Delta RMC101 User Manual
Page 599
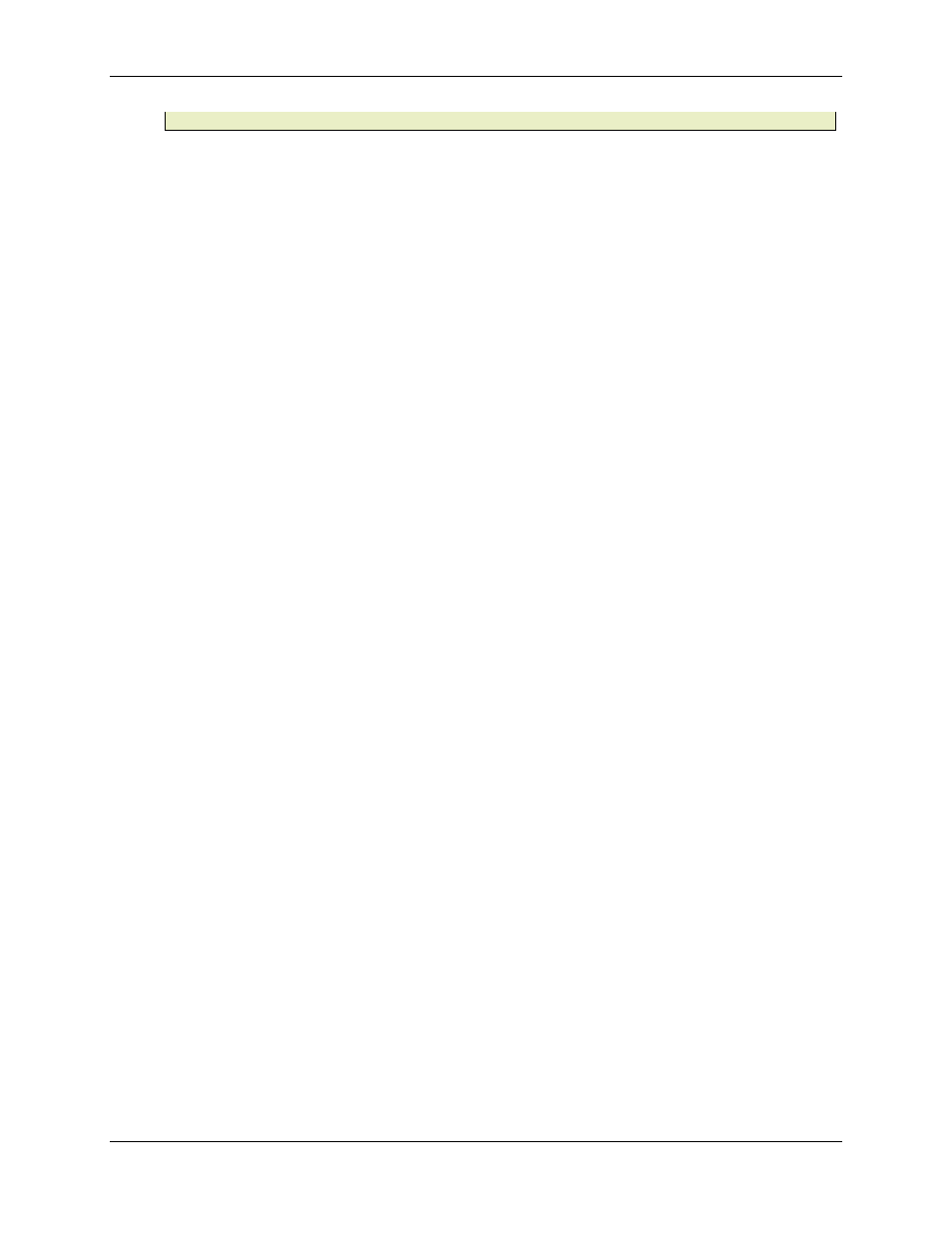
Quadrature with Stepper Output 6.4
Transducer Interface Modules
6-55
Following Error from being generated.
There are several of ways that these scales can be set up. The following examples illustrate the
potential uses of these scale parameters.
Example 1:
The user has a 100-line encoder, a 1.8°-per-step (200 steps per revolution) motor, and a stepper
drive configured to use half steps. The encoder is mounted on the same shaft as the stepper
motor, so each will turn one revolution in the same amount of time.
The user chose these devices so that the number of quadrature counts per revolution is equal to
the number of half steps per revolution, and wishes to use the raw counts as position units. That
is, because the stepper drive uses half steps there are 400 steps per revolution to match the 400
quadrature counts per revolution on the 100-line encoder.
Therefore, the ratio of steps to counts to position units is 1:1:1. The following parameters achieve
this:
Parameter
Value
Steps/Rev
400
Position Units/Rev
400
Quad Counts/Rev
400
Example 2:
The user has a 256-line encoder, a 7.5°-per-step (48 steps per revolution) motor, and a full-step
stepper drive. Therefore, the encoder generates 1024 quadrature counts per revolution. The
encoder is mounted on the same shaft as the stepper motor, so each will turn one revolution in
the same amount of time. The user wants positions to be given in degrees, so we will have 360
position units per revolution.
In this example, we simply enter the following values direct from our calculations above:
Parameter
Value
Steps/Rev
48
Position Units/Rev
360
Quad Counts/Rev
1024
Therefore, each quadrature count will affect the actual position by 360/1024 of a position unit.
Each target position unit causes 48/360 of a step. Notice that this means that it takes 7.5 position
units to get one step output. This would need to be taken into consideration when the Following
Error Window parameter is set.
Example 3:
Suppose we have the same motor, drive, and encoder as in the previous example: the stepper
has 48 steps per revolution, and the encoder has 256 lines. However, this time the stepper motor
is on shaft A and the encoder is on shaft B. Shaft A must turn 15 revolutions in order to turn shaft
B one revolution; the gear ratio is 1:15. The user wishes to measure positions in degrees on shaft
B.
Therefore, we define a revolution as one turn of shaft B. This means we have 1024 quadrature
counts per revolution of our 256-line encoder, and 360 position units per revolution. Calculating
the number of steps per revolution of shaft B requires multiplying by the gear ratio between shaft
A to shaft B: