Delta RMC151 User Manual
Page 749
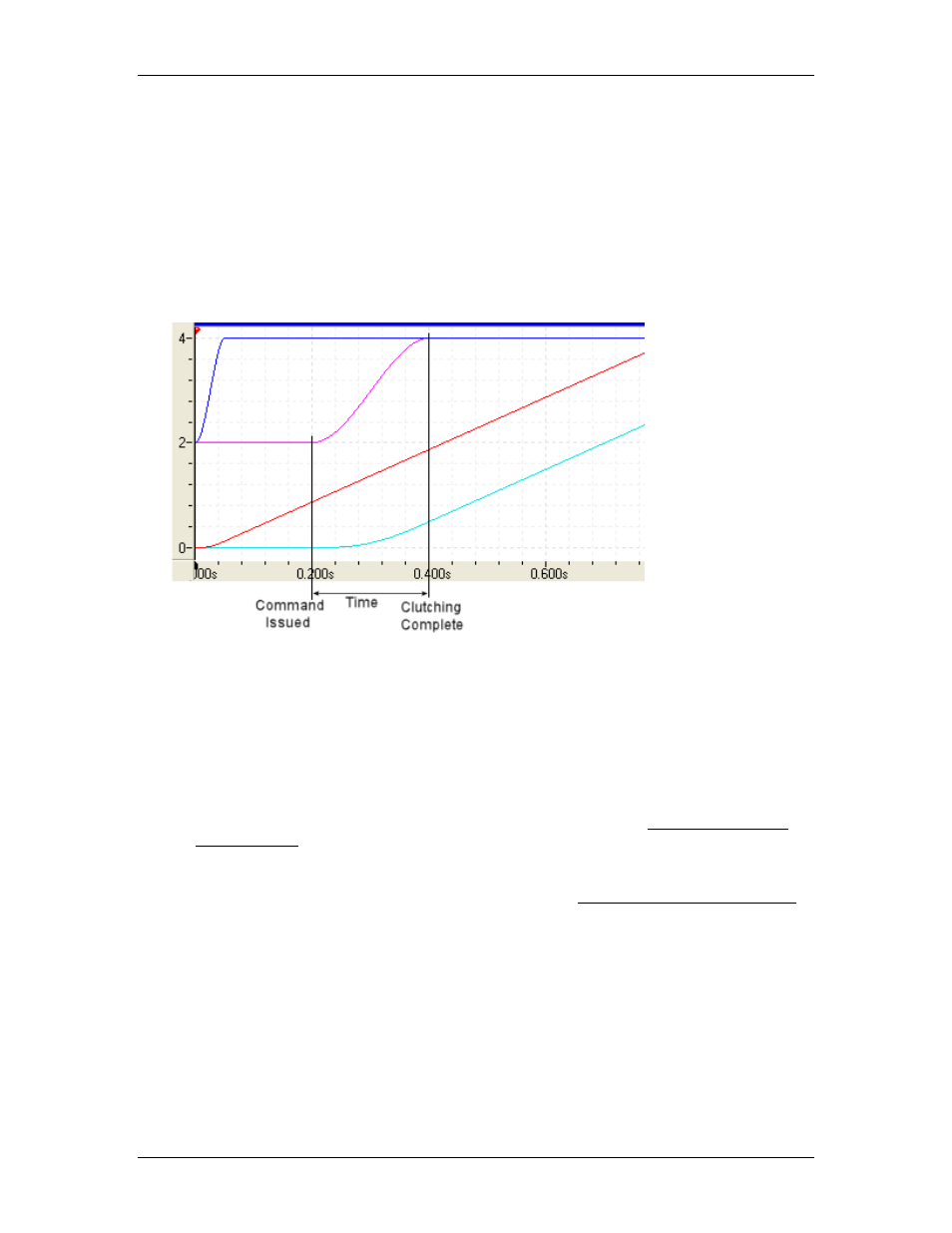
8 Command Reference
In this example, Axis 1 (slave) gears to Axis 0 (master) at a 1:1 ratio. Both axes start at
0 pu. The master starts moving at time 0. At 0.2 seconds, the following Gear Pos (Clutch
by Time) command is issued to the slave.
Numerator = 1
Denominator = 1
Master Register = _Axis[0].TarPos
Clutch Time = 0.2 sec
The plot below shows how the slave moves.
Legend:
— Master Position
— Master Velocity
—
Slave Position
— Slave Velocity
At 0.2 seconds, when the command was issued to the slave, it began ramping up the
velocity such that slave reached the specified gear ratio at 0.4 seconds.
Applications Not Suitable for Clutch by Time
The Gear Position command clutches based on time, which means it will reach the
requested gear ratio in the time specified. This command is not well-suited for the
following types of applications:
•
If Position at which Axis Reaches Gear Ratio is Important
The Gear Pos (Clutch by Time) command does not directly specify the position at
which the gear ratio will be reached. If the axis must reach the requested gear ratio at
a certain position, such as in flying cut-off applications, use the Gear Pos (Clutch by
Distance) (32) command instead.
•
If Maximum Velocity or Acceleration Must be Specified
The Gear Pos (Clutch by Time) command does not limit the velocity or acceleration. If
you need to limit the velocity or acceleration, use the Gear Pos (Clutch by Rate) (39)
instead.
Specifying a Register Address
When issuing this command from anywhere other than RMCTools, the addresses in the
Master Register command parameter must be entered as an integer value.
RMC addresses are represented in IEC format as:
%MDfile.element, where file = file number, and element = element number.
Use the following equation to convert a register address to integer format, N:
N = file * 4096 + element
deltamotion.com
729