Tuning a position-pressure system, Tuning a position-pressure system -12, 4 tuning a position-pressure system – Delta RMC101 User Manual
Page 40
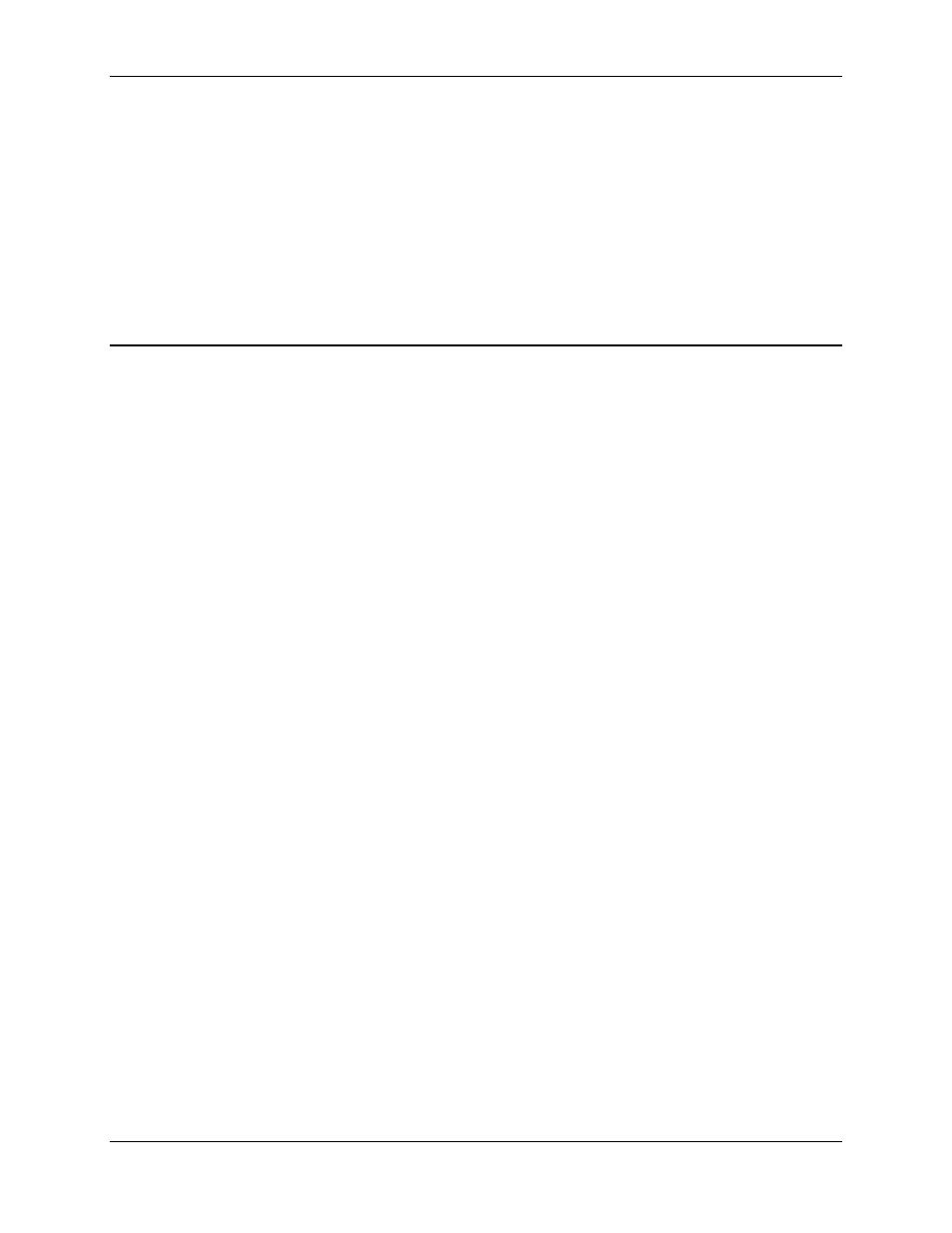
RMC100 and RMCWin User Manual
2-12
• If the Drive is not high, the gains can probably be increased for better control. If the Drive is
too high, or an overdrive error occurs, the system is not capable of performing the requested
move. The Speed, and/or Accelerations may need to be decreased.
• If the system vibrates while in position, the Dead Band value may need to be increased.
The final tuning of the system should be made at the speed of intended operation.
2.2.3.4 Tuning a Position-Pressure System
The following procedure may be used to tune a system that transitions from position control to
pressure control.
Please read the following topics before performing the tuning procedure:
• Tuning Overview
• Position/Pressure Overview
• Position/Pressure Setup
• Position/Pressure Example
There is no substitute for experience when tuning an axis. This procedure offers some guidelines,
tips, and suggestions for tuning your system. While these steps will work for some systems, they
may not be the best for a particular system.
Position/Pressure Tuning Procedure
1. Tune the Position Gains
The position gains should be tuned before attempting to tune the axis for pressure. Obtaining
control of the axis' position greatly simplifies the tuning of the pressure gains. If you have not yet
tuned the position gains, follow the procedure outlined in Tuning a Position Axis before
continuing.
2. Set Null Drive.
When the axis is holding position (stopped) in closed loop, issue a Set Null Drive to Integral Drive
(n) command. For best accuracy, this should be done after the axis has been in position for a
while, such as 1 second.
The null drive is the drive required to hold the axis in position. In some systems, such as
hydraulics with servo valves, this value may change with time. Therefore, this step should be
performed periodically.
For the remainder of the tuning procedure, use an Event Step sequence as described in the
Position/Pressure Setup topic and illustrated in the Position/Pressure Example.