Sine move continuous command, A.1.56 sine move continuous command – Delta RMC101 User Manual
Page 693
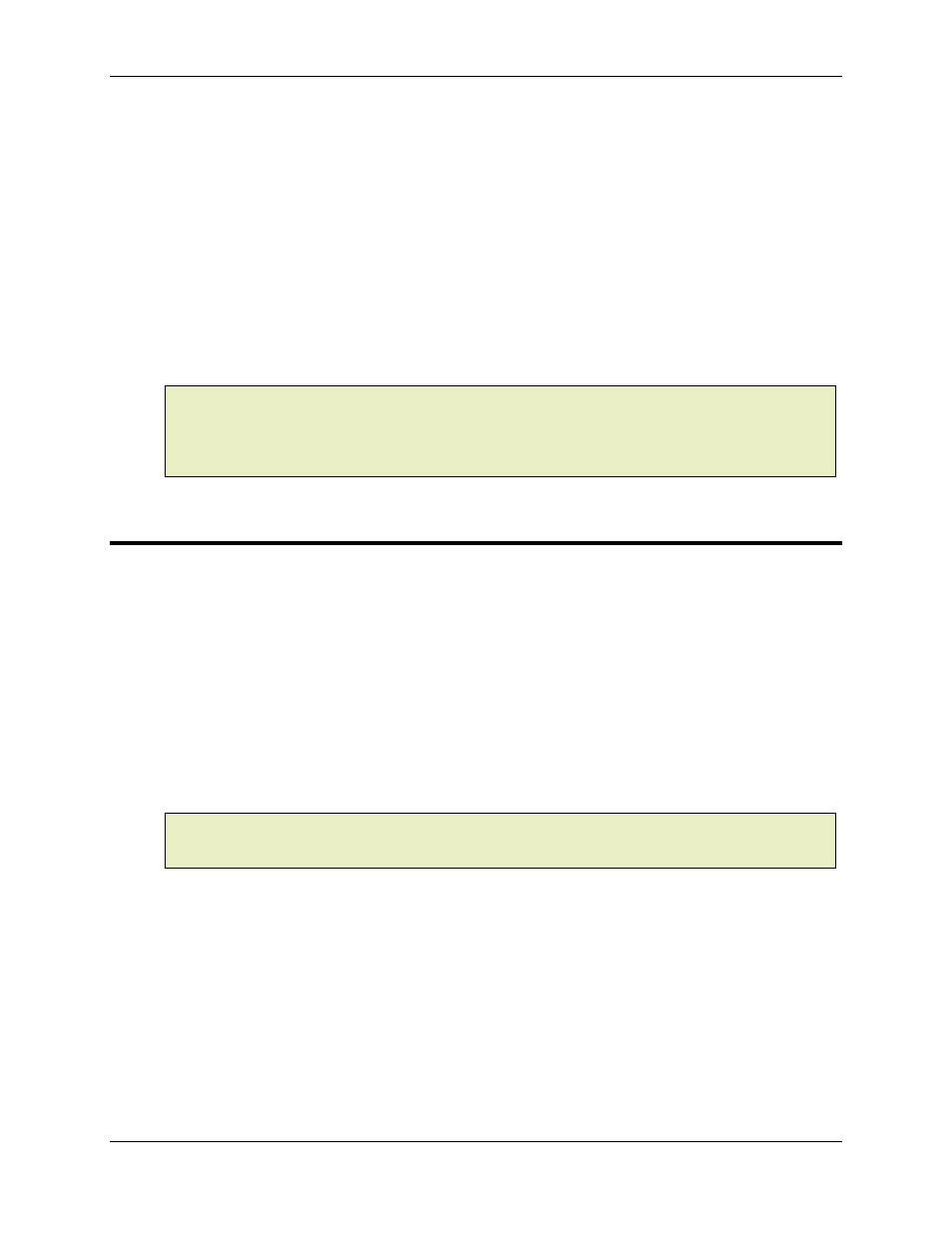
Appendix A: Command Reference
A-41
The 16-bit Command Value is split into two bytes. The upper 8 bits specify which bits are to be
cleared. For example, setting bits 8 and 10 of the Command Value would clear wait bits 0 and 2.
Likewise the lower 8 bits specify the bits to be set. It is possible to set and clear multiple bits with
just one command.
Example:
Axis 4 may need to know when axes 0 to 3 have cleared a position. The step sequence running
on Axis 4 would set wait bits 0 to 3 and then wait for axis 0 to 3 to clear their bit. When all four bits
are cleared then axis 4 would know it is safe to proceed. Axis 4 would use the check wait bits link
type to insure that wait bits 0 to 3 are cleared before proceeding. It is much easier for axis 4 to do
just one check for the 4 wait bits to be cleared than doing four individual enhanced links that
check axis 0 to 3's position one by one.
Note:
Wait bit 7 is used by the Profibus DP communications so the user can tell when spline
downloads are finished. The Profibus DP spline processing routine sets wait bit 7 when a
download to the spline area is detected. The bit is cleared when the download is done. The user
can then use the step table and the Check Wait Bits link to be sure the spline is ready before
executing the spline.
A.1.56 Sine Move Continuous Command
Character: none
Decimal: 48
Hexadecimal: 0x30
Command Value: Amplitude
This command moves the position, pressure or force axis in a sinusoid. The user specifies the
amplitude, frequency, and number of cycles (count). The count may be changed while the move
is in progress, but the amplitude and frequency should not be changed until the Sine Move
Continuous is complete. The Sine Move Continuous will stop at the starting position after
completing the specified number of cycles.
The cycling can be stopped by issuing a Sine Move Continuous command with the count set at 1.
When the actuator gets to the starting position the cycling will stop.
Note:
On pressure control axes, the axis must be in closed-loop pressure control when this
command is issued. If the pressure control axis is in open loop control when this command is
issued, a parameter error will result.
Command Value: Amplitude in position units. The current target position is used as a starting
point and the sinusoidal motion can go positive or negative from there depending on the sign of
the amplitude. For example: If the actuator is a 1000 and a sinusoidal command has an amplitude
of 100 then the actuator will cycle between 1000 and 1200. If the amplitude is –50, the actuator
will cycle between 1000 and 900.
Speed: Frequency in HZ x 100. This allows frequencies up to 655Hz but in reality it is hard to
attain. For example, 500 is 5 Hz, and 20 is 0.2 Hz.
Deceleration: Count. Enter 1-65535 for a set number of cycles. Enter 0 for continuous cycling.