Status (pressure/force), D.3.4 status (pressure/force) – Delta RMC101 User Manual
Page 886
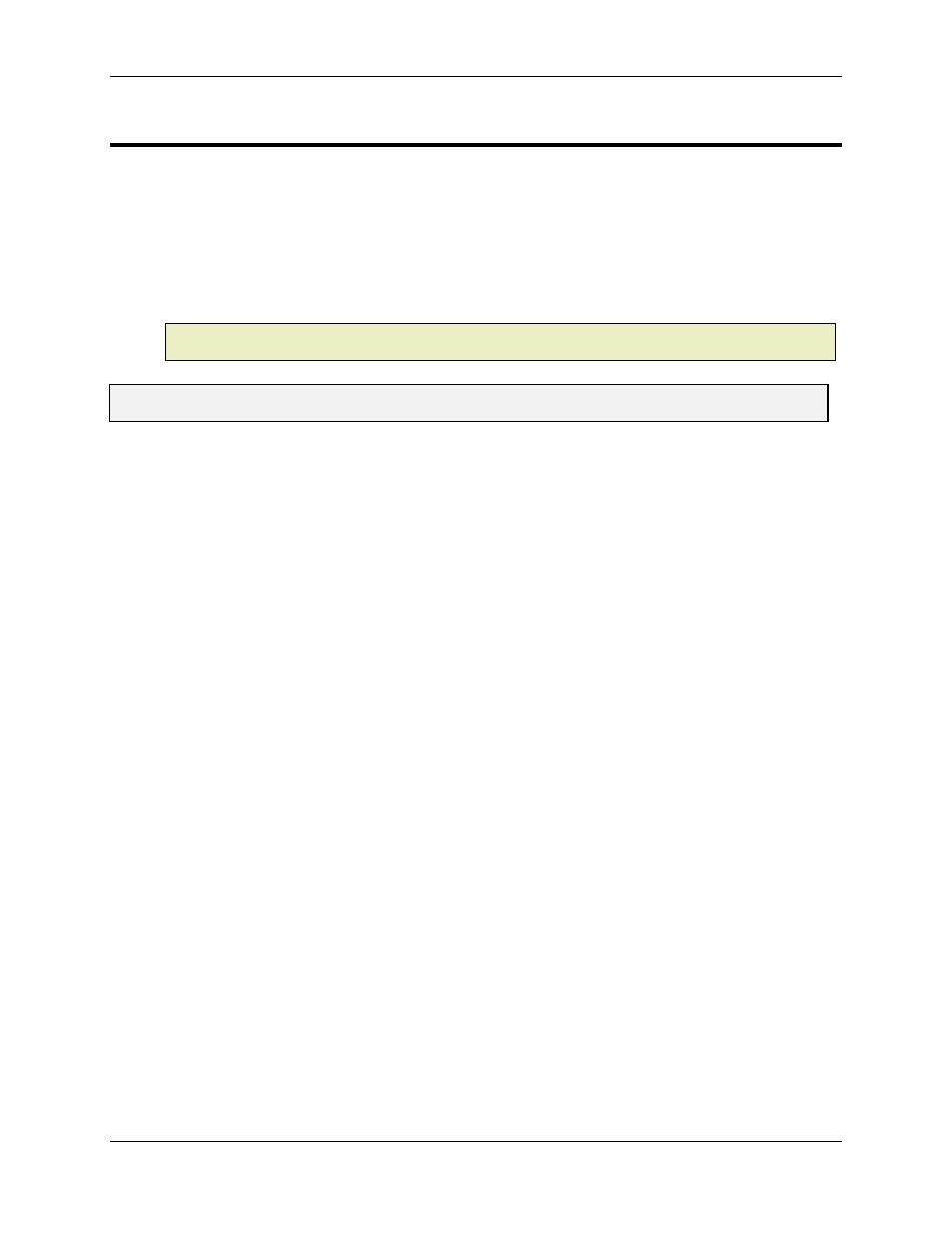
RMC100 and RMCWin User Manual
D-24
D.3.4 Status (Pressure/Force)
The pressure Status word contains 16 bits of information about the condition of the axis. You can
use any of the first eight error bits to trigger a STOP on the axis using the Auto Stop parameter.
To display the expanded Status bit window, see Using the Status Bits Window, or click here for
the Axis Status Bit Map.
Error bits 8 through 14 are cleared whenever a Set Pressure (^) command is given. Error bit 15 is
cleared after a Set Parameters (P) command if a transducer is detected at that time.
Note:
Bit 15 is the most significant bit (MSB; left-most bit), Bit 0 is the least significant bit (LSB,
right-most bit).
Tip:
On the Window menu, click Status Bits (or press CTRL+B) to display the Bit Status window, which
shows the individual bits of the Status words.
Bit 15 - No Transducer
This bit is set if the transducer falls into a range which indicates that no transducer is connected.
In all voltage modes, this occurs if the COUNTS read -32768. In 4 to 20mA mode, this occurs if
the COUNTS read below 5898, which represents 3.6mA. This bit causes a Hard Stop or a Soft
Stop, depending on the setting of Auto Stop bit 7. This bit will stay on until a new command is
given to the axis.
Bit 14 - Transducer Noise
This bit is currently unused for analog transducers.
Bit 13 - Transducer Overflow
This bit indicates that the analog input is being over-ranged. Ensure that the analog input is
between the range selected in the Configuration Word. For example, if the range selected is
between 0 and 10V, and the input voltage is 12V. See Counts for a list of the actual count ranges.
Bit 12 - Overdrive
This bit is only used with 16-bit analog modules that have drive outputs. This bit is set when this
drive output exceeds the 12-bit range of the D/A converter. This drive output can only be set by
using the Open Loop command, and therefore this bit is not affected by the axis regulating
pressure. The module will truncate the drive to 12 bits (+10V or -10V). It causes no action, a Soft
Stop, or a Hard Stop, depending on the setting of Auto Stop bits 4 and 12. This bit will stay on
until a new command is given to the axis. Because the drive output on the analog module
generally does not have anything to do with regulating the pressure or position, it is
recommended that no Auto Stop bits be set for this error.
Bit 11 - Parameter Error
This bit is set when an initialization parameter or control parameter is out of bounds. In some
cases one parameter's limit will depend on the value of another parameter, so definite limits may