Delta RMC101 User Manual
Page 192
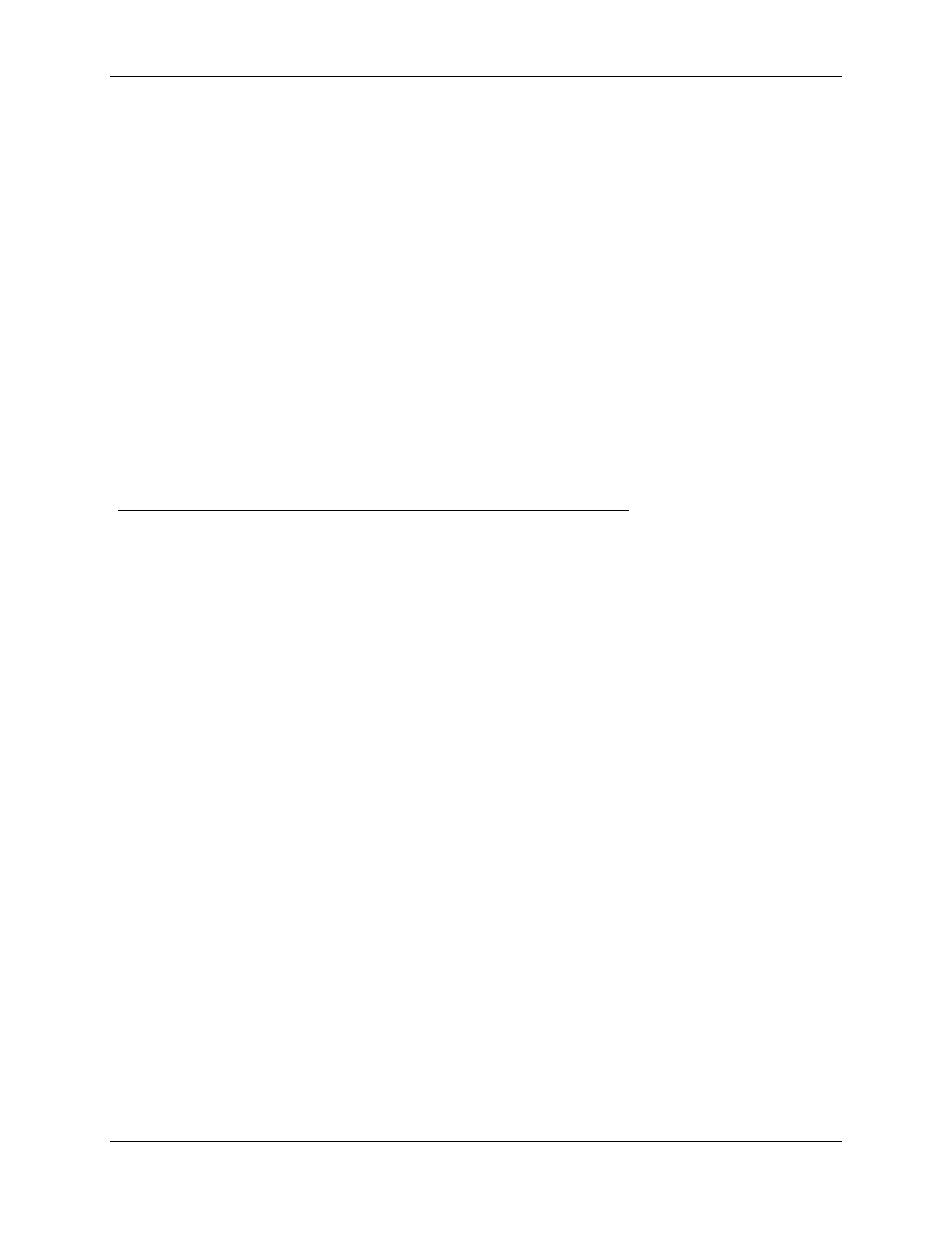
RMC100 and RMCWin User Manual
4-6
reach the requested gear ratio when the master is at 300 position units.
Note that if the axis is given this gearing command when the master axis is at a position less
than 300, the gearing will start instantaneously.
Mode 3 (Time):
The Acceleration field indicates the time in milliseconds that the ramp will take. The
Deceleration field is not used in this mode.
4. Issue the Command.
After the command parameters (Mode, Acceleration, Deceleration, Speed, and Command Value)
have been set up as described in the preceding steps, the Go (G) command can be issued.
Gear Ratio Status
State Bits A and B in the Status word are used to indicate the state of the gear ratio on the slave
axis in the following manner:
Gear Ratio State
Bit 5 (State
Bit B)
Bit 4 (State Bit
A)
At zero
0
0
Increasing
0
1
At Requested
Value
1
0
Decreasing
1
1
Limitations
Because both the Command Value and Speed fields, which make up the gear ratio, are limited to
–32,768 and +32,768, the number of teeth on the master and slave gear are likewise limited.
However the Speed field (denominator) of the slave axis cannot be zero. Also, be careful when
setting the number of master teeth larger than the number of slave teeth. It is possible to cause
the slave speeds to exceed 65,535 position units per second, which would cause the speed to
wrap and incorrect feed forward values to be calculated.
Example 1:
Axis 0
(Master)
Axis 1
(Slave)
Mode
0x0281
0x2001
Acceleration
100
50
Deceleration
100
50
Speed
10000
10000
Command
Value
0
5000
Command
G
G
In the gear master axis's Mode word, the Rotational and S-Curve bits are set to indicate that the
axis will control speed using S-Curved ramps. See Speed Control for details on this feature. Also
in its Mode word, the Acceleration and Deceleration Mode is selected as type 1. As a result the
axis will move continuously in the positive direction at 10,000 position units per second.