Command: enter pressure/force control (time) (45), Enter pressure/force control (time) (45), R enter pressure/force control (time) (45) – Delta RMC151 User Manual
Page 815
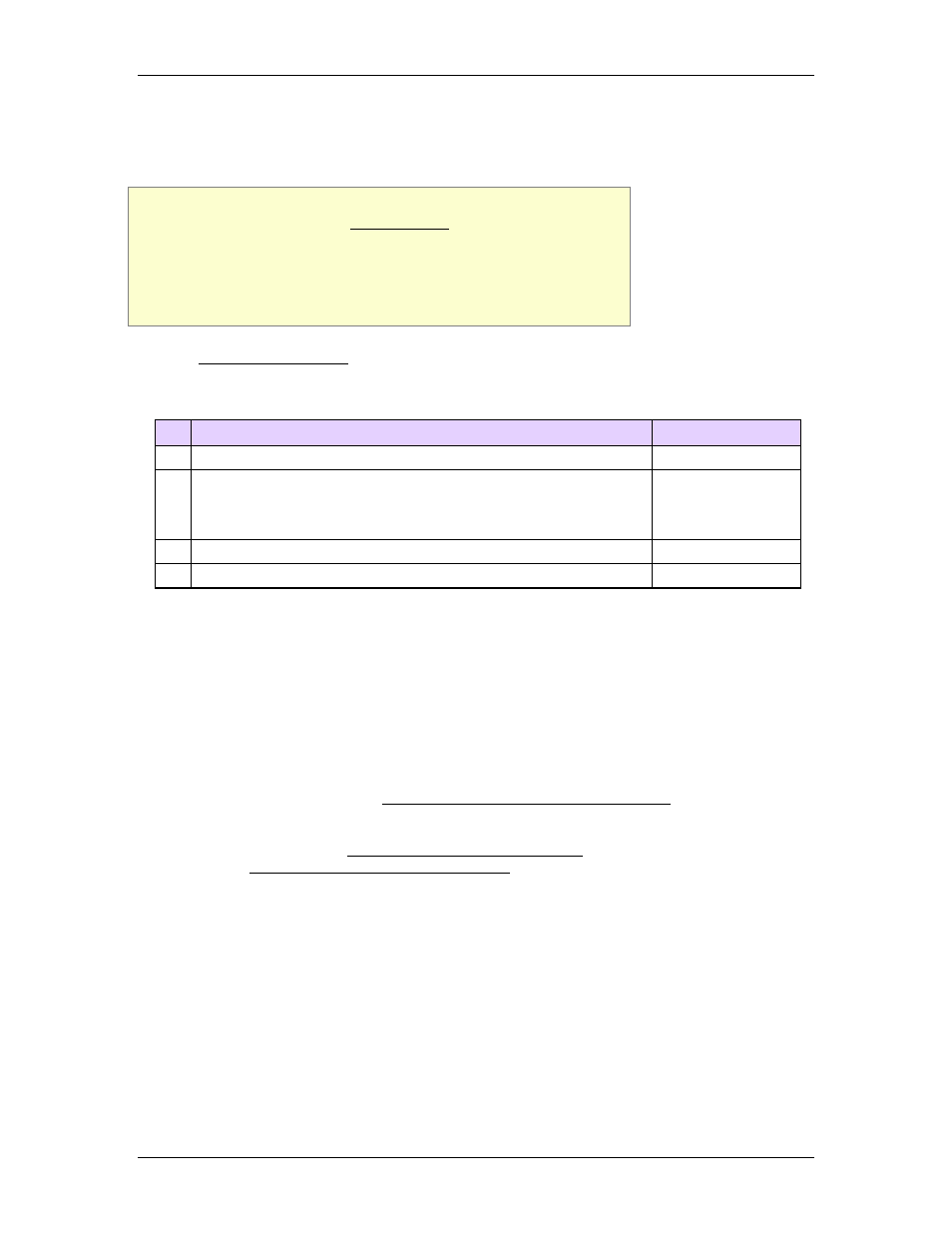
8 Command Reference
8.5.1.7. Command: Enter Pressure/Force Control (Time)
(45)
Supported Axes: Pressure/Force Control Axes
Firmware Requirement: 2.50 or newer
Hardware Limitations: RMC75S: versions 2.1D or newer only
RMC75P: versions 2.1E or newer only
RMC75E: No limitations
RMC150E: No limitations
See the Commands Overview topic for basic command information and how to issue
commands from PLCs, HMIs, etc.
Command Parameters
# Parameter Description
Range
1 Requested Pressure/Force (Pr or Fr)
any
2 Ramp Type
•
Linear (0)
•
S-curve (1)
A valid integer as
described
3 Time for Ramp (sec)
≥ 0
4 Integrator Preload (%)
-100% to 100%
Description
This command enters pressure or force control and then ramps to the requested
Pressure or Force in the specified Time for Ramp. A Linear Ramp Type will ramp the
pressure or force linearly until it reaches the Requested Pressure/Force. An S-curve
Ramp Type will provide a half s-curve ramp to the Requested Pressure/Force.
Upon entering pressure or force control, the Target Pressure or Target Force will be set to
the Actual Pressure or Actual Force. The Target Pressure or Target Force will then be
ramped to the Requested Pressure/Force in the specified Time for Ramp.
This command may cause the pressure/force rate to change suddenly at the transition, as
shown in the plot in the example below. If this is a problem, try using a shorter Time for
Ramp, or consider using the Enter Pressure/Force Control (Auto) (44) command, which
will automatically ramp at the current Actual Pressure/Force Rate (depending on the
tuning), eliminating the sudden change in rate. Another option is to create a user
program that issues the Hold Current Pressure/Force (19) command, then immediately
issues the Ramp Pressure/Force (S-Curve) (41) command.
The Integrator Preload specifies the value that the Integral Output Term should be set
to when transitioning into pressure/force control. The Preload is specified as a percentage
of the Output Scale (typically 10V), and is not affected by the pre-transition integrator
state. Typically, this can be left at the default value of 0. If the pressure/force exhibits a
drop upon entering pressure/force, increase this value to help smooth the transition.
Example
Consider a hydraulic press that must move toward the material to be pressed, transition
to pressure control and hold a certain pressure.
The user program below shows a possible sequence of steps.
Step 0 issues a Move Absolute command to move the axis to a position beyond where it
expects to encounter the material. The Step 0 Link Type waits for the Actual Pressure to
exceed 1000, then it goes to Step 1 which issues an Enter Pressure/Force Control (Time)
deltamotion.com
795