Delta RMC101 User Manual
Page 279
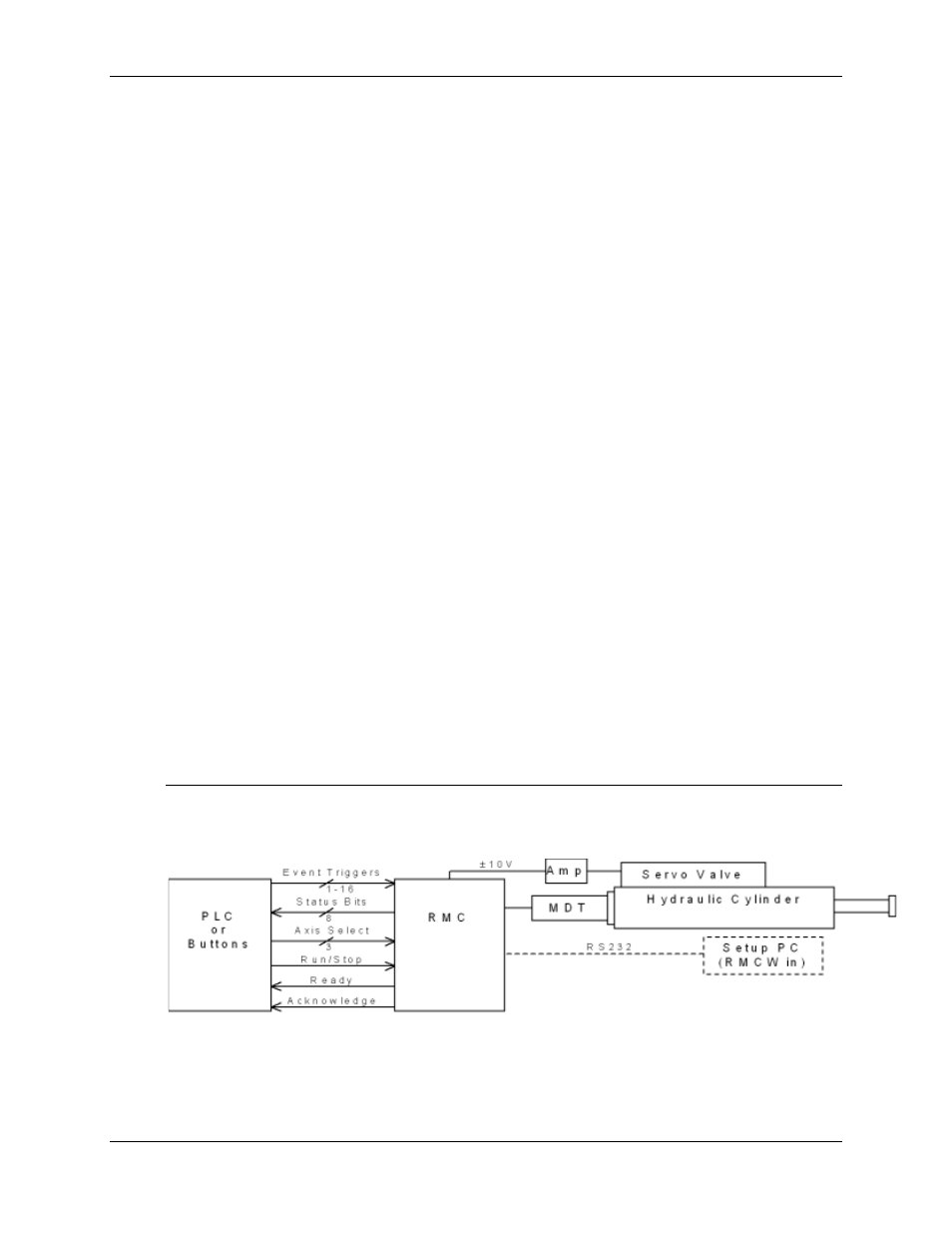
Digital I/O 5.1
Communications
5-29
Event Mode
• Multiple axes may be
given commands from a
single input
• Allows use of Event
Control feature
Bit—indicating an error
has occurred—and an In
Position Bit per axis
• Issues only Start Event
commands
Parallel
Event Mode
• Up to four axes may be
commanded at once
• PLC or thumb-wheel
switches may be used
• Allows use of Event
Control feature
• Requires parallel inputs
• Returns only a Halted
Bit—indicating an error
has occurred—and an In
Position Bit per axis
• Sequence must be pre-
programmed in Event
Control
Parallel
Position
Mode
• Any position can be
moved to in a single
PLC scan
• Any open loop drive can
be triggered in a single
PLC scan
• Multiple profiles can be
selected for any move
• Requires a PLC
• Returns only a Halted
Bit—indicating an error
has occurred—and an In
Position Bit per axis
• Issues only Go and
Open Loop commands
• Gives commands to only
one axis per scan
Command
Mode
• Any RMC command can
be issued
• Any status information
can be retrieved
(including Actual
Position, Actual Speed,
Drive, Error Bits, and
other Status Bits)
• Requires a PLC
• Requires 2 PLC scans
per command
• Gives commands to only
one axis per command
cycle
Implementation
The following diagram shows the electrical control connections of a single-axis hydraulic system
using RMC-DI/O in Input to Event Mode (the PC and its RS232 cable are needed only during
setup):
This document discusses only the connections between the Programmable Controller and the
RMC. For details on the transducer and drive wiring, look up Wiring Notes in the RMCWin index.
Input to Event mode requires use of the Event Control feature of the RMC. You should first
familiarize yourself with Event Control and the Event Step table. The RMCWin online help is a