Feedback resolution – Delta RMC151 User Manual
Page 81
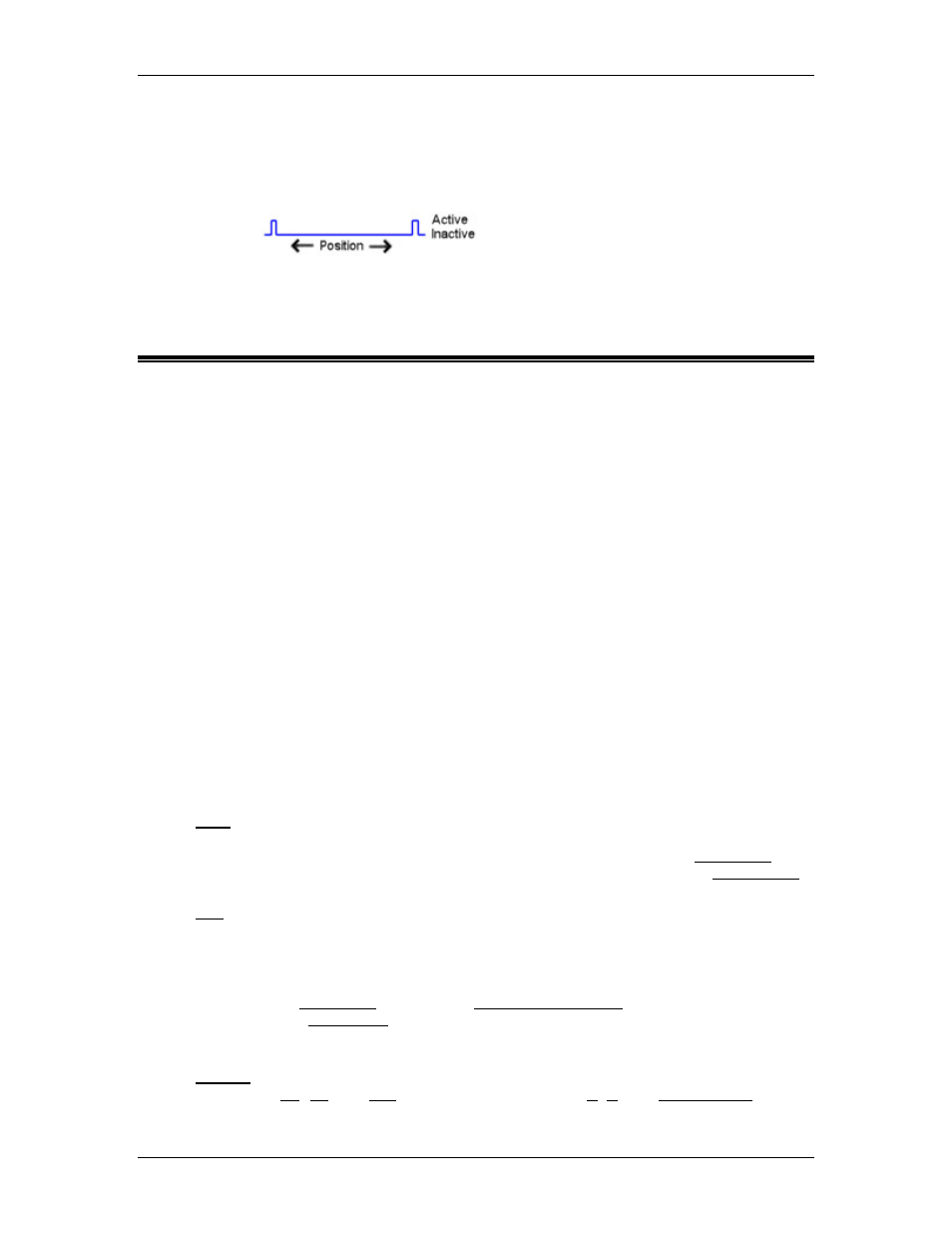
3 Controller Features
Good Practice
Do not install limit sensors such that they become active close to the end of travel, but
then become inactive at the end of travel, as shown below. In this case, commands in the
wrong direction will be allowed.
Poor Practice
3.2.7. Feedback Resolution
Feedback Resolution specifies the smallest increment that can be measured by the feedback
device (such as a position transducer or encoder). With analog feedback the resolution can
also be a function of the input circuit (Analog-to-Digital converter) on the controller.
Sometimes Resolution is referred to as Granularity.
Why is Feedback Resolution Important?
There are two main reasons why feedback resolution is important:
a. Positioning Accuracy
The controller cannot hold a position if it can’t accurately determine how close it is to
the desired position. It is generally necessary to have resolution that is several times
better than the desired accuracy. Notice, however, that high resolution is a
requirement for, but is not equivalent to high accuracy.
b. Quantization Noise
A less obvious, but equally important reason is quantization noise. Since velocity is the
change in position per unit of time, the velocity resolution is dependent on the position
resolution and the controller loop time. If the controller has a 1 millisecond loop time,
the velocity resolution will be 1000 times worse than the position resolution. The
acceleration measurement will be 1000 times worse than the velocity measurement.
On many systems the velocity measurement is used (with the differential gain) to
increase the system stability. Excessive quantizing noise on the velocity measurement
limits its effectiveness.
Maximum Feedback Resolution for the RMC
The maximum resolution available on the RMC for various feedback types is listed below:
•
For MDT Start/Stop or PWM feedback with a typical transducer having a gradient (or
calibration constant) of 9 µs/in, the resolution obtained by the RMC70 MA Module is
0.0005 inch with 1 recirculation. The resolution obtained by the RMC150 MDT Module
is 0.001 inch with 1 recirculation.
•
The SSI transducer sends the position information digitally, so the only limit is in the
transducer or encoder. Five micron resolution is common for linear SSI transducers,
and 8192 counts per turn is common for rotary encoders. Other resolutions are readily
available.
The RMC70 MA Module and RMC150 Universal I/O Module support 8 to 32 SSI bits.
The RMC150 SSI Module supports 8 to 31 bits. However, Delta recommends that
the SSI Counts value should not exceed 24 bits (16,777,216). See the Exceeding
24 Bits section below.
•
The RMC70 AA, A2, and AP2 modules and the RMC150 H, G, and Universal I/O
deltamotion.com
61