Pneumatic control, Pneumatic cylinders – Delta RMC151 User Manual
Page 205
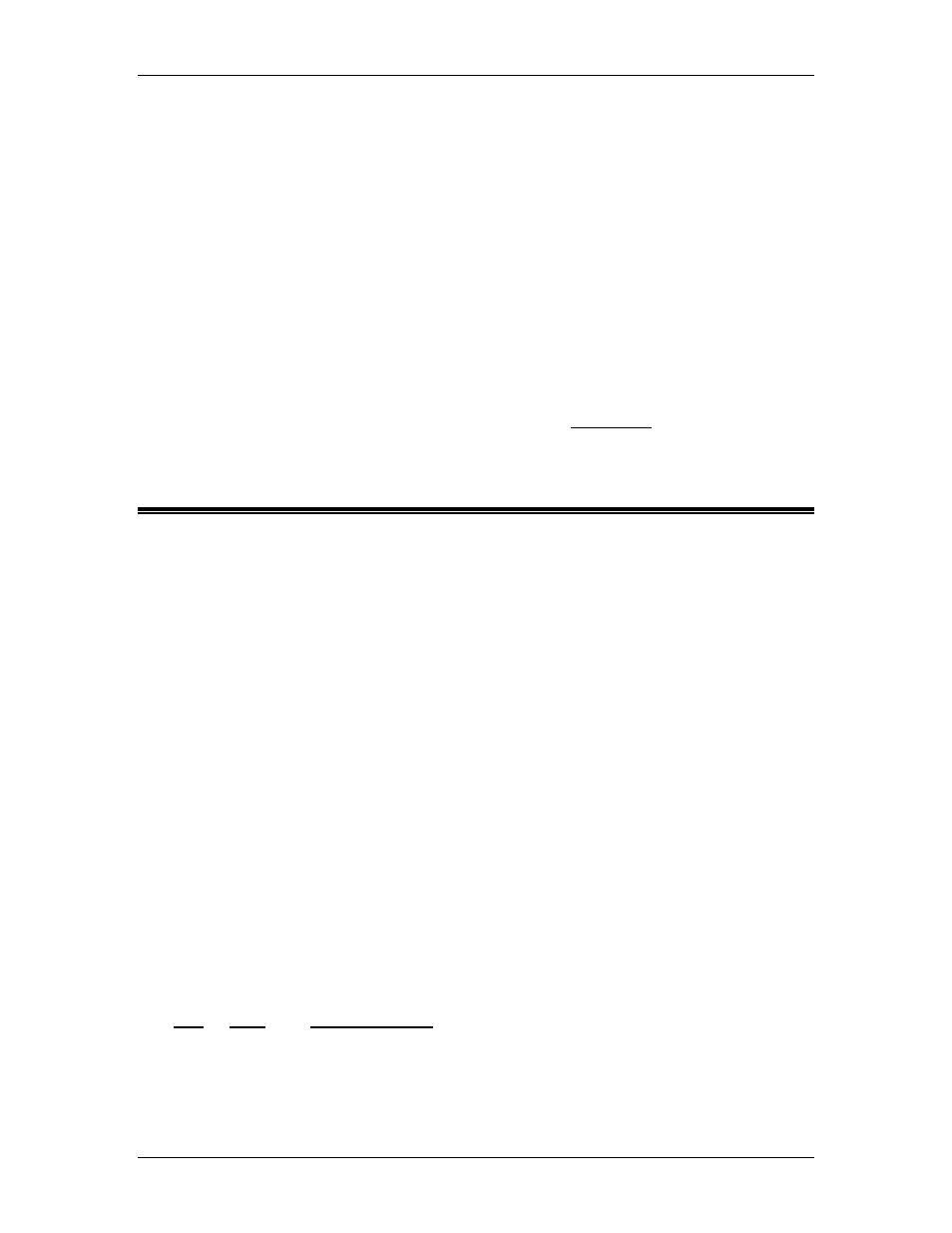
3 Controller Features
performance significantly, Delta does not recommend using valves with overlapped spools
– in particular for high performance applications or for pressure control.
Position-Pressure/Force Control
Hydraulic cylinders are ideal for applications where large forces must be applied to a load,
and the RMC includes control modes and parameters specifically for these types of
applications.
Active Damping and Acceleration Control
Active Damping uses Acceleration or force feedback to increase the stability of systems
with heavy loads relative to the cylinder diameter. This can increase the performance of a
hydraulic system without significant increases in cost from increasing the size of the
cylinder, valve and power unit.
Specialized Commands
The RMC has several commands that allow you to obtain the highest performance
possible from your hydraulic system or control difficult applications by combining Open
Loop and Closed Loop control in a single move. See the Quick Move command.
3.11.3. Pneumatic Control
The RMC family of motion controllers excels at pneumatic motion control applications that
demand precise, smooth motion.
Pneumatic Control has been serving industry for a long time and provides several advantages,
not the least of which is less costly devices, clean operation and lower maintenance costs.
However, precision and smooth motion has been elusive because of inherent drawbacks to
pneumatics. The major drawback is the compressibility of air. This drawback has been
minimized with new motion control techniques.
The RMC gives the user an option to replace start/stop or ”bang-bang” control that cause
shock and wear allowing machines and equipment to last longer. This is done with motion
controllers and by using feedback from position and pressure sensors. The RMC then controls
the servo proportional valve to eliminate banging and bottoming out at the ends of cylinders.
Use of proportional servo valves also allows a better option for accurate control in place of
using a pressure relief valve. Delta recommends pressure relief valves be used for relieving
pressure and not for controlling motion or pressure.
Precise midpoint positioning is also easily done with an RMC motion controller using servo
valves by moving the spool to meter air in and out of a cylinder. Pneumatic motion control
that is fast and smooth can make a system stiffer and act much like an elecro-mechanical
system at a much less expensive cost.
High-performance motion control requires a servo valve and a high-resolution position
transducer. For optimal control, a low-friction cylinder should be used. In addition, for the best
control, either pressure transducers or accelerometers should be used.
Once the pneumatic system has been set up and tuned, it can be controlled much like any
typical hydraulic or electric servo system.
Pneumatic Control Options
The RMC has several options for pneumatic control:
PID or I-PD with Active Damping with force feedback (load cell or pressure
transducers) or accelerometers
Easy to tune without overshooting; smooth.
Force Feedback can be a load cell or differential force, which requires two pressure
transducers; one on each end of the cylinder.
deltamotion.com
185