Delta RMC101 User Manual
Page 276
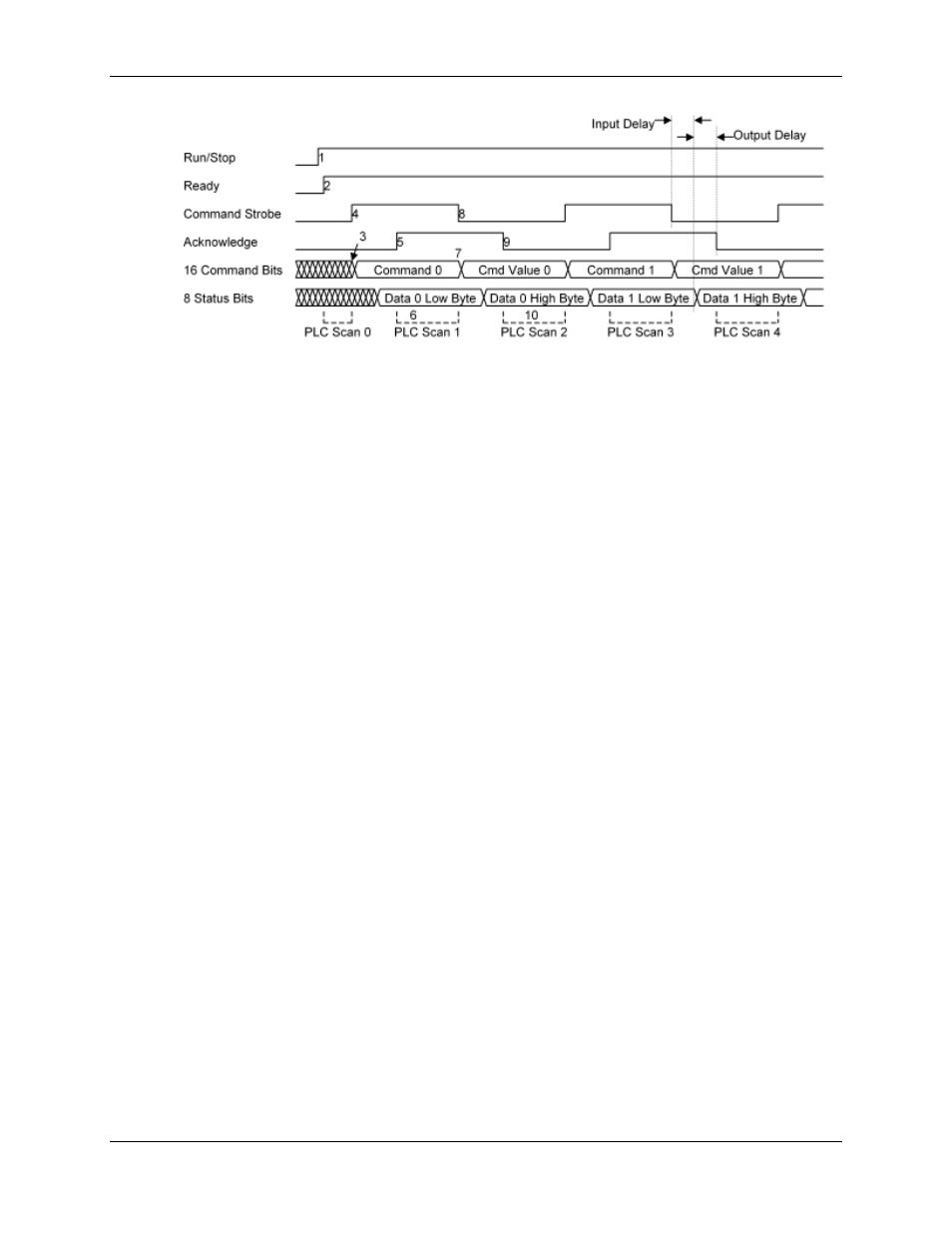
RMC100 and RMCWin User Manual
5-26
This process begins assuming that Run/Stop and Command Strobe are set low by the PLC. In
the steps below inputs and outputs are labeled as ”r;CPU” or ”r;DI/O”. These labels refer to the
CPU and DI/O modules of the RMC product, and not of the PLC:
1. Raise the Run/Stop (CPU input 0) line on the RMC. This is done on startup of the PLC.
2. Wait for the Ready (CPU output 0) line on the RMC to go high in response to the Run/Stop line.
This begins the first PLC scan.
3. Place the 16-bit Command on the RMC’s Command Bits (DI/O inputs 0-15).
4. Raise the Command Strobe (CPU input 1) line on the RMC. This ends the first PLC scan.
5. Wait for the Acknowledge (CPU output 1) line on the RMC to go high. This begins the next PLC
scan.
6. Read the low byte of the data requested by the command from the Status Bits (DI/O outputs 0-7)
on the RMC.
7. Place the 16-bit Command Value on the RMC’s Command Bits.
8. Lower the Command Strobe on the RMC. Then ends the next PLC scan.
9. Wait for the Acknowledge line on the RMC to go low. This begins the next PLC scan.
10. Read the high byte of the data requested by the command from the Status Bits on the RMC.
The process then repeats from step 3 with the next command.
In the above timing chart, notice two time durations are marked: Input Delay and Output Delay.
These intervals can be set using RMCWin to any value between zero and twenty milliseconds.
Input Delay indicates how long the RMC waits after seeing the Command Strobe toggle before
reading the command data. Change this setting to account for the PLC outputs’ and the RMC
inputs’ settling time.
Output Delay indicates how long the RMC waits after writing the requested data before toggling
the Acknowledge line. Change this setting to account for the RMC outputs’ and the PLC inputs’
settling time.
To configure Command mode, do the following:
• Connect the serial port to the module being configured.