Non-linear – Delta RMC151 User Manual
Page 108
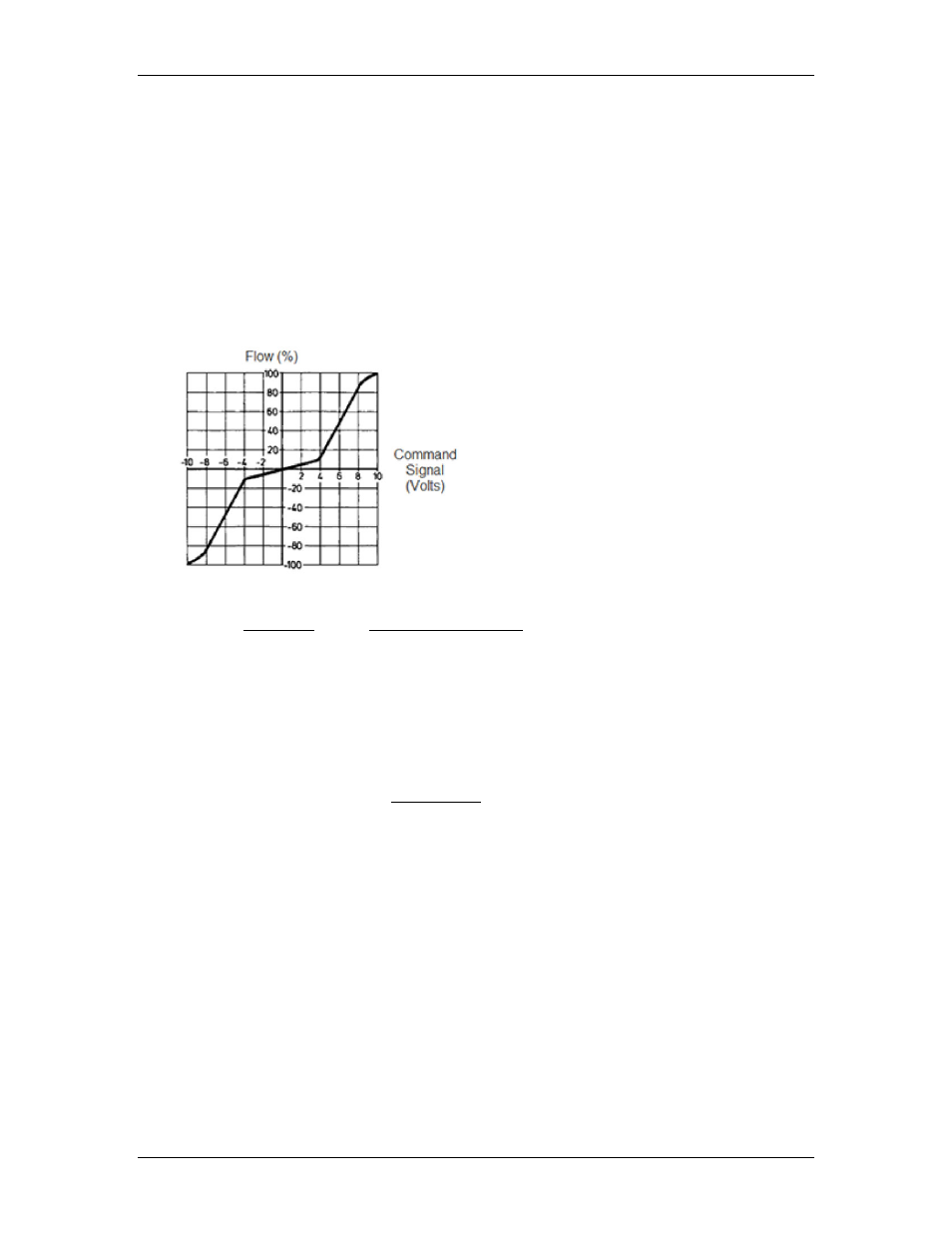
RMC70/150 and RMCTools User Manual
Delta does not recommend using non-linear valves for motion control if a linear valve is
available. When using a high-performance motion controller, there is usually no reason to use
a non-linear valve. Linear valves will perform better than non-linear valves, even with valve
linearization. Non-linear valves are typically only useful for valves directly controlled by hand
controls, such as a joystick.
Single-Point Valve linearization
The RMC75 and RMC150 motion controllers provide single-point valve linearization to
compensate for valves with one sharp "knee" or "kink" in the flow versus command signal
diagram, as shown in the Single-Knee Valve diagram below. This valve linearization
typically results in a drastic improvement in control. Using this method for other non-
linear valve types will provide some improvement, but will not provide optimum control.
Single-Knee Valve
To Apply Single-Knee Valve Linearization
1. In the Axis Tools, in the Axis Parameters Pane, and the All tab, expand the Output
section.
2. In the Valve Linearization Type cell, choose Single-Point.
3. In the Knee Command Voltage cell, enter the voltage value of the knee. This
voltage can be obtained from the valve data sheet. For example, in the Single-Knee
Valve diagram above, the voltage is 4 volts.
4. In the Knee Flow Percentage cell, enter the flow percentage of the valve at the
knee. This value can be obtained from the valve data sheet. For example, in the
Single-Knee Valve diagram above, the flow percentage is 10 %.
5. Download the changes and update Flash.
The valve linearization is applied only when the axis is in closed loop control.
Linear and Non-Linear Valves
Linear and non-linear refer to the flow versus command signal profile of a valve.
Linear Valves
Linear valves have a profile where the flow of the valve is linearly proportional to the
command signal input. The diagram should look like this:
88
Delta Computer Systems, Inc.