Differential gain, C.2.10 differential gain – Delta RMC101 User Manual
Page 797
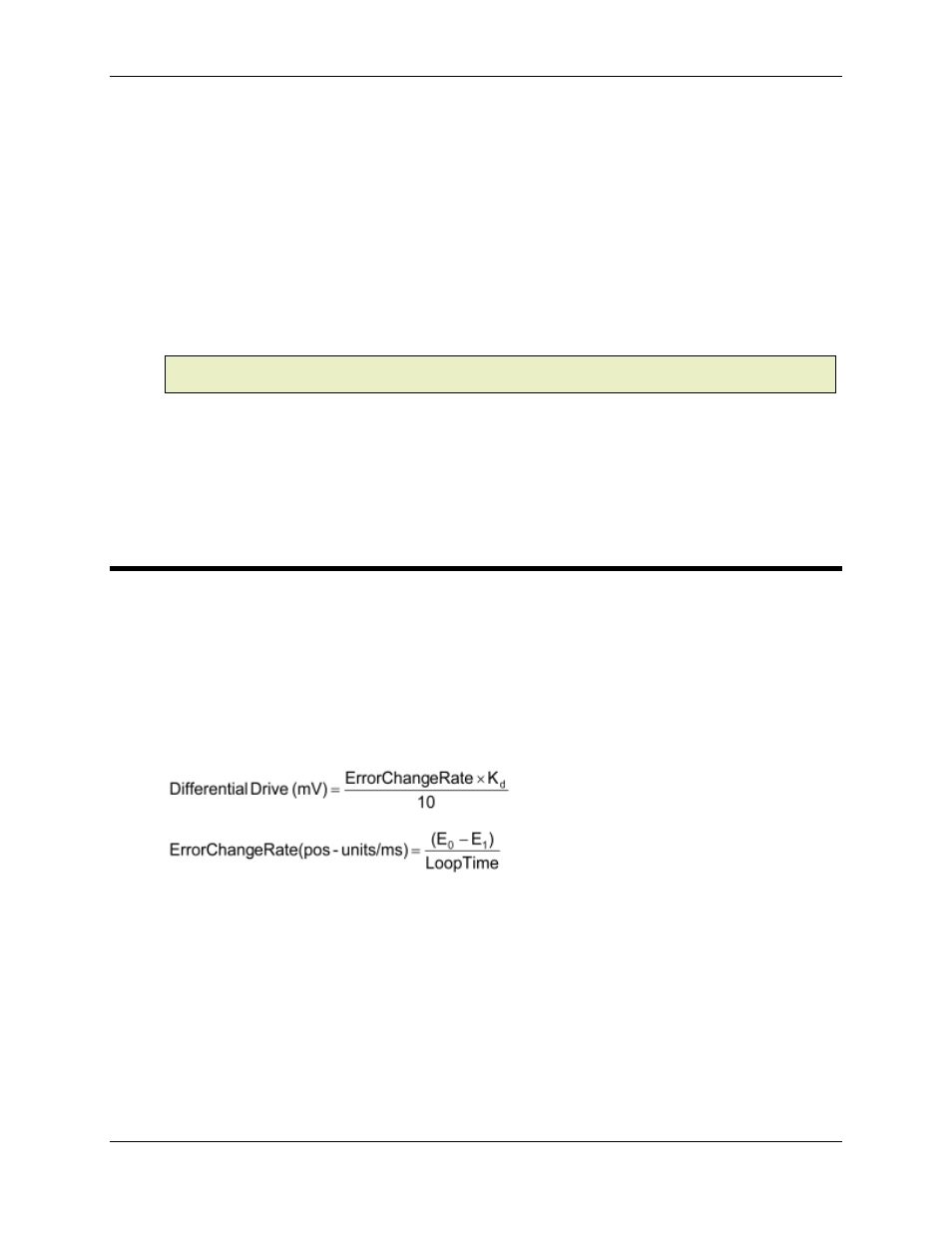
Appendix C: Parameter Field Reference
C-27
that you set the Integral Gain to a value of at least 50.
Integral Gain is defined as:
Integral Gain = millivolts per 10240 counts of accumulated Position Error
Integral Drive is defined as:
Integral Drive = Integral Gain x Accumulated Counts / 10240
Note:
The actual drive output may be reduced based on the values of the Extend Feed Forward
and Retract Feed Forward .
Why Bother?
Integral Gain should be used to compensate for the fact that loads may vary, valves are non-
linear and the axis may have trouble getting to the Command Position without Integral Gain.
C.2.10 Differential Gain
Default: 0
Range: 0 to 65535
The Differential Gain field is used to apply a gain based on the rate of change between the target
and actual positions. There are two ways to view this.
First, this is a gain multiplied by the current rate of change in the position error. The differential
drive, in millivolts is computed as follows:
where:
K
d
=
Differential Gain in mV/[pos-units/ms]
E
0
=
position error this control loop in position units
E
1
=
position error last control loop in position units
LoopTime =
RMC Control Loop Time in ms (1 or 2)
A second equivalent way of viewing this parameter is as the gain multiplied by the velocity error.
When looked at from this angle, the above equations become the following: