Delta RMC151 User Manual
Page 1191
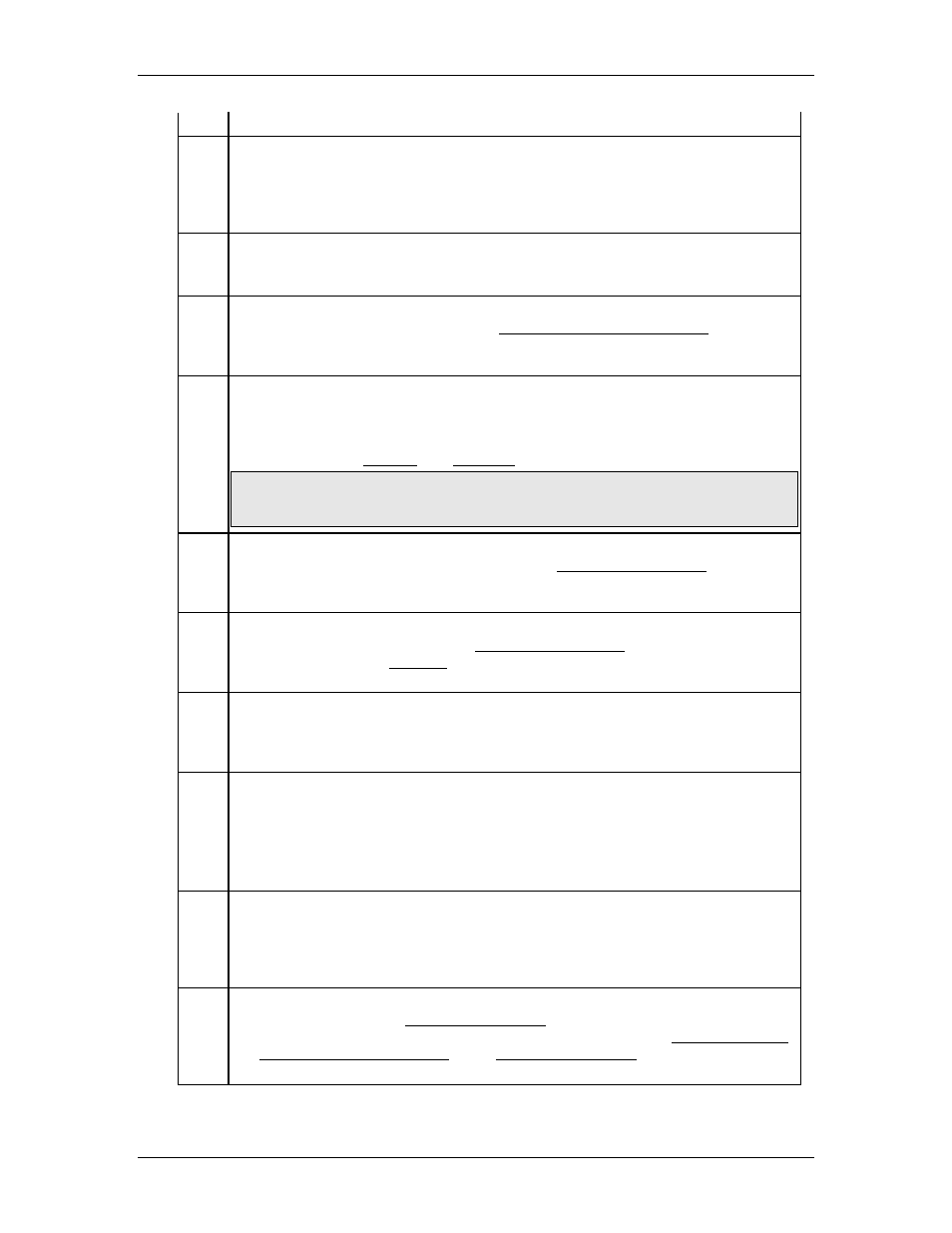
11 Troubleshooting
Endpoint Behavior set to Cyclic (+2) or Zero-Velocity (+0).
34
Curve Add failed because the curve queue is full.
Curve Add failed because the curve queue is full. The curve queue contains
the curves that are currently being added to the curve store. The curve
queue can handle up to 16 curves simultaneously. To prevent this error, wait
for a curve to be completely added before adding another curve.
35
Command is not supported by this RMC75S/RMC75P hardware revision.
The hardware revision of this RMC75S or RMC75P does not support this
command. You will need to obtain a newer RMC75S or RMC75P.
36
Cannot join a synchronized move in progress.
This error occurs when you issued a synchronized move command with a
group number that is already being used by another sync move in progress.
You must use another group number.
37
Cannot do a synchronized stop on a non-synchronized axis.
You issued a motion command with a Requested Position that was outside
the Positive or Negative Overtravel Limits. The requested position was
truncated at the limit or the current position, whichever is farther from the
limits. Check the Positive and Negative Overtravel limits.
Note:
If you want the axis to halt instead of moving to a truncated position, make
sure the Auto Stop on the Command Adjusted error bit is set to halt.
38
Cannot change the final position of a synchronized move in progress.
When a synchronized move is in progress, a sync move command with the
same group number can only be issued if the resulting final position will still
be the same.
39
Cannot start a synchronized move when the axis is moving.
An axis must be stopped when a sync move command is issued to it. In open
loop, this means the Stopped Status bit must be on. In closed loop control,
this means the Target Velocity must be zero.
40
Motion command ignored due to grouped halt.
This command error appears whenever, within the same command block, a
command in the same sync or halt group as the current axis had a command
error.
41
Program cannot run on selected task
This can occur either when a program has been set up to not run on this
particular task, or if it has been set to run on only one task at a time and is
already running on another task.
Refer to the User Program Properties dialog for each individual program to
view or change which tasks the user program is allowed to run on.
42
Position is too large relative to Position Unwind
This will occur when a rotary axis is commanded with a position that is on
the order of 16 million times the Position Unwind value. Beyond this point it
is not possible to properly unwind the value due to the maximum dynamic
range of floating point (REAL) values.
43
Command requires that the axis be following a curve move
This error occurs if the Change Master (79) command is sent to an axis on
which a curve move is not in progress (whether started with Curve Start (86)
or Curve Start Advanced (88)). The Change Master (79) command should
only be sent to an axis on which a curve move is in progress.
Command Modified Errors
deltamotion.com
1171