Using siemens s7 plcs via profinet, Siemens s7 plcs via profinet, Siemens s7 plcs – Delta RMC151 User Manual
Page 614: E using
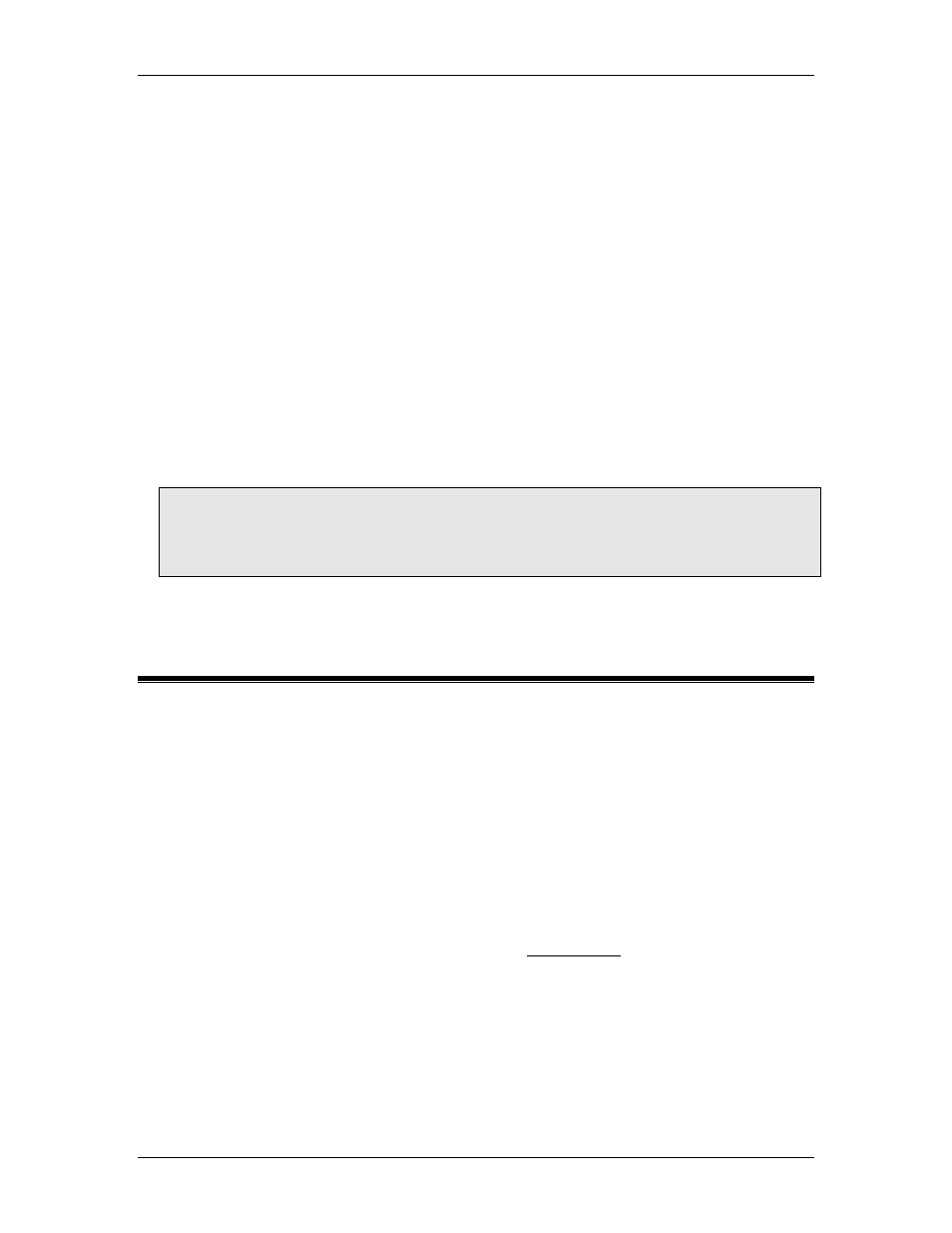
RMC70/150 and RMCTools User Manual
10. In the Device Shortcuts area of the Communication Setup dialog, click ADD. Enter
a name, such as "RMC75S".
11. Now, you must make sure the shortcut is assigned to the RMC75S on the Local and
Target tabs. In the Device Shortcuts box, make sure the shortcut you added is
selected. Then, on the Local tab, select the RMC75S, and similarly, on the Target
tab, select the RMC75S.
12. Click OK to close the Communication Setup.
To add a tag using the Device Shortcut (RMC75S, RMC75E, or RMC150E):
1. To add a tag, expand the HMI Tags node, and double-click Tags. Select the bottom
line in the Tag Name list.
2. In the Name box, enter a name, such as RMC_ActPos.
3. In the Type box, choose Analog. In the Data Type box, choose Floating Point.
4. In the Data Source area, choose Device.
5. The Address must be entered in direct format. The format is {::[ShortcutName]Fn:x}
, where n is the file number and x is the element number.
For example, with a device shortcut of "RMC75E" and the Axis 0 Actual Position tag
(address F8:8), the Address would be:
{::[RMC75E]F8:8}
6. Click Accept.
Note:
Using tags with direct addressing in a Numeric Display does not seem to work properly.
When using a Numeric Display, enter the direct address as the Value. The direct address
format is {::[ShortcutName]%MDn.x} , where n is the file number and x is the element
number, as described above.
6.11.12. Using Siemens S7 PLCs via PROFINET
Siemens offers several CPUs and Communication Processors (CPs) that support PROFINET,
including products in the S7-300, S7-400, and S7-1200 lines. The procedures below describe
using STEP 7 V5.5 with the S7 CPU 315-2 PN/DP, but the steps will be similar for other S7-
family products and versions of STEP 7 software.
The PROFINET IO connection can be configured for both cyclic and acyclic I/O data:
•
Cyclic I/O data is always exchanged between the PLC and RMC at the specified
update time. For example, status information from the RMC, and variables to be
written to the RMC would typically be part of the cyclic data. Cyclic I/O data is defined
by the Incoming and Outgoing Cyclic I/O Data. At the time of this writing (September
2010), Siemens S7 PLCs are limited to 63 registers in each direction.
•
Acyclic data is sent only when it is needed. For example, if the PLC creates a curve
and sends it to the PLC, that data would typically be sent via the acyclic data. Or, if
the PLC needs to read a captured plot from the RMC, that is also best done via the
acyclic data. Acyclic I/O data is defined by the Data Records. The maximum length is
8192 bytes, or 2048 32-bit registers.
Determine I/O Data Locations in the RMC
PROFINET IO transfers data back and forth between the RMC and PLC at the specified
update time. The user must specify which data items in the RMC should be sent and
received. Typically, this is data in the Indirect Data Map.
Set up the Indirect Data map so that one part contains all the data coming from the PLC
(Incoming Data), and another part contains all the data going to the PLC (Outgoing
594
Delta Computer Systems, Inc.