Position-pressure and position-force control, Controlling both position and pressure, Controlling both position and force – Delta RMC151 User Manual
Page 170: E position-pressure and position-force control
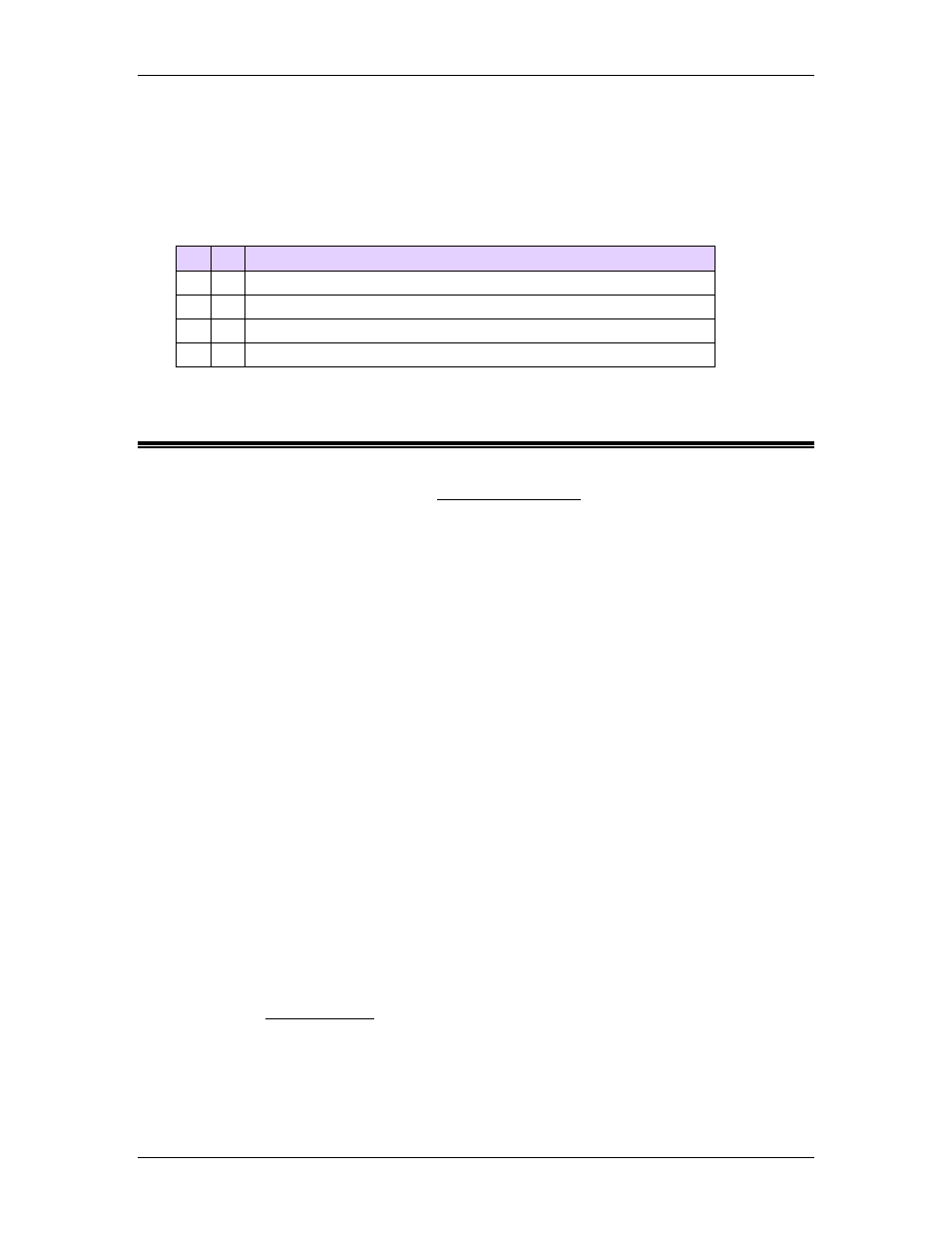
RMC70/150 and RMCTools User Manual
Pressure/Force Target Generator Done bit
This bit indicates that the Target Pressure or Target Force has reached the Requested
Pressure/Force. If the ramp is interrupted, e.g. due to a halt, the done bit will not be
set because the commanded motion was not completed. Notice that this bit does not
indicate whether the Actual Pressure or Actual Force has reached the Requested
Pressure/Force.
Pressure/Force Target Generator State A and B bits
B
A Description
0
0
The target generator is complete
0
1
Pressure/Force is accelerating
1
0
Constant
1
1
Pressure/Force is decelerating
3.7.3. Position-Pressure and Position-Force Control
This topic describes position-pressure and position-force control. For information on pressure
control only or force control only, see the Pressure/Force Limit topic.
Pressure/Force Control or Pressure/Force Limit can be used on position-pressure or position-
force control axes. Position-torque is identical to or position-force with a single-input force, or
position-pressure.
Required Hardware
A position-pressure or position-force axis requires the following RMC hardware:
•
Pressure-Enabled Controller
This is the term for an RMC that supports dual-loop control, such as position-
pressure or position-force.
o
RMC70: Requires the AP2 module.
o
RMC150E: Requires the pressure option (denoted as RMC151). This must
be specified when ordering the RMC.
o
One Control Output
o
One Position Input
This can be any type of position feedback supported by the RMC.
o
One or Two Analog Inputs
Two analog inputs are required only if you are using two pressure transducers for
differential force feedback.
Pressure or Force feedback requires analog feedback transducers (voltage or current).
The input range from the transducer must fall within the RMC supported ranges of ±10V
or 4-20mA. For the best resolution, the feedback should use a large portion of the ±10V
or 4-20mA range.
Define the Axis
The first step for pressure/force control is to define the axis. This means assigning the
physical inputs and analog Control Output to an axis in RMCTools.
1. Open the Axis Definitions dialog to define the axes.
2. In order to define the axes as you want them, you may need to first remove the
existing axes and add new axes. Or, you may be able to change an existing axis.
3. Whether you choose to change an existing axis or add a new axis, set the axis to the
following:
150
Delta Computer Systems, Inc.