 x Slave Distance / Final Gear Ratio. Therefore, the
target profile may in some cases move in the other direction before moving in the
direction of the master. Make sure to test the Gear Pos (Clutch by Distance) parameters
you will be using to verify that the profiles are acceptable.
Gear Ratio Details
This command has only one register to specify the gear ratio. Therefore, it cannot exactly
represent certain fractional numbers, such as 1/3. If you require such a ratio, first issue
this command with the desired sync positions and an approximate final ratio, then issue
the Gear Pos (Clutch by Time) (30) command after the axes have locked into the final
gear ratio. Make sure to specify a time of zero (0) for the Gear Pos (Clutch by Time)
command. To maintain accuracy, this should be done in a user program. Use the Target
Generator Status bits to determine when the axes have locked in the final gear ratio. See
the Target Generator State Bits section below.
The Gear Pos (Clutch by Distance) command will be accurate up to the sync positions.
Therefore, you will not lose any accuracy by using the Gear Pos (Clutch by Distance)
followed by a Gear Pos (Clutch by Time) command with a time of zero.
Specifying a Register Address
When issuing this command from anywhere other than RMCTools, the addresses in the
Master Register command parameter must be entered as an integer value.
RMC addresses are represented in IEC format as:
%MDfile.element, where file = file number, and element = element number.
Use the following equation to convert a register address to integer format, N:
N = file * 4096 + element
Example:
Register address %MD8.33 is 8*4096 + 33 = 32801.
Rotary Motion
740
Delta Computer Systems, Inc.