Using omron controllers via ethernet/ip i/o, Omron plcs via ethernet/ip i/o, Using omron – Delta RMC151 User Manual
Page 593: Controllers via ethernet/ip i/o
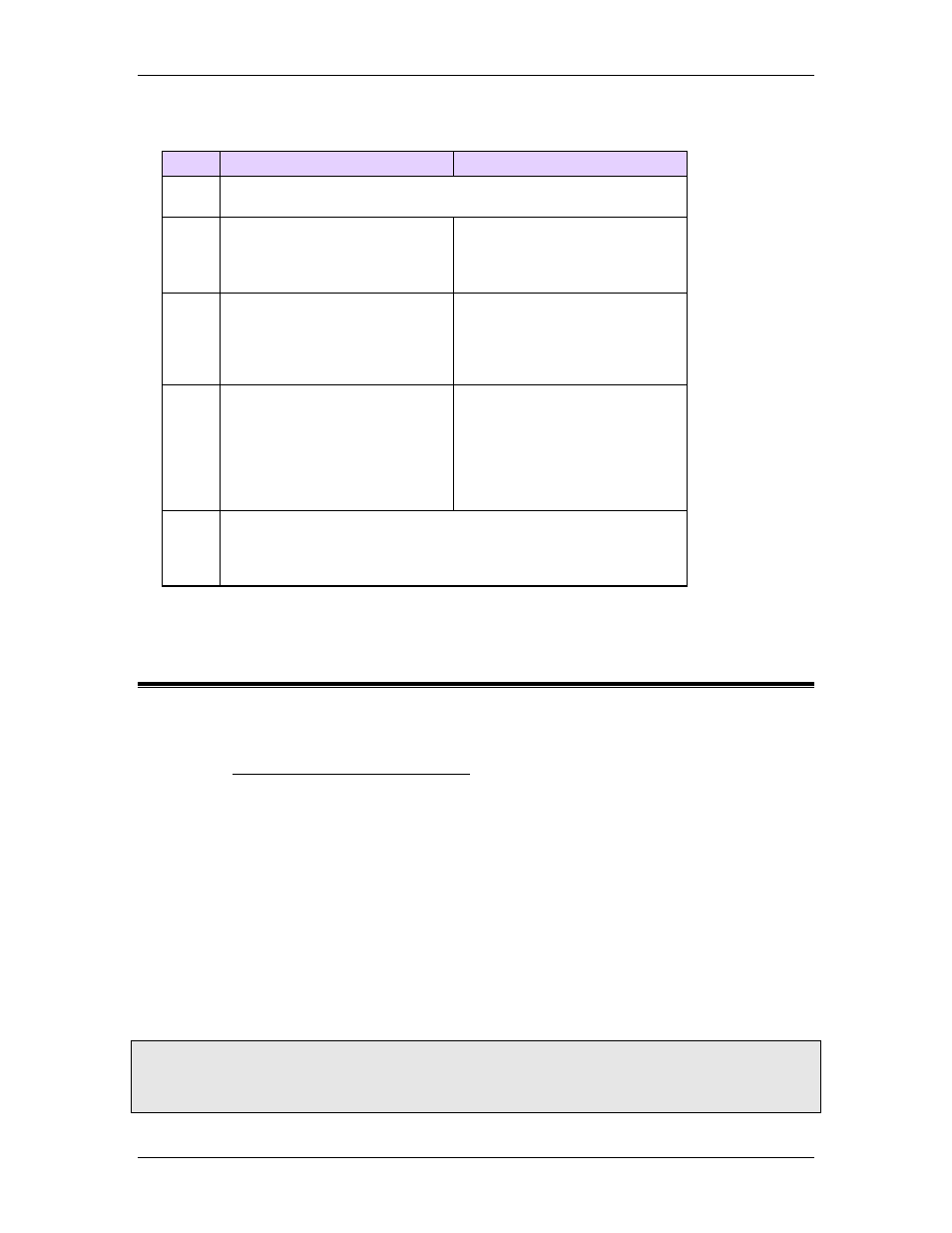
6 Communication
Some notes about setting up the control word for the SEND and RECV instructions for the
RMC75E are given below:
Word Bits 08 to 15
Bits 00 to 07
C
Number of words to read (1 to 512). The PLC supports reads
up to 990 words, but the RMC is limited to 512 words.
C + 1 Always 00 for RMCs.
Remote Network Address.
For RMCs, this value should be
set to the address of the RMC's
Ethernet network.
C + 2 Remote Node Number. For
RMCs, this value should be set
to whichever Node Number will
be mapped to the RMC's IP
address
Remote Unit Number. For
RMCs, this value should be 0.
C + 3 Port Number: 00 to 07. The
Port Number is used to allow
simultaneous communications
in the PLC. Use a different
number for each
communication that may be
requested simultaneously.
No. of Retries: 00 to 0F (0 to
15). For RMC communications,
this value should be between 2
and 5.
C + 4 Timeout: 0001 to FFFF (0.1 to 6553.5 seconds).The default
setting of 0000 sets a monitoring time of 2 seconds. For RMC
communications, this value should be set to 0001 or 0002 for
0.1 or 0.2 second timeouts.
6.11.10. Using Omron Controllers via EtherNet/IP I/O
Several Omron controllers support EtherNet/IP I/O communication. This topic describes how to
configure and use the Omron CS1 and CJ2 PLCs to communicate with the RMC via EtherNet/IP
I/O. For instructions on using the FINS protocol to communicate with an RMC from an Omron
PLC, see the Using Omron Controllers via FINS topic.
Determine I/O Data Locations in the RMC
EtherNet/IP I/O transfers data back and forth between the RMC and PLC at the Requested
Packet Interval (RPI). The user must specify which data items in the RMC should be sent
and received. Typically, this is data in the Indirect Data Map.
Set up the Indirect Data map so that one part contains all the data coming from the PLC
(Incoming Data), and another part contains all the data going to the PLC (Outgoing
Data). Make sure the Incoming and Outgoing Data areas in the Indirect Data Map do not
overlap.
The Outgoing Data typically includes RMC status items that the PLC always needs to keep
track of, such as actual positions and status bits.
The Incoming Data consists of items that the PLC needs to write to in the RMC. This is
typically variables and possibly command registers.
Note:
The Incoming and Outgoing Data locations need not be the Indirect Data Map. However, the
Indirect Data Map is usually the best choice. Other options are the Variable Table and the
command area.
deltamotion.com
573