Delta RMC151 User Manual
Page 766
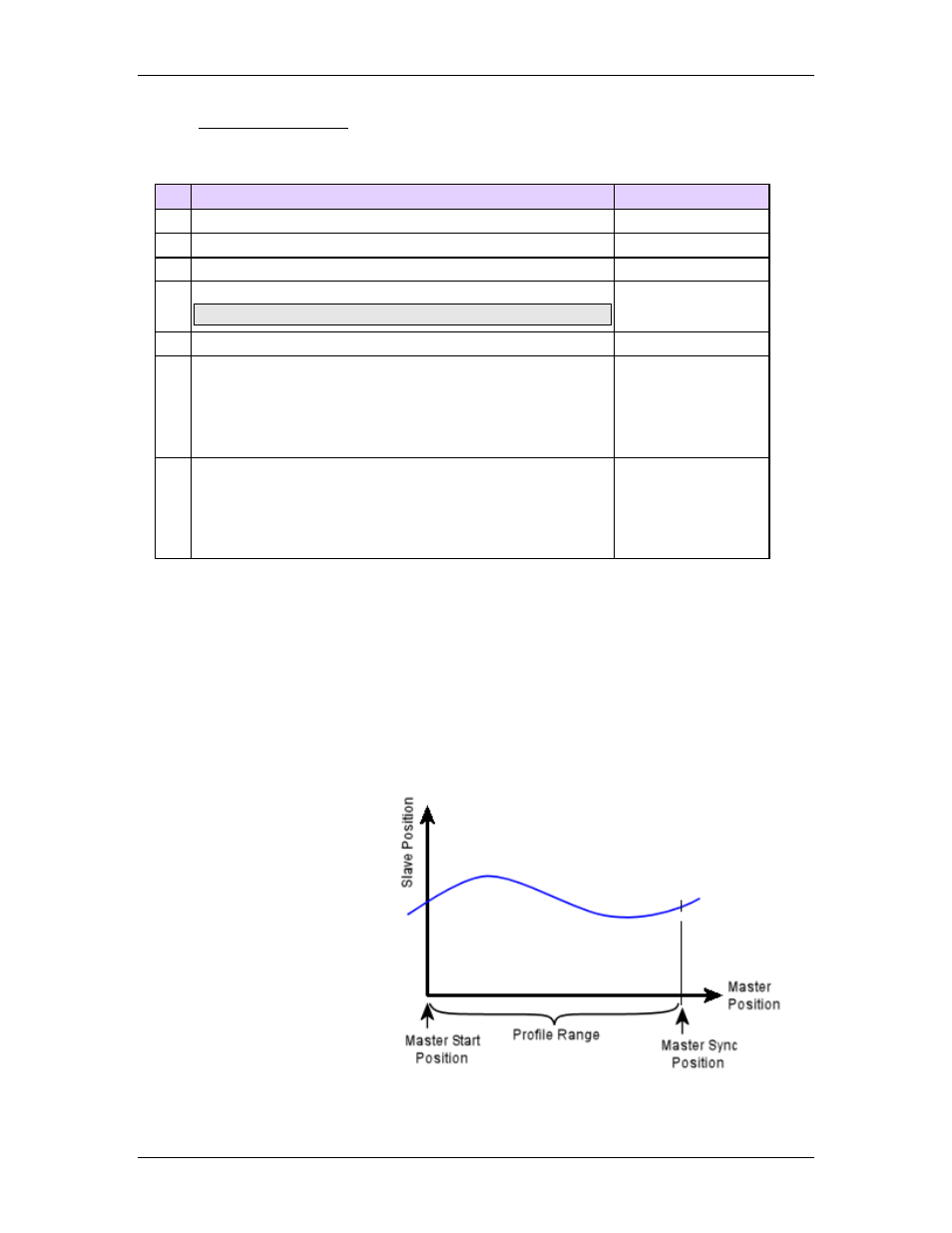
RMC70/150 and RMCTools User Manual
See the Commands Overview topic for basic command information and how to issue
commands from PLCs, HMIs, etc.
Command Parameters
# Parameter Description
Range
1 Slave Sync Position (position-units)
Any REAL number
2 Final Gear Ratio
Any REAL number
3 Final Gear Ratio Rate
Any REAL number
4 Master Register
Note: See Specifying a Register Address below.
Valid RMC register
5 Master Sync Position (position-units)
Any REAL number
6 Master Direction
If the master axis linear, this must be Nearest (0). The
other options will have no effect.
If the master axis is rotary, see the Rotary Motion
section below.
a valid integer as
described
7 Slave Direction
If the slave axis linear, this must be Nearest (0). The
other options will have no effect.
If the slave axis is rotary, see the Rotary Motion
section below.
a valid integer as
described
Description
This command calculates a gear target profile (a cam segment) for the slave axis using a
5th-order polynomial based on the position of the master axis. The profile extends along
the master from the Master Start Position (position at the time the command was issued)
to the Master Sync Position.
The Slave Profile
As shown in the diagram below, the slave profile extends along the master from the
Master Start Position (position at the time the command was issued) to the Master Sync
Position. The slave profile between the Master Start Position and Master Sync Position
endpoints is a 5th-order polynomial. The shape of the slave profile polynomial is defined
by the conditions at these endpoints.
The endpoint conditions
are:
•
Position
The position of the
slave.
•
Gear Ratio
The gear ratio of
the slave to the
master. This is the
rate of change of
the slave position
with respect to the
master position.
•
Gear Ratio Rate
The gear ratio rate
of the slave. This is
the rate of change
of the Gear Ratio
746
Delta Computer Systems, Inc.