Ssi wiring, Ssi wiring -68, 2 ssi wiring – Delta RMC101 User Manual
Page 612
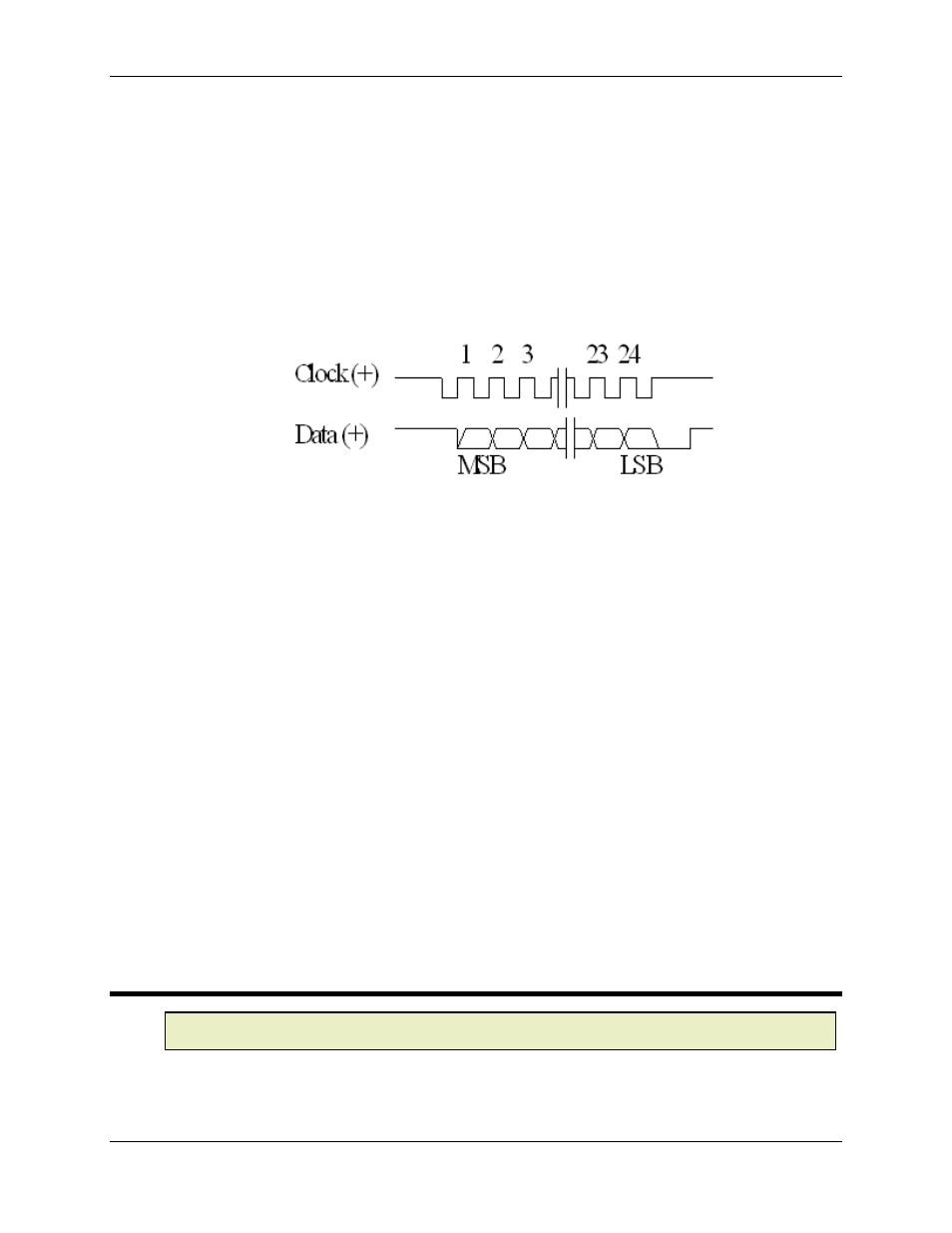
RMC100 and RMCWin User Manual
6-68
• Transmission rate independent of data length and resolution
• Transmission over long distances
• Direct connection to the RMC’s SSI interface module
Each RMC100 SSI interface module has circuitry for two SSI transducers. Each axis can be
configured independently for different types of SSI transducers. To read an SSI position, the RMC
sends clock pulses to the transducer, and on each rising edge of the +Clock signal, the SSI
transducer places one bit of the digital position on the +Data and Data signals. The most
significant bit is sent first. Below is shown a 24-bit SSI reading:
SSI Transducer
The RMC must then convert the counts returned from the transducer to an Actual Position in
user-defined Position Units (usually 0.001 inch or 0.1 mm) for use in the PID control loop.
Synchronized SSI for MDTs
For motion control, MDT (Magnetostrictive Displacement Transducer) type transducers with SSI
output must be of the Synchronized type. This ensures that the time between position samples
matches the control loop time of the RMC controller. If the transducer is not synchronized, the
sample time may not match and will adversely affect control. Make sure to specify that the
transducer be of the synchronized type.
Synchronized SSI is not an issue for encoders.
See also:
SSI Wiring
SSI Configuration
SSI LED Indicators
SSI Specifications
6.6.2 SSI Wiring
Note:
When positive voltage is sent to an axis’s drive, the axis must extend. The extend
direction is defined as the direction that causes the transducer to return increasing counts.
Use shielded twisted pairs for all connections to inputs and outputs. Route the transducer wiring
separate from other wiring. You must provide the power supplies needed by your transducers.