Link type - multiple axes in position, E.4.10 link type - multiple axes in position – Delta RMC101 User Manual
Page 908
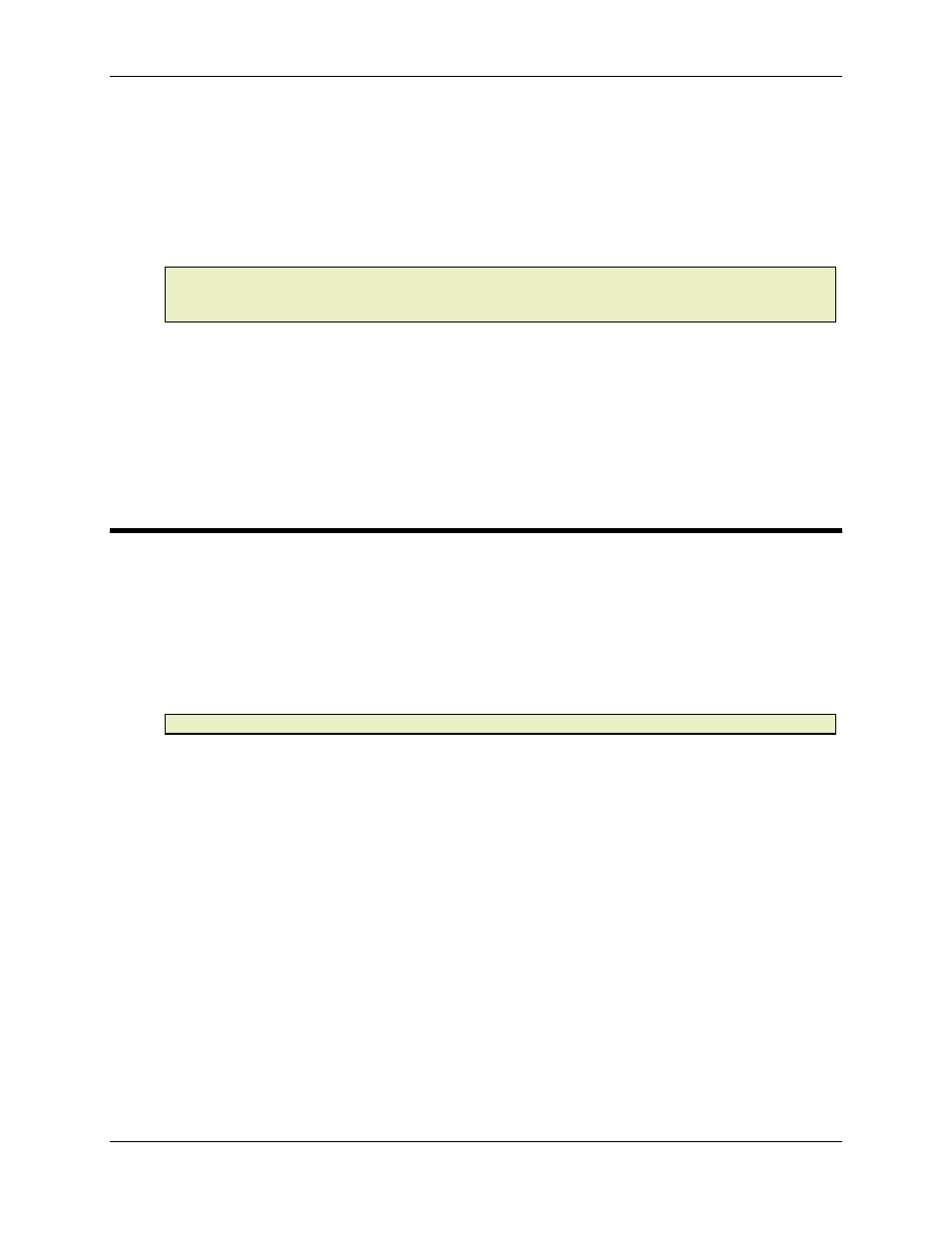
RMC100 and RMCWin User Manual
E-18
4. If you selected to jump on a comparison, then select the comparison type (=, <, >, etc.) and enter
the value to compare with.
5. If you selected a relational comparison (any comparison other than equal or not equal), then
select the type of the result and compare values (signed, unsigned, or position units).
6. If you selected a relational comparison for position values, then select the axis whose position
unit range you want to use.
Note:
This axis is encoded in bits 4-6 of the step's Mode word. Therefore, changing this value
will change the Mode for the event step. Ensure that this is acceptable for the command on that
event step. If it is not, then you will need to move the link type to another step.
Using without the Link Type and Link Value Dialog Box
1. In the Link Type field, enter one of the link types listed at the top of this topic. You must enter it in
hexadecimal.
2. For the MathERR and MathOK link types, enter 0 for the Link Value. Otherwise, enter the value
you want to compare with.
E.4.10 Link Type - Multiple Axes In Position
Link
Type:
AxesInPos (A, hex 0x41, dec 65)
Link
Value:
Bits 0-7 select axes to be monitored.
Range:
Any combination of bits 0-7. Bits 8-15 are reserved.
Note:
This feature is available only in RMC100 CPU firmware version 19990625 and later.
This link type waits for all selected axes to be either in position (for position axes) or at pressure
(for pressure axes) before going to the next step. This link type will work with both types at the
same time.
Example:
Link Type: AxesInPos (A)
Link Value: 0x000C
Link Next: 10
On a four-axis system this link would wait for the third and fourth axis to be in position before going to
step 10. On a two axis systems with two pressure channels this link would wait for the two pressure
channels to be at pressure before going to step 10. On a system with just two axes this would be a
mistake and the RMC would never link to step 10.
Why Bother?
This is a GREAT way to get axes synchronized at startup and other places within a machine
cycle.