Using rotary motion – Delta RMC151 User Manual
Page 121
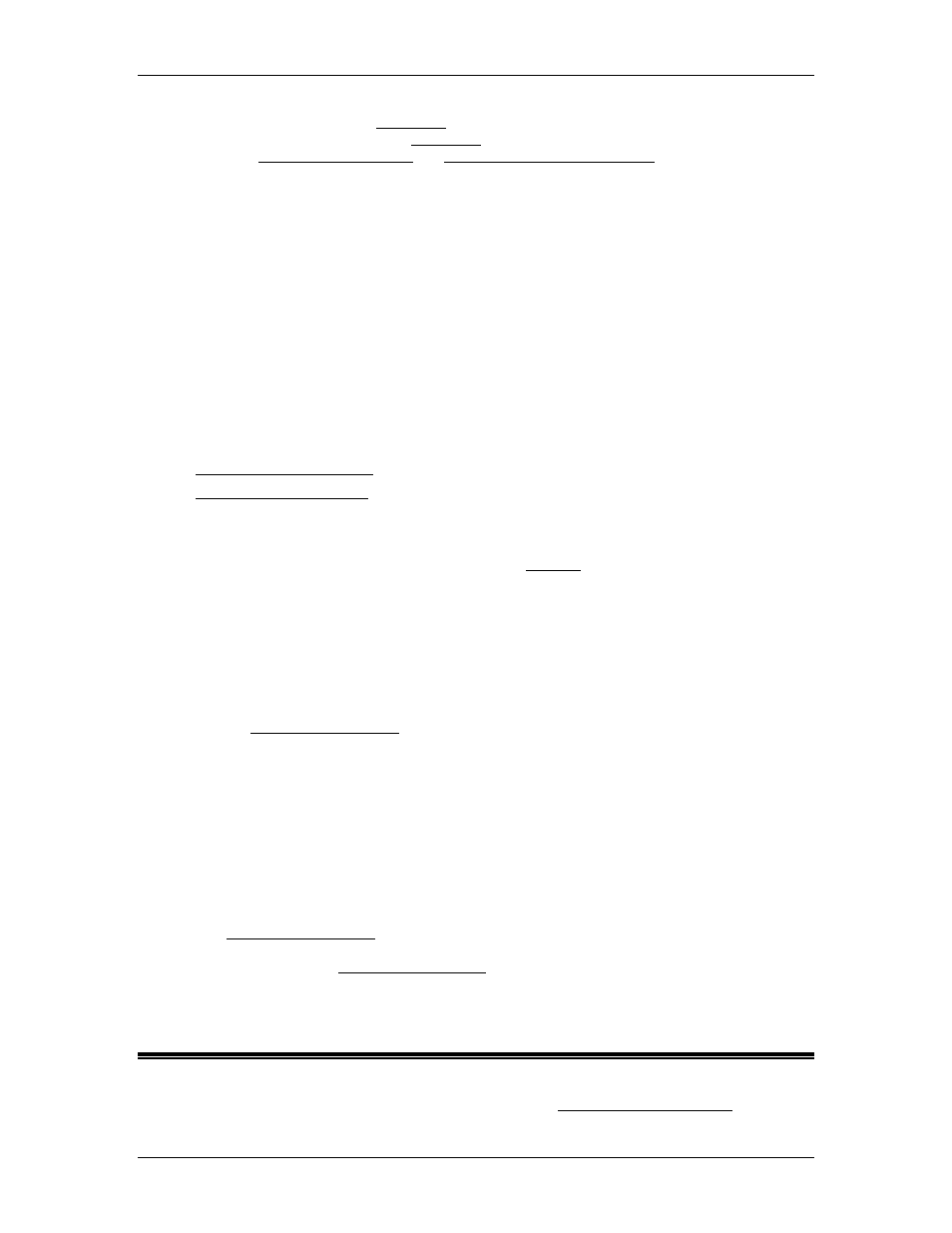
3 Controller Features
the error bit turns on, its Auto Stop setting determines what type of halt occurs.
Make sure the Following Error Auto Stop is set identically for each axis. Also make
sure the Open Loop Halt Ramp (or Closed Loop Halt Deceleration, depending on your
halt type) parameter is identical for each axis.
With these parameters set correctly, when you simultaneously issue identical motion
commands to each axis, the Target Position will be identical for each axis at all times. If
the Position Error on one axis becomes too large, the following error bit will turn on, and
all the axes will halt at the same time. Notice that the maximum allowable skew is twice
the Position Error Tolerance.
Ratioed Motion (Synchronized Unequal Travel Distances)
In this type of synchronization, the motion of the axes is synchronized such that all the
axes start and stop moving simultaneously, and at any point during the move, each axis
has completed the same percentage distance (or ratio) of its move. For example, if three
axes are at 0 inches, and are to move to 2, 4, and 6 inches, respectively, then at any
point in the move, the axes' positions will be at a 1:2:3 ratio.
Ratioed moves are useful when several actuators are moving a rigid structure around a
fulcrum. The axes do not need to start or stop at the same positions.
To achieve ratioed motion, use the Sync move commands:
•
•
Gearing
In this case, the motion of one axis must move at a rate proportional to the position or
speed of another axis or reference input. See the Gearing topic for more details.
Synchronizing RMCs
An RMC can synchronize up to 8 axes. To synchronize more axes, multiple RMCs are
needed. There are several ways to synchronize axes across RMCs.
•
Synchronize all axes to a single axis
This applies to applications such as gearing multiple axes to a single feed chain. A
transducer provides the master positions, to which all the other axes are synchronized
to. A quadrature encoder signal can be daisy-chained to multiple RMC QUAD modules.
Or, the Universal I/O Module can be used to daisy-chain SSI position data to multiple
RMCs. An analog position signal can also be connected to multiple RMCs.
•
Start identical motion simultaneously
If the axes need only do identical motion, then the motion can be started
simultaneously using a discrete output to trigger each RMC.
•
Via communications
If the axes need only do identical motion, and do not require very tight
synchronization, then the motion can be started simultaneously via the communication
channel. The communication channels do exhibit a certain amount of latency and
jitter.
•
UI/O Inter-Module Communciation
The Universal I/O Module can exchange data between RMC150s each loop time.
Therefore, this is suitable for tight synchronization of motion between controllers, such
as gearing. See the Universal I/O Module for details.
3.6.2. Using Rotary Motion
This topic describes and provides examples of how to use rotary motion with the RMC series
motion controller. For a description of rotary axes, see the Axis Type: Rotary/Linear topic.
deltamotion.com
101