Delta RMC151 User Manual
Page 132
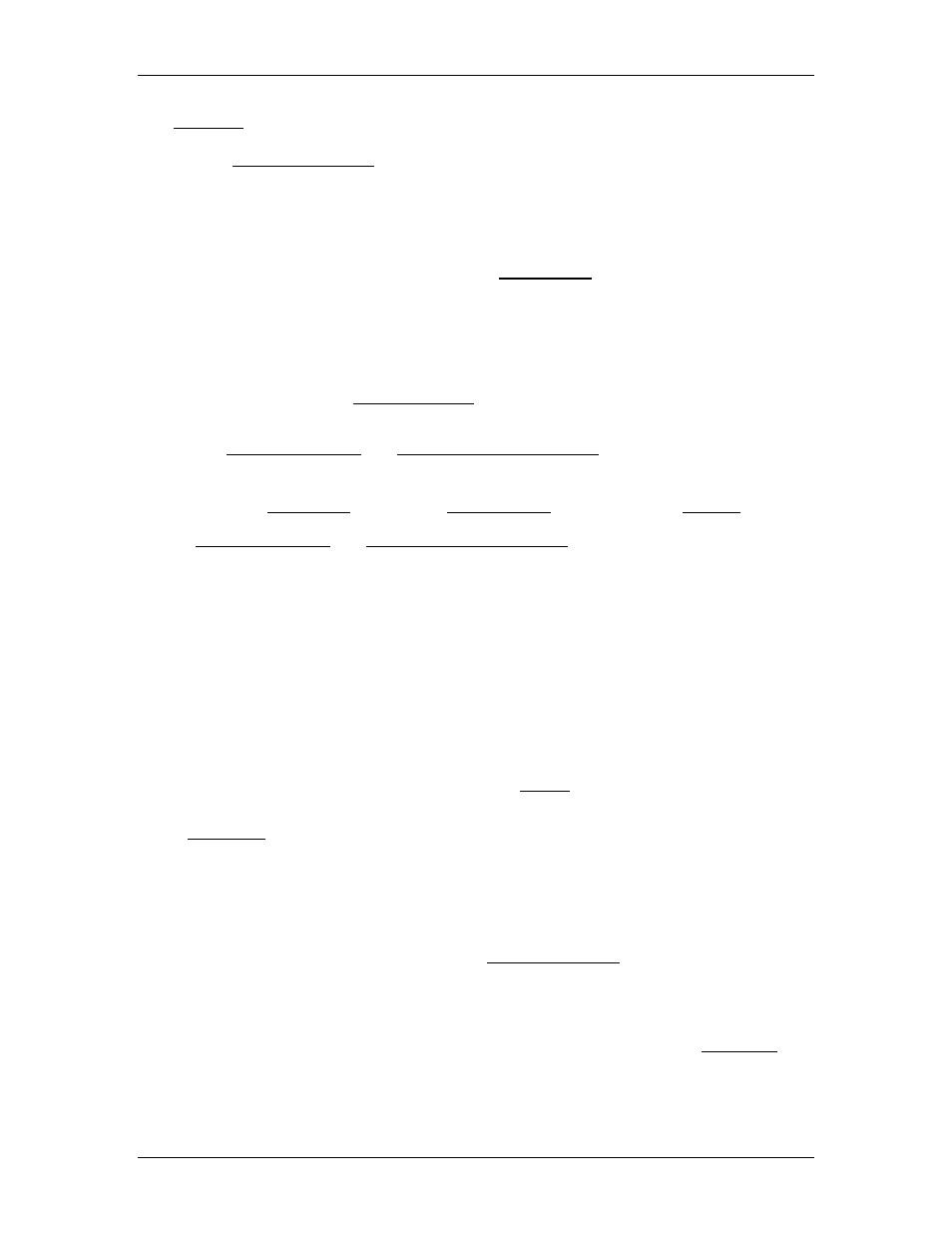
RMC70/150 and RMCTools User Manual
Transition command must previously have been issued to the axis to define how the axis
should move from it's current position onto the gearing relationship.
See the Transition Rate (56) command or more details.
Possible Gear Masters
The gear master can be any register in the RMC. A register does not need to do anything
to be a gear master. Most registers in the RMC are not useful as a gear master. Some
practical gear masters are described below:
•
Target Position or Actual Position of a control axis:
In this case, the axis is geared to the Target or Actual Position (or pressure or force)
of another control axis. For example, one motor may need to gear to another motor,
or one cylinder may have to move at the same rate as another cylinder. Typically, if
you are gearing to a control axis, gearing to the Target Position provides smoother
motion than gearing to an Actual Position because Actual Positions, as an actual
feedback signal, tend to be less smooth due to transducer noise and quantization.
•
Actual Position of a reference input (half axis):
In this case, the axis is geared to the position (or pressure or force) of a reference
input, such as from a joystick, an analog output from a PLC, or a belt position sensor.
The Gear Absolute (25) and Gear Absolute (Prs/Frc) (59) commands work very well for
this type of application.
•
A Variable:
Using the Expressions command in User Programs, you can create a Variable that
varies in time. By gearing to the variable, you can move the axis in that profile. The
Gear Absolute (25) and Gear Absolute (Prs/Frc) (59) commands work very well for this
type of application.
The RMC will process the slave after the master, which reduces latency in the slave axis—
as long as there are no g"gear chains". For example, if axis A is geared to axis B, which
is, in turn, geared to axis C, there is no guarantee that C will be processed before B which
will be processed before A. However, if A and B are both geared to directly C, then C will
be processed before both A and B.
Noisy Masters
Gear masters that are not very smooth, such as Actual Positions or reference inputs, may
cause chatter in the slave axis. The velocity, acceleration and jerk of the slave are
calculated from the master. Any noise on the master will be exaggerated in these
calculations, especially the acceleration and jerk. To reduce chatter, you may need to set
the Acceleration Feed Forward and Jerk Feed Forward to 0 on the slave axis.
If the gear master is a reference input, it can be filtered to make it smoother.
Using a Virtual Axis as a Gearing Master
A virtual axis can be used as a gearing master axis. It is sometimes desirable to gear to a
virtual axis rather than executing the motion as a function of time. All the axes geared to
the virtual axis can be sped up or slowed down by speeding up or slowing down the
virtual axis. The virtual axis can even be moved backwards causing the geared axes to
back up too. This cannot be done using time-based commands.
When using a virtual axis as a master as described above, it is often useful to set it up as
a rotary axis because it will never need to be reset. When used as a master, the virtual
axis is typically commanded to move with a Move Velocity (37) command. Moving it at 1
unit/sec as the standard velocity makes gearing ratio calculations very easy. The
acceleration and deceleration provide a smooth start and stop for the geared axis.
Halt Groups
For safety, both the master and slave axis should be included in the same Halt Group. If
one axis in a Halt Group halts due to an error, all the other axes in that halt group will
also halt.
Target Generator Components
112
Delta Computer Systems, Inc.