Delta RMC151 User Manual
Page 768
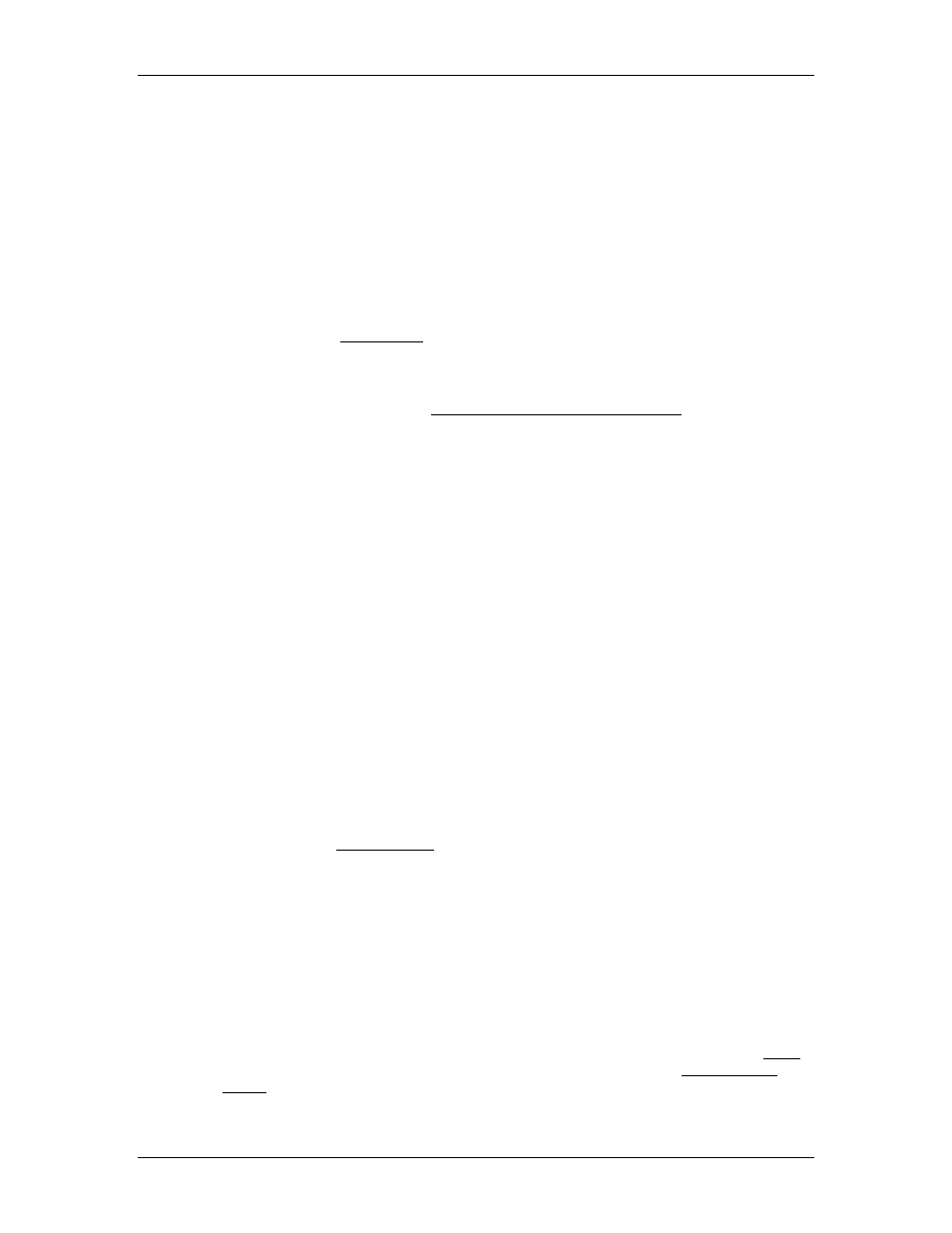
RMC70/150 and RMCTools User Manual
This command offers ultimate gearing flexibility and is useful if you need to specify an
arbitrary motion profile as a function of the master position. For example, if you know the
equation of the cam profile or cam profile segments you wish to create, you can use this
command.
This command is typically used for only a segment of a move, and you should always
issue another command after this one when the Done Status bit is set. This can easily be
done in the User Programs. You can issue several of these moves in a row to get the cam
profile you want, especially if you need to specify the gear ratio and gear ratio rate at
certain points. The Expression (113) command can be used to calculate the position, gear
ratio, and gear ratio rate at the specific master locations. Complex profiles may require
many individual segments using the Advanced Gear Move commands.
Typically, using this command requires knowledge of calculus and a thorough
understanding of using expressions in a user program. Notice that the Gear Ratio is the
first derivative of the slave position with respect to the master position and the Gear
Ratio Rate is the second derivative of the slave position with respect to the master
position.
This command is very similar to the Advanced Time Move Absolute (26), except that it
creates a profile based on a master position rather than time. The Final Velocity and Final
Acceleration of the Advanced Time Move are similar to the Final Gear Ratio and Final
Gear Ratio Rate of the Advanced Gear Move.
Specifying a Register Address
When issuing this command from anywhere other than RMCTools, the addresses in the
Master Register command parameter must be entered as an integer value.
RMC addresses are represented in IEC format as:
%MDfile.element, where file = file number, and element = element number.
Use the following equation to convert a register address to integer format, N:
N = file * 4096 + element
Example:
Register address %MD8.33 is 8*4096 + 33 = 32801.
Rotary Motion
The Master Direction and Slave Direction parameters of this command are for use on
rotary axes. For non-rotary axes, the direction parameters should be "Nearest". The other
options will have no effect. If the master register is not a Target Position or Actual
Position register, the master directions cannot be rotary.
On rotary axes, the direction parameters specify the direction of the Slave Sync position
from it's current position and the direction of the Master Start Distance from the Master
Sync Position. See the Rotary Motion topic for details on the meaning of the direction
options.
Direction Options
•
Negative (-1)
•
Nearest (0)
•
Positive (1)
•
Absolute (3)
Using the Advanced Gear Move in User Programs
Indexing Arrays
Typically, the Advanced Gear Move is programmed in a loop and cycles through an array
or arrays of positions, speeds, and/or accelerations. To do this, use the variable table to
set up arrays. A variable for indexing the array is also required. It must be of data type
DINT.
748
Delta Computer Systems, Inc.