Delta RMC151 User Manual
Page 804
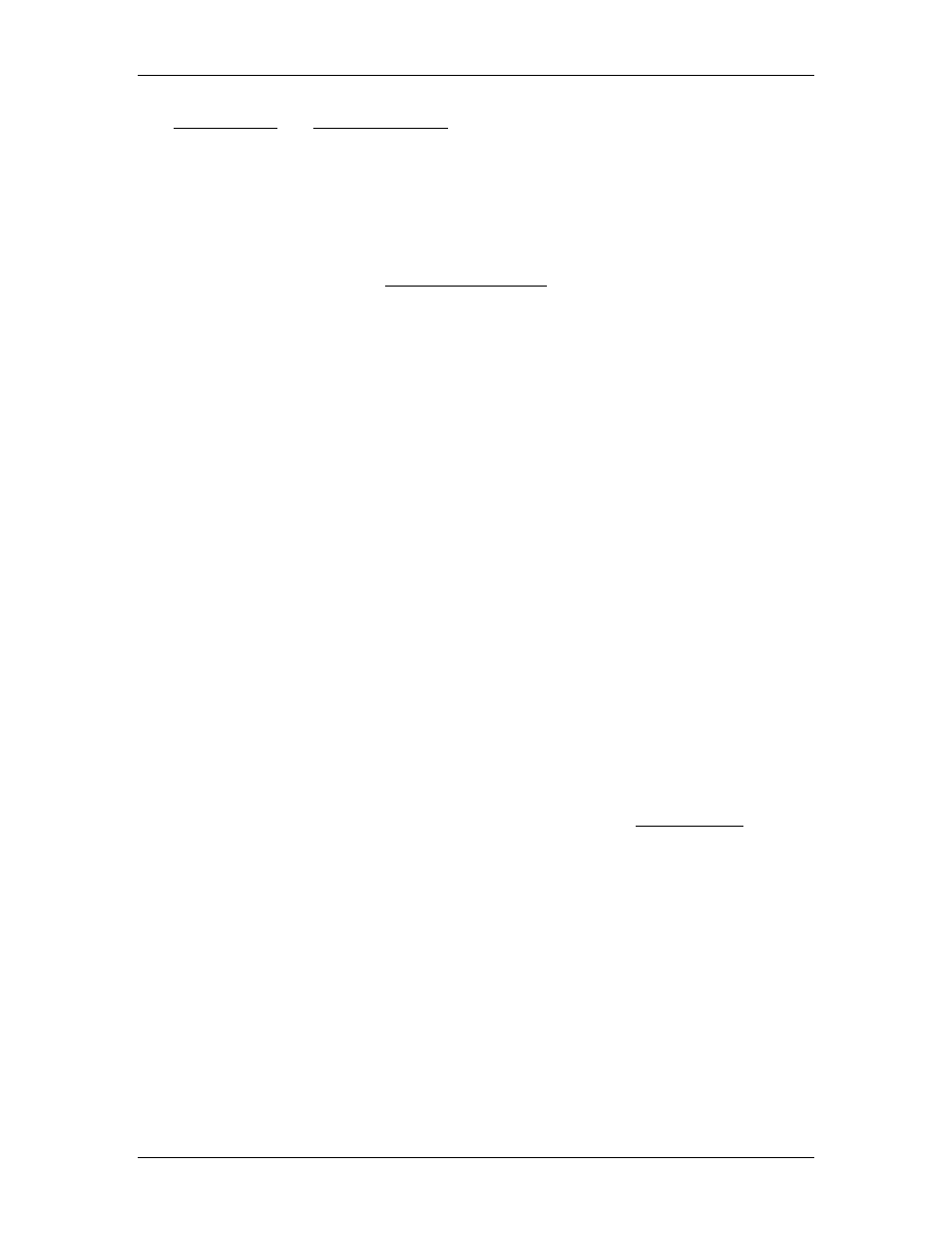
RMC70/150 and RMCTools User Manual
Advanced (88) and Gear Absolute (25) commands normally require that the axis be at
the correct starting point. However, if a transition has been enabled, then these
commands can be issued even though the axis is not at the correct starting point. When
the motion command is issued, the axis will move toward the requested profile (curve,
sine wave, gearing relationship, etc.) as defined by the transition command.
When the RMC powers up, transitions are disabled on all axes. To enable position axis
transitions, issue the Transition Rate (56) command. Once this command has been
issued, it does not need to be issued again, unless you wish to specify a different
transition, or if you need to re-enable transitions after disabling transitions. To disable
position transitions, issue the Transition Disable (55) command.
This command will not affect any transitions that are in progress.
Transition Types
This command provides the following transition options:
•
Seek (0)
The axis will move toward the requested profile using the Max Speed and Accel
Rate. When the position and velocity of the axis come close to the position and
velocity of the profile, the axis will "lock" onto the profile. Use this option to get to the
requested profile quickly and smoothly.
•
Reach (1)
The axis will move toward the requested profile using the Max Speed and Accel
Rate. When the position reaches the position of the profile, the axis will "lock" onto
the profile. Notice that this option does not require that the velocities be close when it
locks on, and therefore may cause the axis to jerk. Use this option to get to the
requested profile as quickly as possible.
•
Superimposed (2)
A trapezoidal or S-curve move using the Max Speed and Accel Rate will be
superimposed onto the requested profile such that the axis will reach the profile.
Notice that since the move is superimposed onto the profile, the axis will not
necessarily move at the specified speed and acceleration, but rather at the sum of the
speeds and accelerations from the requested profile and the superimposed portions of
the move.
This method will always guarantee that the axis will lock on to the requested profile,
even if the Max Speed and Accel Rate are slower than that of the profile. The
time it takes to lock on will be based on how far the axis position is from the
requested profile and on the Max Speed. For example, if the axis is at 3, the profile
is at 9, and the Max Speed is 6, it will take roughly one second to lock on. The
"lock-on" of the Superimposed method will be as smooth or smoother than Seek.
This superimposed move will be trapezoidal if the Requested Jerk axis parameter is
zero, or S-curve if the Requested Jerk is non-zero. See the Requested Jerk topic for
details.
Choosing a Transition Type
In general, try the Seek method first. If it takes too long to lock on, switch to Reach. For
either of these methods, make sure to set the Max Speed and Accel Rate to values
higher than that of the profile it is trying to follow. Otherwise, the axis may never catch
up to the profile. Notice that if the master register is stopped, then all 3 methods will
perform similarly.
If the transition is used for a gearing application, the behavior of any of the methods will
be the same if the master is not moving while the transition is taking place. If the master
is moving, and is a well-behaved Target Position, then the Seek and Reach methods will
both behave very similarly. If the master is moving, but is noisy, such as an analog
reference signal, then the Reach method will "lock in" the quickest, but may cause jerk.
The Superimposed method is not as useful as the first two methods, but it can provide a
more predictable "lock-on", as described above. Also, this method will always guarantee
784
Delta Computer Systems, Inc.