Using an ethernet/ip i/o connection, E using an ethernet/ip i/o connection, E using an ethernet/ip – Delta RMC151 User Manual
Page 470: I/o connection, Ip address collision detection (acd), Advanced multicast settings
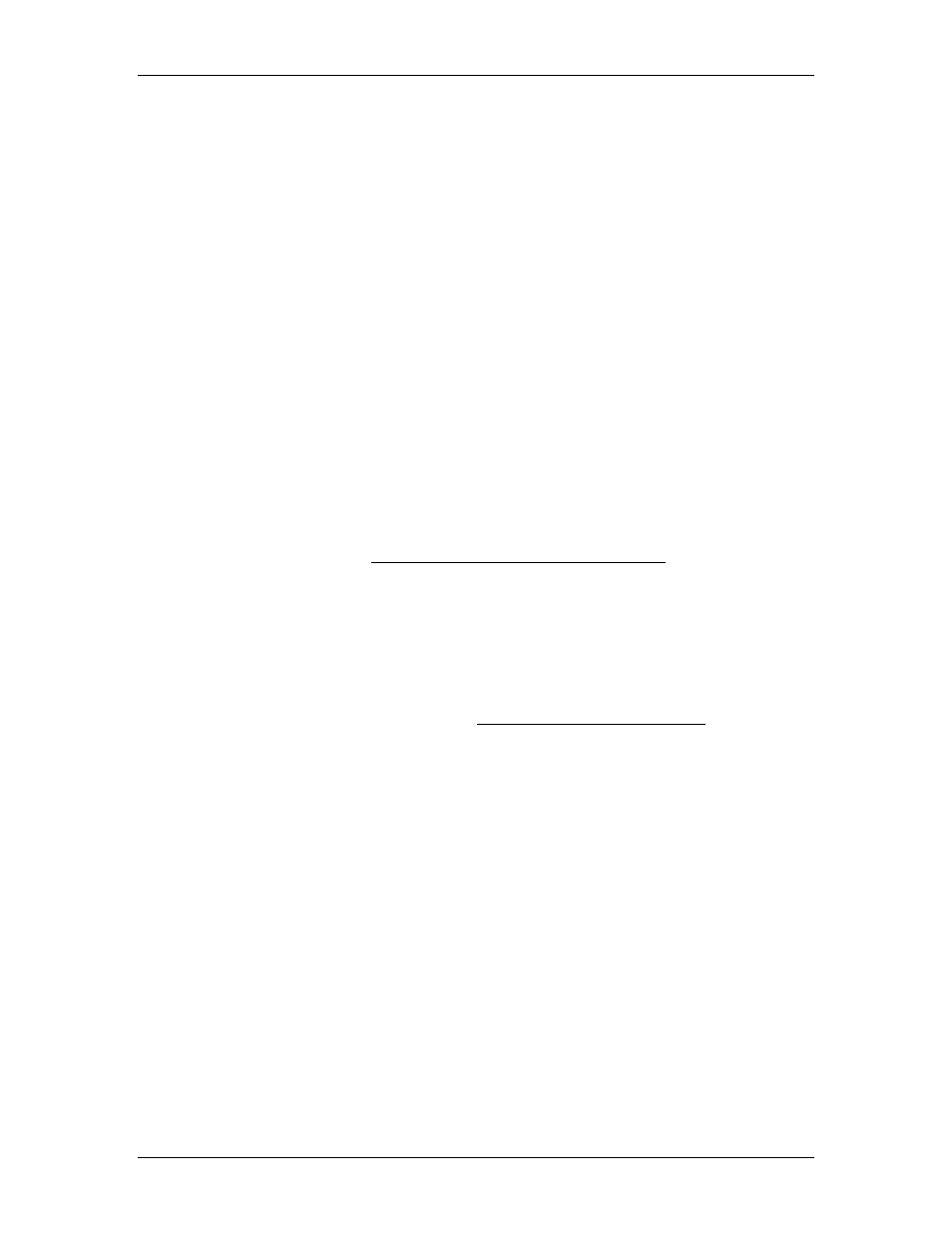
RMC70/150 and RMCTools User Manual
any system that will use 802.1D/Q priority tagging. See the EtherNet/IP Settings Page
topic for more details.
DiffServ Code Point (DSCP) marking is enabled by default. If you are using Rockwell
Automation Ethernet modules with older firmware, and RMC firmware 3.41.0 or newer,
you may need to disable this feature. See the EtherNet/IP Settings Page topic for more
details.
IP Address Collision Detection (ACD)
IP Address Collision Detection (ACD) detects duplicate IP addresses. This feature is
enabled by default, and is typically best left enabled. However, in situations where the IP
address must be available quickly and the risk of duplicate IP addresses is deemed low,
users may elect to disable Address Collision Detection. See the EtherNet/IP Settings Page
topic for more details.
Advanced Multicast Settings
In addition to the standard settings described above, the RMC provides advanced
multicast I/O connection settings. These include the ability to override the default
multicast address and Time To Live (TTL) value. See the EtherNet/IP Settings Page topic
for details on these settings.
6.8.10.6.3. Using an EtherNet/IP I/O Connection
This topic describes how to control the RMC over an EtherNet/IP I/O connection. For details on
setting up a connection, see the Setting up an EtherNet/IP I/O Connection topic.
Understanding the Sync Register
The I/O data can operate in two modes: with a Sync Register and without a Sync
Register. When using a Sync Register, the first Input Data register and first Output Data
register are each reserved as a Sync Register, and the RMC processes incoming data only
when the Sync Register changes. When not using a Sync Register, the RMC processes
incoming data each time any register in the block changes.
The Sync Registers show up in the Input and Output Data images in the PLC. In the RMC,
they are only visible in the Event Log. See Troubleshooting EtherNet/IP I/O for details.
Why Use a Sync Register?
The Sync Register gives the user tight control over synchronization between the PLC and
RMC. In applications that do not require this level of synchronization, the user can choose
to not include the Sync Register.
The synchronization provided by the Sync Register is useful when:
•
Treating writes to a block of registers as a consistent block.
Not all PLCs synchronize their I/O with the PLC scan. Therefore, while data is being placed
in the Output Data by the PLC program, a copy of the Output Data could prematurely be
sent to the RMC, mixing some old data with some new data. When the Sync Register is
used, this problem is avoided by the simple convention of having the PLC program update
the Sync Register after all other registers have been set to the desired values. The RMC is
then guaranteed to receive all the data in a single block.
•
Coordinating when Input Data has been updated to reflect an issued command.
This benefit is best demonstrated with an example. Suppose that an axis is holding
position with its In Position status bit set. If the PLC issues a new move command to a
new position, then we will see that the In Position bit will go off when the command is
first processed and remain off until the new move completes and the axis is at the new
position. How then does the PLC know when its copy of the In Position bit received in
the Input Data reflects the new command having been received? When the Sync Register
is used, the PLC can simply wait until the Sync Register coming from the RMC matches
450
Delta Computer Systems, Inc.