Input data, Output data – Delta RMC151 User Manual
Page 467
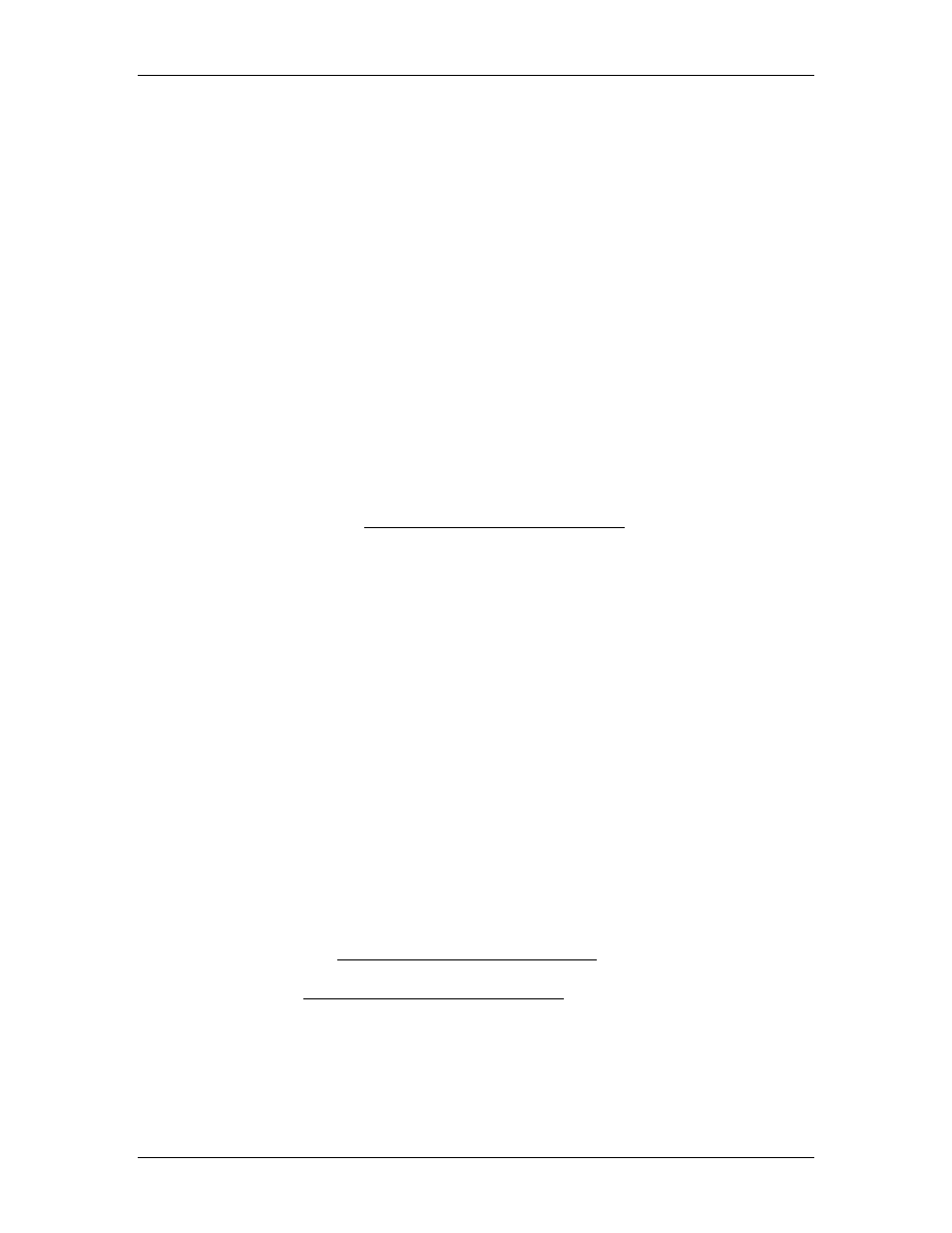
6 Communication
The RMC supports both multicast and unicast (point-to-point) I/O connections.
Traditionally, most EtherNet/IP I/O connections have been multicast, since Allen-Bradley
controllers did not support unicast I/O connections until RSLogix 5000 version 18.00.00
was released in March 2010. However, multicast connections are much more demanding
on the network bandwidth and require special switchgear (either routers or special
switches with IGMP snooping/querying capabilities) to limit the spread of multicast traffic
across the network. The RMC only requires multicast I/O connections when multiple I/O
connections will be established at once, which is quite rare. Therefore, in almost all cases,
unicast I/O connections should be selected whenever supported by the EtherNet/IP I/O
controller.
Input Data
The Input Data is the data produced by the RMC and sent to the PLC. By default, the
source of the Input Data is the Indirect Data Map, beginning with Indirect Data Map item
0. First, you must set up the Indirect Data Map in RMCTools to map to the RMC registers
you want to transfer. Typically, you would include Actual Positions, Status and Error Bits
for each axis of control, task status registers so the PLC can tell which user programs are
running, and any other registers of your choice. The Input Data source can be changed to
something other than the Indirect Data Map, as described below, but the Indirect Data
Map is used in nearly all EtherNet/IP I/O applications.
The size of the Input Data—up to 125 registers (500 bytes)—is specified in the PLC when
configuring the EtherNet/IP I/O connection. This should be set to the number of registers
you have set up in the Indirect Data Map, plus the Sync Register, if used. For details on
the Sync Register, see the Using an EtherNet/IP I/O Connection topic.
Once an EtherNet/IP I/O connection is established, the Input Data will automatically be
sent from the RMC to the PLC each RPI. The PLC can use the data whenever it needs it.
Setting the Input Data Source in RMCTools
To set the source in the RMC for the Input Data:
1. In the Project pane, expand the Modules folder, double-click the CPU module, and
choose EtherNet/IP.
2. Under Outgoing Cyclic I/O Data, in the Address of Outgoing Data box, type the
starting address of the data to have sent to the I/O controller each RPI. Use the
Browse button to use the Address Selection Tool to find the location you want to
use.
Notice that the length of the Input Data is specified in the PLC, not in RMCTools.
Output Data
The Output Data is the data sent from the PLC and consumed by the RMC. By default, the
destination of the Output Data is the Indirect Data Map. This allows the PLC to easily
write to whatever registers you have mapped into the Indirect Data Map, such as
variables and axis command registers. The destination of the Output Data can be
changed to something other than the Indirect Data Map registers, as described below.
However, the Indirect Data Map works very well for most applications.
The size of the Output Data—up to 124 registers (496 bytes)—is specified in the PLC
when configuring the EtherNet/IP I/O connection. The Output Data size must be the
number of registers you wish to write, plus the Sync Register, if used. For details on the
Sync Register, see the Using an EtherNet/IP I/O Connection topic.
Once an EtherNet/IP I/O connection is established, the Output Data is used to write to the
RMC. Refer to the Using an EtherNet/IP I/O Connection topic for details.
Setting the Output Data Destination in RMCTools
To set the destination in the RMC for the Output Data:
1. In the Project pane, expand the Modules folder, double-click the CPU module, and
choose EtherNet/IP.
deltamotion.com
447