Delta RMC101 User Manual
Page 887
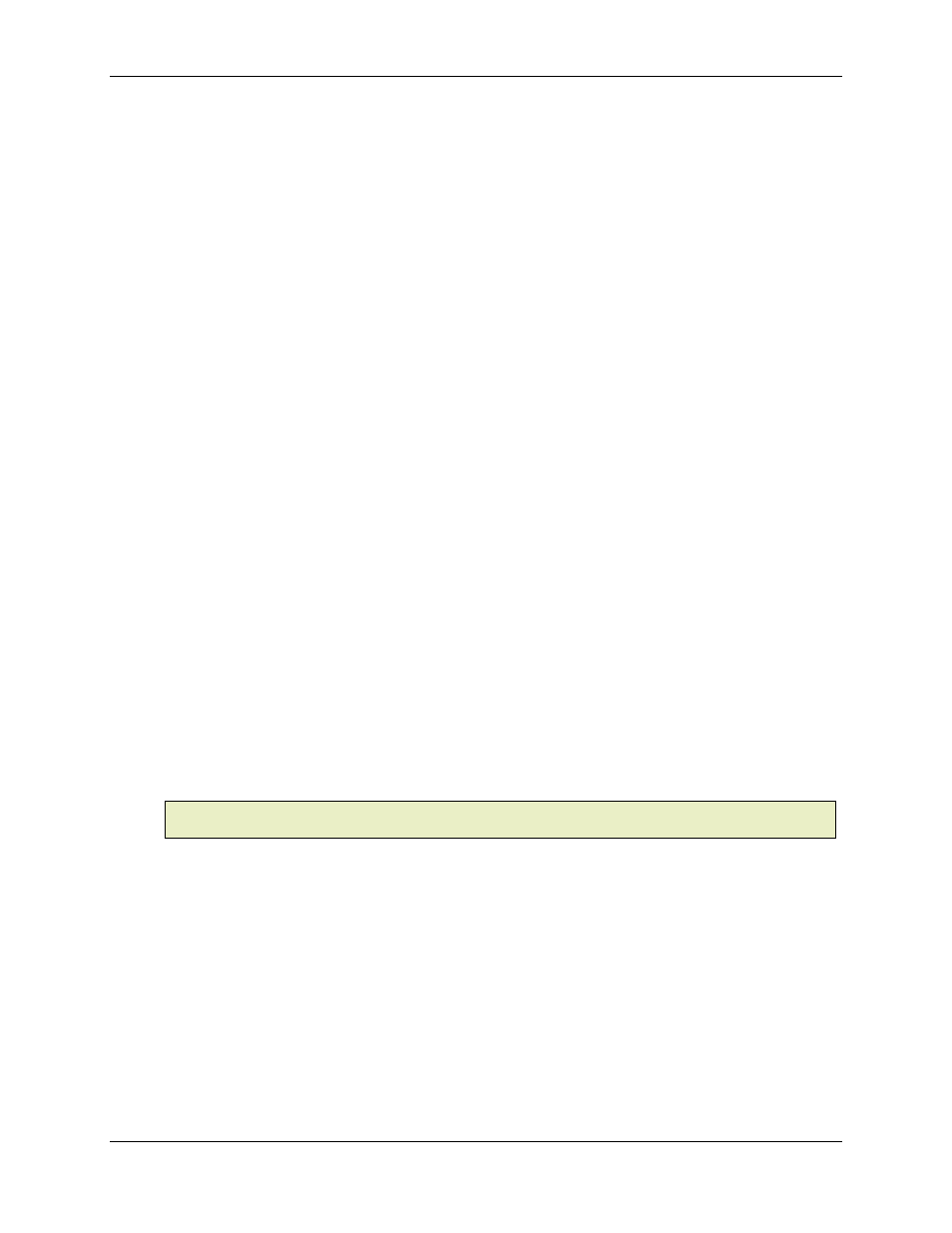
Appendix D: Status Field Reference
D-25
not always be available. However, the motion controller does try to replace the erroneous value
with another that is within range, so the offending parameter can be determined by comparing the
parameter values before and after the error bit is set. This error causes no action, a Soft Stop, or
a Hard Stop, depending on the setting of Auto Stop bits 3 and 11. This bit will stay on until a new
command is given to the axis.
Bit 10 - Pressure Overflow
This bit indicates that the pressure read from the transducer does not fit within a 16-bit number.
For single-ended analog axes, an overflow is not possible because the counts never exceed 16-
bits. For differential analog axes, because one 16-bit number is subtracted from another, the total
range is 17 bits, and therefore an overflow can occur. It causes no action, a Soft Stop, or a Hard
Stop, depending on the setting of Auto Stop bits 2 and 10. This bit will stay on until a new
command is given to the axis.
Bit 9 - Integrator Windup
This bit is set when the integrator value is larger than 20% or 80%, depending on the setting of
the Integrator bit in the Configuration word. It causes no action, a Soft Stop, or a Hard Stop,
depending on the setting of Auto Stop bits 1 and 9. This bit will stay on until a new command is
given to the axis.
Bit 8 - Following Error
This bit is set when the difference between the Target Pressure and the Actual Pressure is
greater than the Following Error parameter. It causes no action, a Soft Stop, or a Hard Stop,
depending on the setting of Auto Stop bits 0 and 8. This bit will stay on until a new command is
given to the axis.
Bit 7 - Acknowledge
This bit will toggle after the motion controller receives a valid command or Status Area Request.
This can be used to verify that the motion controller has received the command.
Note:
This bit only toggles on commands received from the Programmable Controller and
therefore will not toggle on commands from RMCWin.
Bit 6 - Initialized
This bit is set after a Set Parameter (P) command is successfully executed. Until this bit is set,
the axis will not regulate pressure. This bit is cleared when the module is reset.
Bit 4-5 - State Bits
Bits 4 and 5 show the state of the target generator:
STATE
Bit 5 (State Bit
B)
Bit 4 (State
Bit A)