Delta RMC151 User Manual
Page 524
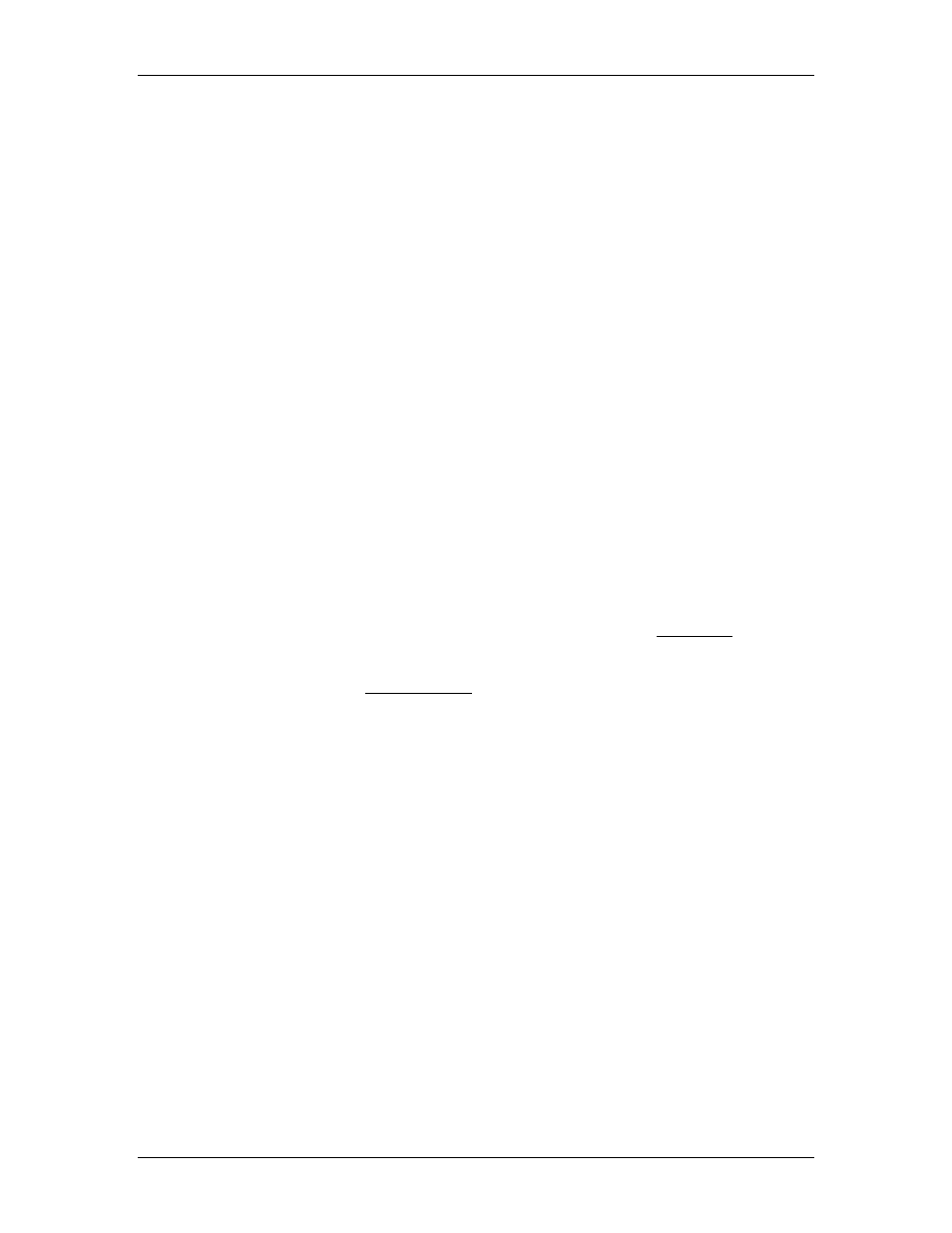
RMC70/150 and RMCTools User Manual
For example, suppose a PLC issues a command to axis 1 and then needs to wait for it to
get in position. To do this, the PLC must issue the command, wait for the command to be
received, and finally check the axis's In Position status bit. However, if the Axis 1 Status
Bits register is placed in the second block of registers, then even after the Command
Acknowledge bit matches the Command Request bit, indicating that the command
was received, we have no way of knowing whether the Axis 1 Status Bits register was
read from the controller before or after the command was issued, and thus could provide
the In Position bit from before the command was issued.
In short, do not put any registers that depend on a command being issued—such as axis
Status Bits, Error Bits, or Command Position—or the Read Response—which is tightly
coupled to the Read/Write Acknowledge bit in register 0—in the second block of
registers.
Example
Requirements
First, the user lists the desired registers to read from the RMC70:
•
Axis 0 Status Bits
•
Axis 0 Actual Position
•
Axis 1 Status Bits
•
Axis 1 Actual Position
•
Task 0 Current Step
•
Task 1 Current Step
•
The first 8 registers of the Variable Table.
In addition, the user would like to read some other registers occasionally.
Implementation
•
First, PROFIBUS communications requires that Axis 0 Status Bits register
must be in the first Response Block register, which is entry 0 in the Indirect
Data Map.
•
Second, the Read Response register is needed in order to read other
registers occasionally.
•
Third, the user determines which registers must be in registers 0-7 to
preserve consistency. The rest of the registers can then be placed in the
remaining registers.
The user chose to set up the Indirect Data Map like this:
504
Delta Computer Systems, Inc.