Gearing, E gearing – Delta RMC151 User Manual
Page 129
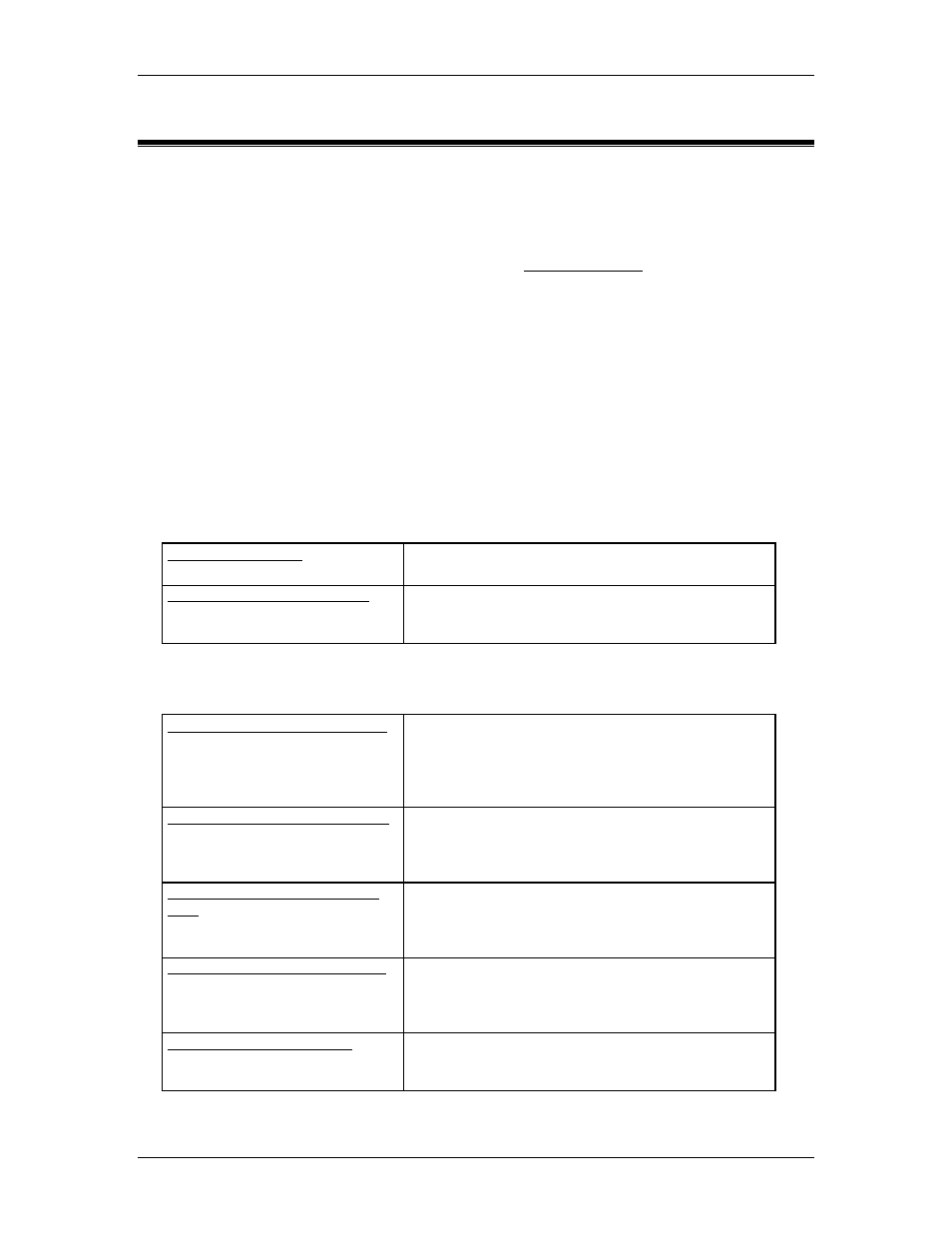
3 Controller Features
3.6.4. Gearing
Gearing is used when one axis (the slave axis) must move incrementally and proportionately
to a register (the gear master), which is typically the position or velocity of another axis. The
RMC has several commands to cover a wide range of simple and advanced gearing
applications. This topic describes the basics of gearing and gives an overview of the gearing
commands.
If you need to gear using a non-linear profile, see the Curves Overview topic.
In general, to gear an axis, issue a gearing command to the axis to be geared (the slave axis).
The axis will remain geared until another command is issued to the axis. A register does not
need to do anything to become the master of a gearing relationship. The slave axis will select
its gear master.
The RMC provides both relative gearing, which defines only the rate at which the slave moves
based on the rate of the master, and absolute gearing, which defines exactly the position of
the slave based on the value of the master.
Gearing Commands
The RMC offers the following gearing commands:
Absolute Gearing Commands
Absolute gearing defines exactly the position of the slave based on the value of the
master. The absolute gearing commands work very well for making an axis follow a
reference input (half axis).
Sets up an absolute linear gearing relationship and
will make the axis follow that relationship.
Sets up an absolute linear gearing relationship for
pressure/force and will make the axis follow that
relationship.
Relative Gearing Commands
Relative gearing defines the rate at which the slave moves based on the rate of the
master.
Gear Pos (Clutch by Rate) (39)
Gears the position of an axis to a master. The
clutching is done such that the slave axis ramps its
target velocity using the acceleration and jerk
parameters until it reaches the synchronized gear
ratio.
Gear Pos (Clutch by Time) (30)
Gears the position of an axis to a master. The
clutching is done such that the gear ratio ramps
from the current ratio to the specified ratio in the
specified time.
Gears the position of an axis to a master. The
clutching is done such that the master and slave
synchronize exactly at the requested positions.
Typically used in flying-cutoff type applications.
Gear Vel (Clutch by Time) (31)
Gears the velocity of an axis to a register. The
clutching is done such that the gear ratio ramps
from the current ratio to the specified ratio in the
specified time.
For very advanced gearing applications. It is
intended to be used in user programs along with
mathematical calculations.
Gearing with Motion Limits Commands
deltamotion.com
109